Курсовая работа: Система управления ГПМ на базе 4-координатного многоцелевого фрезерного станка с ЧПУ для изготовления корпусных деталей
Описание
Руководитель курсового проекта: Мещерякова В. Б.
РПЗ + 5 листов А1
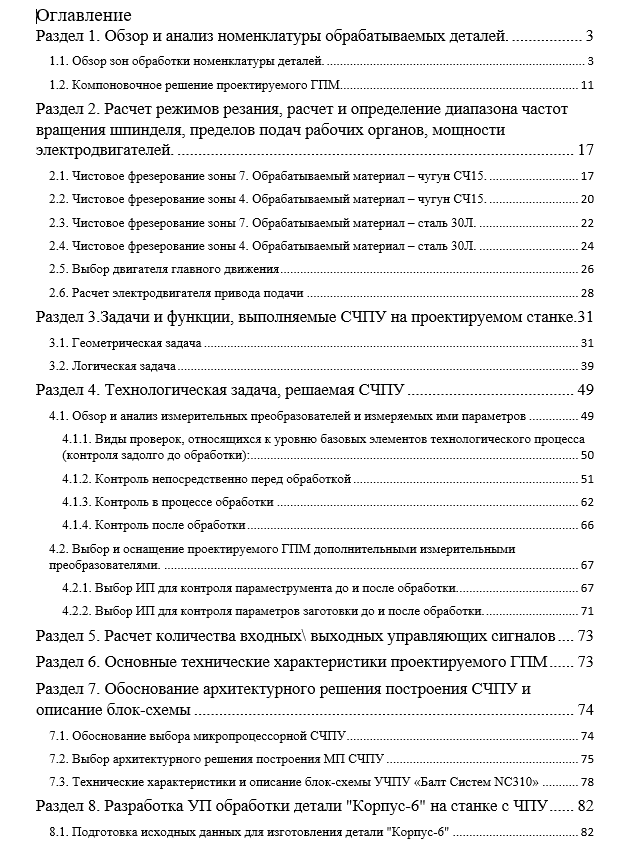
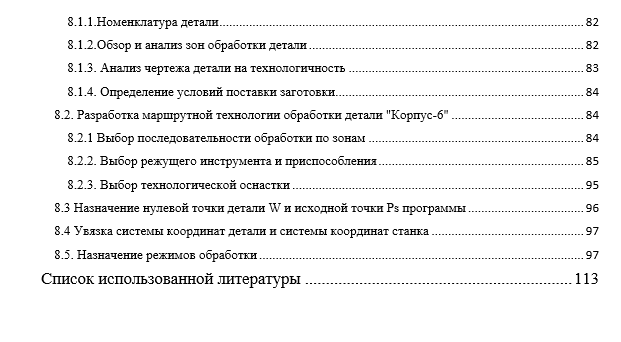
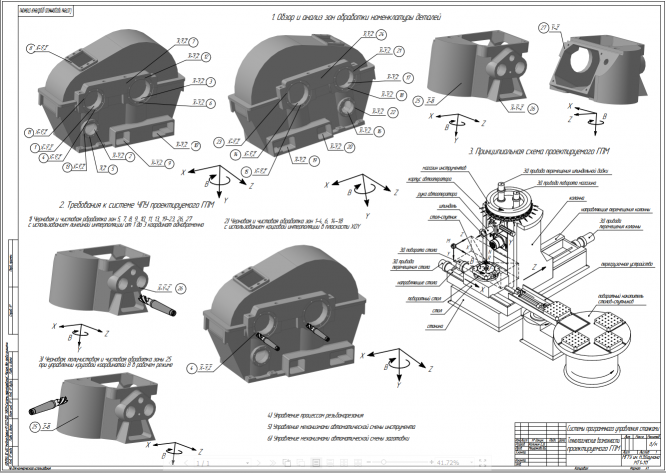
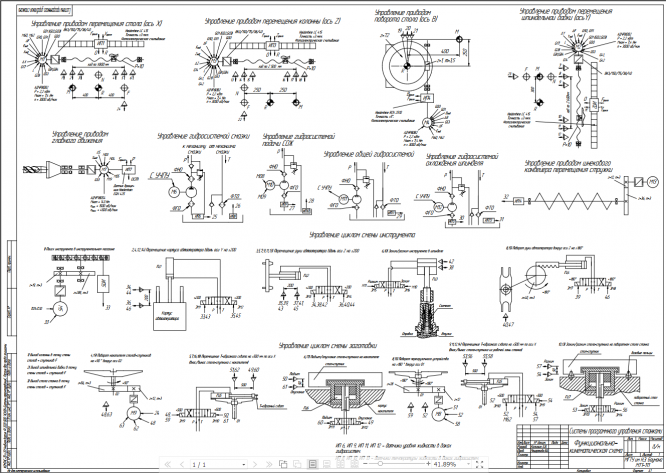
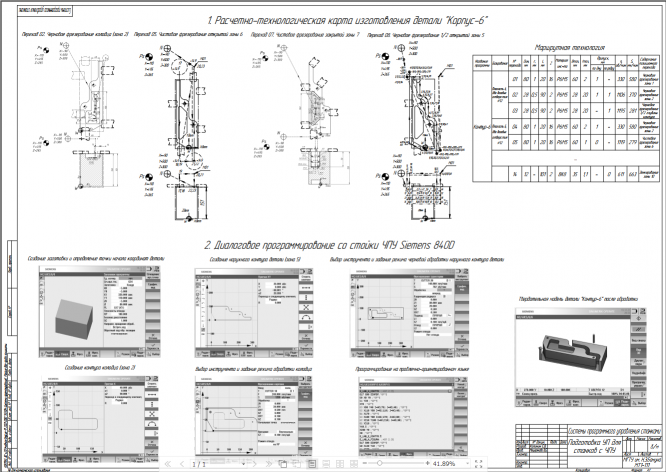
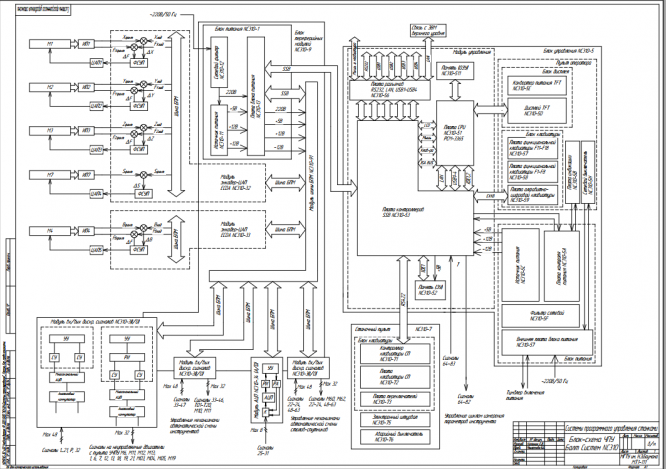
Вывод: для обработки приведенной номенклатуры деталей требуются следующие технологические возможности СЧПУ проектируемого ГПМ:
- черновая и чистовая обработка зон 8-10, 19, 20, 26, 27 с использованием линейной интерполяции от одной до трех координат одновременно;
- черновая обработка зон 1-4, 6, 14-18 с использованием круговой интерполяции в плоскости XOY;
- черновая, получистовая и чистовая обработка зон 1-7, 9-24, 26, 27 при управлении круговой координатой B в режиме позиционирования ;
- черновая, получистовая и чистовая обработка зоны 25 при управлении круговой координатой B в рабочем режиме;
- управление процессом резьбонарезания;
- управление механизмами автоматической смены инструмента;
- управление механизмами автоматической смены заготовки.
1.2. Компоновочное решение проектируемого ГПМ
В качестве базы для построения многоцелевых станков обычно используют компоновки станков фрезерной и сверлильно-расточной групп.
Многообразие возможных компоновок проектируемого станка обусловлено характером формообразования на металлорежущих станках, выполняемого посредством относительных движений заготовки и инструмента. Одно и то же относительное движение формообразования может быть реализовано при различном расположении подвижных блоков компоновки относительно друг друга и стационарного блока, то есть число возможных вариантов компоновки напрямую связано с количеством движений, предусмотренных в станке.
Для компоновок крупных многоцелевых станков характерно наличие подвижной стойки (колонны, портала) как элемента несущей системы, обеспечивающей значительные вертикальные перемещения блоков. Стойки всегда размещают в ветви перемещения инструмента, так как поднимать крупную заготовку труднее, чем инструмент. Соответственно, блоки, относящиеся к заготовке, вертикальных перемещений иметь не будут.
Во избежание влияния массы заготовки при горизонтальных перемещениях узлов, стол станка должен иметь не более одного горизонтального перемещения, а сам горизонтально-подвижный блок должен примыкать к стационарному блоку (станине) станка.
Для уменьшения вертикально-перемещаемых и консольных масс, вертикально-подвижный блок должен быть замыкающим в цепи инструмента.
На рис. 5 представлены возможные компоновки проектируемого станка из числа получивших широкое применение в станкостроении, в частности, в качестве базы для многоцелевых станков. Сведения о соответствии этих компоновок указанным выше условиям приведены в таблице 2.
Рис. 5.
Табл.2
Краткая формулировка условия отбора | Номер компоновки согласно рис. 5 | |||||||
1 | 2 | 3 | 4 | 5 | 6 | 7 | 8 | |
Отсутствие влияния массы заготовки при вертикальном движении | + | + | + | + | + | + | + | - |
То же, при горизонтальном движении | + | + | + | + | - | - | - | - |
Отсутствие влияния массы узлов при продольном движении | + | + | + | + | - | + | - | - |
Возможность увеличения аксиального хода для упрощения процесса автоматической смены инструмента | - | + | + | - | - | - | - | - |
Уменьшение влияния температурных деформаций шпиндельного узла | + | + | + | + | - | - | + | - |
Уменьшение вертикально-подвижных и консольных масс. | - | + | - | - | + | + | - | - |
Распределение масс между двумя ветвями компоновки | + | + | + | - | + | + | + | - |
Возможность встраивания в автоматическую линию | - | + | + | + | - | - | - | - |
В наименьшей степени условиям отбора удовлетворяет компоновка 8. Наиболее подходящими являются компоновки 2 и 3, однако наличие у станка компоновки 3 дополнительного установочного движения шпинделя для фиксации его в определенном угловом положении позволяет расширить спектр выполняемых операций обработки.
Основные конструктивные особенности проектируемого ГПМ, исходя из требований, предъявляемых необходимостью обработки детали "Крышка":
- Станок должен быть изготовлен в одношпиндельном исполнении. Для выполнения операций резьбонарезания метчиками шпиндель станка может автоматически реверсироваться.
- Автоматическая смена инструмента осуществляется посредством автоматической разгрузки и загрузки шпинделя оправками с инструментом из магазина с помощью автооператора.
- Для последовательной обработки деталей с разных сторон станок снабжен прецизионным поворотным столом, способным поворочиваться на угол, заданный программным управлением.
- Для совмещения времени установки новых заготовок с основным временем работы станок оснащен дополнительными загрузочными позициями и специальным автоматическим устройством смены заготовки.
- Для увеличения числа операций обработки за одну установку, применена горизонтальная компоновка станка. Применение с этой же целью делительных устройств на столах многоцелевых станков вертикальной компоновки снижает жесткость системы станок-приспособление-инструмент-деталь.
Принципиальная схема ГПМ с указанием его рабочих органов, управляемых СЧПУ по соответствующим необходимым координатам; расположения инструментального магазина, перегрузочных устройств представлена на рис. 6. Управляемые координаты указаны стрелками на рабочих органах станка.
Присоединительные размеры стола-спутника станка приведены на рис. 7.
Схемы перегрузочного устройства и цикла смены стола-спутника приведены на рис. 8 и рис. 9 соответственно.
Рис. 6
Рис. 7
Рис. 8
Рис. 9
Раздел 2. Расчет режимов резания, расчет и определение диапазона частот вращения шпинделя, пределов подач рабочих органов, мощности электродвигателей.
Назначение режимов обработки проведем по справочнику [2] для наиболее и наименее нагруженных переходов для разных обрабатываемых материалов: чугун СЧ15 ГОСТ 1412-85, сталь 30Л ГОСТ977-88. Наиболее нагруженным переходом является чистовое фрезерование зоны 7, наименее нагруженным – чистовое фрезерование зоны 4.
2.1. Чистовое фрезерование зоны 7. Обрабатываемый материал – чугун СЧ15.
Исходные данные для расчета:
Инструмент – фреза торцевая диаметром 40 мм с механическим креплением твердосплавных пластин с износостойким покрытием (марка твердого сплава ВК6, количество пластин 8), с главным углом в плане 75°.
Период стойкости инструмента T = 60 мин.
Ширина фрезерования B = 35 мм. Глубина фрезерования t = 5 мм соответственно.
Материал – чугун СЧ15. Твердость HB не более 2200 МПа (ГОСТ 1412-85).
Рекомендуемое значение подачи на зуб:
где – подача на зуб в зависимости от обрабатываемого материала, диаметра и числа зубьев фрезы, ширины и глубины фрезерования, а также от жесткости системы станок — приспособление — инструмент —деталь (группа подач I – фрезерование жестких деталей закрепленных непосредственно на столе станка, при небольших вылетах фрез);
– коэффициент твердости обрабатываемого материала;
– коэффициент материала режущей части;
– коэффициент главного угла в плане;
– коэффициент способа крепления пластины и наличия покрытия;
– коэффициент схемы установки фрезы (симметричная);
– коэффициент отношения фактической ширины фрезерования к нормативной (120 мм);
– коэффициент группы обрабатываемого материала.
Подача на оборот:
где – количество зубьев фрезы.
Значения скорости и мощности резания:
где – скорость (м/мин) и мощность (кВт) резания в зависимости от обрабатываемого материала, глубины резания и выбранного значения подачи (0,135 мм/зуб);
– коэффициенты твердости обрабатываемого материала;
– коэффициент материала режущей части;
– коэффициенты состояния поверхности заготовки (с коркой);
– коэффициент главного угла в плане;
– коэффициент отношения ширины фрезерования к диаметру фрезы;
– коэффициент периода стойкости режущей части фрезы;
– коэффициент способа крепления пластины и наличия покрытия;
– коэффициент наличия охлаждения (с охлаждением);
– коэффициент группы обрабатываемого материала.
Частота вращения шпинделя:
Подача:
Проведем проверочный расчет по мощности. Касательная составляющая силы резания:
где – касательная составляющая силы резания, выбираемая в зависимости от обрабатываемого материала, диаметра и числа зубьев фрезы, ширины и глубины фрезерования, а также выбранного значения подачи;
– коэффициент материала режущей части фрезы;
– коэффициент главного угла в плане;
– коэффициент отношения фактической ширины фрезерования к нормативной;
– коэффициент отношения фактического количества зубьев к нормативному.
Расчетная мощность резания:
Выбираем наибольшее значение мощности .
2.2. Чистовое фрезерование зоны 4. Обрабатываемый материал – чугун СЧ15.
Исходные данные для расчета:
Инструмент – фреза концевая диаметром 8 мм с механическим креплением твердосплавных пластин с износостойким покрытием (марка твердого сплава ВК6, количество пластин 3), с главным углом в плане 75°.
Период стойкости инструмента T = 90 мин.
Ширина фрезерования B = 6,5 мм. Глубина фрезерования t = 1,5 мм соответственно.
Материал – чугун СЧ15. Твердость HB не более 2200 МПа
Рекомендуемое значение подачи на зуб:
где – подача на зуб в зависимости от обрабатываемого материала, диаметра и числа зубьев фрезы, ширины и глубины фрезерования;
– коэффициент твердости обрабатываемого материала;
– коэффициент материала режущей части;
– коэффициент, учитывающий отношение фактического числа зубьев фрезы к нормативному;
– коэффициент, учитывающий отношение вылета фрезы к диаметру;
Подача на оборот:
где – количество зубьев фрезы.
Значения скорости и мощности резания:
где – скорость (м/мин) и мощность (кВт) резания в зависимости от обрабатываемого материала, глубины резания и выбранного значения подачи (0,034 мм/зуб);
– коэффициенты группы обрабатываемого материала;
– коэффициенты твердости обрабатываемого материала;
– коэффициенты материала режущей части инструмента;
– коэффициенты периода стойкости режущей части фрезы;
– коэффициент отношения ширины фрезерования к диаметру фрезы;
– коэффициенты состояния поверхности заготовки (с коркой);
– коэффициенты, учитывающие наличие или отсутствия СОЖ.
Частота вращения шпинделя:
Подача:
Проведем проверочный расчет по мощности. Касательная составляющая силы резания:
где – касательная составляющая силы резания, выбираемая в зависимости от диаметра и числа зубьев фрезы, ширины и глубины фрезерования, а также выбранного значения подачи;
– коэффициент обрабатываемого материала;
– коэффициент материала режущей части фрезы;
– коэффициент отношения фактической ширины фрезерования к нормативной;
– коэффициент отношения фактического количества зубьев к нормативному.
Расчетная мощность резания:
2.3. Чистовое фрезерование зоны 7. Обрабатываемый материал – сталь 30Л.
Исходные данные для расчета:
Инструмент – фреза торцевая диаметром 40 мм с механическим креплением твердосплавных пластин с износостойким покрытием (марка твердого сплава ВК8, количество пластин 8), с главным углом в плане 75°.
Период стойкости инструмента T = 60 мин.
Ширина фрезерования B = 35 мм. Глубина фрезерования t = 5 мм соответственно.
Материал – сталь 30Л. Твердость HB не более 2080 МПа.
Рекомендуемое значение подачи на зуб:
где – подача на зуб в зависимости от обрабатываемого материала, диаметра и числа зубьев фрезы, ширины и глубины фрезерования, а также от жесткости системы станок — приспособление — инструмент —деталь (группа подач I – фрезерование жестких деталей закрепленных непосредственно на столе станка, при небольших вылетах фрез);
– коэффициент твердости обрабатываемого материала;
– коэффициент материала режущей части;
– коэффициент главного угла в плане;
– коэффициент способа крепления пластины и наличия покрытия;
– коэффициент схемы установки фрезы (симметричная);
– коэффициент отношения фактической ширины фрезерования к нормативной (120 мм);
– коэффициент группы обрабатываемого материала.
Подача на оборот:
где – количество зубьев фрезы.
Значения скорости и мощности резания:
где – скорость (м/мин) и мощность (кВт) резания в зависимости от обрабатываемого материала, глубины резания и выбранного значения подачи (0,085 мм/зуб);
– коэффициенты твердости обрабатываемого материала;
– коэффициент материала режущей части;
– коэффициенты состояния поверхности заготовки (с коркой);
– коэффициент главного угла в плане;
– коэффициент отношения ширины фрезерования к диаметру фрезы;
– коэффициент периода стойкости режущей части фрезы;
– коэффициент способа крепления пластины и наличия покрытия;
– коэффициент наличия охлаждения (с охлаждением);
– коэффициент группы обрабатываемого материала.
Частота вращения шпинделя:
Подача:
Проведем проверочный расчет по мощности. Касательная составляющая силы резания:
где – касательная составляющая силы резания, выбираемая в зависимости от обрабатываемого материала, диаметра и числа зубьев фрезы, ширины и глубины фрезерования, а также выбранного значения подачи;
– коэффициент материала режущей части фрезы;
– коэффициент главного угла в плане;
– коэффициент отношения фактической ширины фрезерования к нормативной;
– коэффициент отношения фактического количества зубьев к нормативному.
Расчетная мощность резания:
Выбираем наибольшее значение мощности .
2.4. Чистовое фрезерование зоны 4. Обрабатываемый материал – сталь 30Л.
Исходные данные для расчета:
Инструмент – фреза концевая диаметром 8 мм с механическим креплением твердосплавных пластин с износостойким покрытием (марка твердого сплава ВК6, количество пластин 3), с главным углом в плане 75°.
Период стойкости инструмента T = 90 мин.
Ширина фрезерования B = 6,5 мм. Глубина фрезерования t = 1,5 мм соответственно.
Материал – сталь 30Л. Твердость HB не более 2080 МПа.
Рекомендуемое значение подачи на зуб:
где – подача на зуб в зависимости от обрабатываемого материала, диаметра и числа зубьев фрезы, ширины и глубины фрезерования;
– коэффициент твердости обрабатываемого материала;
– коэффициент материала режущей части;
– коэффициент, учитывающий отношение фактического числа зубьев фрезы к нормативному;
– коэффициент, учитывающий отношение вылета фрезы к диаметру;
Подача на оборот:
где – количество зубьев фрезы.
Значения скорости и мощности резания:
где – скорость (м/мин) и мощность (кВт) резания в зависимости от обрабатываемого материала, глубины резания и выбранного значения подачи (0,029 мм/зуб);
– коэффициенты группы обрабатываемого материала;
– коэффициенты твердости обрабатываемого материала;
– коэффициенты материала режущей части инструмента;
– коэффициенты периода стойкости режущей части фрезы;
– коэффициент отношения ширины фрезерования к диаметру фрезы;
– коэффициенты состояния поверхности заготовки (с коркой);
– коэффициенты, учитывающие наличие или отсутствия СОЖ.
Частота вращения шпинделя:
Подача:
Проведем проверочный расчет по мощности. Касательная составляющая силы резания:
где – касательная составляющая силы резания, выбираемая в зависимости от диаметра и числа зубьев фрезы, ширины и глубины фрезерования, а также выбранного значения подачи;
– коэффициент обрабатываемого материала;
– коэффициент материала режущей части фрезы;
– коэффициент отношения фактической ширины фрезерования к нормативной;
– коэффициент отношения фактического количества зубьев к нормативному.
Расчетная мощность резания:
2.5. Выбор двигателя главного движения
Табл. 3
Режимы обработки
Зона обработки | Обрабатываемый материал | n, об/мин | S, мм/мин | N, кВт |
7 | Чугун СЧ15 | 687 | 742 | 11,48 |
Сталь 30Л | 2062 | 1402 | 17,7 | |
4 | Чугун СЧ15 | 1569 | 188 | 0,23 |
Сталь 30Л | 2834 | 298 | 0,46 |
Определим мощность двигателя главного движения PДВ, кВт, учитывая рассчитанную выше максимальную эффективную мощность резания.
Требуемая мощность на валу двигателя главного движения в установившемся режиме с учетом потерь в передачах ηст составляет:
Учитывая требуемые параметры, в качестве двигателя главного движения выбираем асинхронный электродвигатель частотного регулирования АДЧР180S4 (рис. 8).
Рис.10
Основные технические характеристики электродвигателя:
Табл. 4
Мощность, кВт | 22 |
Номинальная скорость, об/мин | 1500 |
Момент, Нм | 143 |
Максимальная скорость, об/мин | 4500 |
Применение частотного регулирования позволяет регулировать частоту вращения шпинделя станка в широком диапазоне, а наличие встроенного электромагнитного динамического тормоза дает возможность как и удерживать вал двигателя в неподвижном состоянии, так и систематически останавливать его с любой скорости за минимальное время.
2.6. Расчет электродвигателя привода подачи
Для станков с ЧПУ могут быть применены различные виды приводов подачи: механический, гидравлический, пневматический и электрический. Однако электрический привод вытесняет все другие виды приводов из-за их существенных недостатков и служит для регулирования скорости в широком диапазоне с высокой точностью и быстродействием, имеет широкий ряд мощностей, моментов и скоростей.
Частота оборотов двигателя определяется скоростью перемещения рабочих органов станка и передаточным отношением механической передачи.
где – шаг ходового винта, мм (
– передаточное отношение (
v – скорость ускоренного хода, м/мин (v = 8 м/мин).
Момент инерции поступательного перемещающегося узла, приведенный к валу двигателя:
где и – массы узла станка и детали соответственно, кг (т.е. масса подвижной части исполнительного механизма соответствующей координаты станка).
Момент инерции ходового винта, кг м, приведенный к валу двигателя:
где – средний диаметр винта, м;
– длина винта, м.
Суммарный момент инерции механизма:
Общий вращающий момент двигателя складывается из статического и динамического моментов:
Статический момент определяется усилием, передаваемым в направлении подачи при установившемся движении рабочего органа станка, т.е. тяговым усилием Р. Тогда статический момент на двигателе подачи передачи винт-гайка:
Предварительно выбираем двигатель с номинальным моментом при максимальной скорости соответствующей скорости быстрого хода.
Выбираем асинхронный двигатель АДЧР80В2.
Динамический момент на двигателе определяется суммарным моментом инерции механизма , приведенным к валу двигателя, и собственным моментом инерции двигателя с учетом моментов инерции датчиков скорости и угла поворота, если они имеются, и ускорением Ɛ, которое должен развить двигатель:
Ускорение двигателя определяется по времени переходного процесса, заданному закону изменения скорости.
Таким образом, при разгоне до скорости быстрого хода за время двигатель должен иметь ускорение:
где – время переходного процесса (0,1…1 сек), выбирается в зависимости от массы подвижных частей (500 – 1500 кг).
Тогда динамический момент при скачкообразном изменении управляющего сигнала:
Находим момент от сил трения:
где f – коэффициент трения в направляющих;
η – КПД механической передачи.
Находим момент от сил резания:
Проверка электродвигателя на пригодность. Должны соблюдаться следующие 3 условия:
Проверяем:
16,3 Нм > 6,68 Нм
7,4 Нм > 2,68 Нм
- 3000 об/мин > 667 об/мин
Все условия соблюдаются, электродвигатель нам подходит.
Раздел 3. Задачи и функции, выполняемые СЧПУ на проектируемом станке.
3.1. Геометрическая задача
В рамках геометрической задачи осуществляется формообразование поверхности детали. В геометрическую задачу входит:
- Ввод и хранение СПО
- Ввод, редактирование и хранение УП
- Интерпретация кадра
- Интерполяция
- Управление приводами
- реализация обратной связи по положению
- реализация обратной связи по скорости
- аварийный останов
- работа УЧПУ в относительных или абсолютных координатах
- согласование УЧПУ и ИП
- автоматический выход в точку М
- автоматический выход в точку R
- автоматический выход в точку N
- автоматический выход в точку F
- Работа с технологическими циклами
- Коррекция УП
- Ввод и хранение СПО
Программное обеспечение (ПО) микропроцессорных систем ЧПУ в общем виде состоит из трех частей:
- системное ПО
- технологическое ПО
- функциональное ПО
Специальное программное обеспечение (СПО) обеспечивает распределение ресурсов устройства ЧПУ, а также организацию процесса обработки, ввода – вывода, редактирования и управления данными [1, с.67]. Для СПО используется энергонезависимая память. Ввод СПО осуществляется с USB или дискового носителя.
- Ввод, редактирование и хранение УП
Управляющая программа (УП) – савокупность команд на языке программирования, обеспечивающая функционирование рабочих органов станка согласно заданному алгоритму по обработке конкретной детали [1, с.18]. Она включает размерную, технологическую и вспомогательную информацию.
Подготовительные функции G определяют способ обработки информации, тип программирования и условия перемещения к заданной точке.
Вспомогательные функции М в основном являются функциями управления электроавтоматикой станка – включения/выключения шпинделя, СОЖ, смены инструмента и др.
УП изменяется при изготовлении разных деталей. Она может вводиться покадрово или целиков следующими способами: с USB, с ЭВМ верхнего уровня, с пульта УЧПУ.
- Интерпретация кадра
Функция интерпретации кадра необходима для того, чтобы перевести команды, записанные в кадрах УП, в вид, понятный СЧПУ.
При интерпретации кадра решаются следующие задачи:
- Распределение информации кадра по адресам памяти, соответствующим буквенно-цифровому коду, в том числе перевод чисел из десятичной системы в двоичную.
- Анализ вспомогательной функции М и формирование кодов управления электроавтоматикой станка.
- Перевод размерных величин перемещений и скоростей в машинные единицы путём умножения на масштабные коэффициенты.
- Анализ кодов учёта корректирующих поправок на размеры инструмента и коррекции траектории.
- Расчёт исходных данных для интерполяции, анализ признаков торможения и расчёт тормозного пути.
- Интерполяция
Интерполяция – процесс получения с требуемой точностью координат промежуточных точек траектории по координатам вспомогательных опорных точек аппроксимируемого контура с величиной дискреты СЧПУ и заданной функцией интерполяции.
Линейная интерполяция задается командой G01, обеспечивающей перемещение инструмента по прямой линии от начальной до конечной точки с заданной скоростью. Скорость перемещения указывается адресом F. Пример линейной интерполяции приведен на рис. 11. Кадр задает перемещение по прямой в точку с координатами (35;45) со скоростью подачи 240 мм/мин.
Рис. 11
Круговая интерполяция (рис. 12) задается по следующим правилам:
- выбор плоскости интерполяции XOY командой G17, плоскости интерполяции XOZ командой G18, плоскости интерполяции YOZ командой G19
- выбор направления движения инструмента по часовой стрелке командой G02, против часовой – командой G03
- задание движения в приращениях
- задание центра окружности в интерполяционной системе координат IJK
Рис.12
На разрабатываемом ГПМ СЧПУ обеспечивает следующие виды интерполяции: G01 – линейная; G02, G03 – круговая в плоскостях XOY, XOZ.
- Управление приводами
5.1) Реализация обратной связи по положению
Реализацию обратной связи по положению рассмотрим на примере управления приводом перемещения стола (ось X) (рис.13). На двигатель М1 из СЧПУ подается сигнал Xзад о перемещении рабочего органа на заданное расстояние. Двигатель АДЧР80В2 через сильфонную муфту ВК3/150/75/38/40 связан с ШВП, которая осуществляет перемещение рабочего органа. Оптический линейный измерительный преобразователь ИП1 Heidenhine LC 415 посылает в СЧПУ сигнал Хфакт о фактическом положении рабочего органа. Если разница фактического Хфакт и заданного Xзад положения рабочего органа не равна нулю и превышает допустимое значение, то на двигатель М1 посылается сигнал ΔX= Хфакт – Xзад о перемещении рабочего органа для устранения рассогласования.
Рис. 13. Управление приводом перемещения стола (ось Х)
5.2) Реализация обратной связи по скорости
Реализацию обратной связи по скорости рассмотрим на примере управления приводом перемещения колонны (ось Z) (рис.15). На двигатель М3 из СЧПУ подается сигнал Fзад о перемещении рабочего органа с заданной скоростью. Оптический линейный измерительный преобразователь ИП3 Heidenhine LC 415 посылает в СЧПУ сигнал Fфакт о фактической скорости рабочего органа. Если разница фактической Fфакт и заданной Fзад скорости рабочего органа не равна нулю и превышает допустимое значение, то на двигатель М2 посылается сигнал ΔF = Fфакт – Fзад о изменении скорости перемещения рабочего органа для устранения рассогласования.
Рис. 14. Управление приводом перемещения шпиндельной бабки (ось Y)
Рис. 15. Управление приводом перемещения колонны (ось Z)
Рис. 16. Управление приводом поворота стола (ось B)
5.3) Аварийный останов привода
Чтобы исключить перемещение рабочего органа за пределы рабочего органа устанавливают 6 концевых выключателей: 2 – для плавного торможения, 2 – для отключения двигателя, крайние 2 – для аварийного отключения СЧПУ.
5.4) Работа УЧПУ в абсолютной или относительной системе координат
Эта функция задается в УП с помощью подготовительных функций G90, G91. Без сигналов, соответствующих этим функциям не будет реализованы алгоритмы интерполяции и рабочие органы не начнут перемещаться.
5.5) Согласование УЧПУ и ИП
Эта функция исключает возникновение рывков после включения привода.
5.6) Автоматической выход рабочего органа в нулевую точку станка M
Положение рабочего органа в точке М фиксируется ИП, который при достижении точки М выдает сигнал «0». Для перемещения рабочих органов в точку М используется подготовительная функция G53, осуществляющая выход рабочих органов в точку М по осям X, Y и Z соответственно.
5.7) Реферирование
Функция предполагает автоматический выход рабочего органа в референтную точку R станка. На проектируемом ГПМ точка R необходима для уменьшения величин холостых ходов. На двигатели приводов подач продается сигнал, соответствующий подготовительной функции G28. При достижении рабочими органами точки R каждый ИП посылает сигнал «R » на УЧПУ.
5.8) Автоматический выход рабочих органов в точку смены инструмента
Перед сменой инструментов колонна и шпиндельная бабка выходят в точку N по сигналу, соответствующему подготовительной функции G14. При достижении рабочими органами точки N в СЧПУ подаются осведомительные сигналы от концевых выключателей 8 и 17.
5.9) Автоматический выход рабочего органа в точку смены столов-спутников
При выполнении цикла смены заготовки рабочие органы должны выйти в точку, в которой развернется цикл смены. Функции выполнения цикла смены заготовки: М60-внос, М62-вынос.
- Работа с постоянными технологическими циклами
СЧПУ может автоматически рассчитывать и формировать траектории движения инструмента, если в УП заданы постоянные технологические циклы обработки.
Цикл – процесс отдельных движений станка для различных видов обработки, выполняемых специальными инструментами. Каждый постоянных цикл имеет определенный формат записи, который записывается и вызывается при необходимости в кадрах основной УП.
На проектируемом ГПМ применяются следующие циклы: цикл сверления G81, цикл резьбонарезания G84.
- Коррекция УП
СЧПУ может автоматически пересчитывать координаты опорных точек траекторий, заданных в УП, с учетом фактически используемых параметров инструмента. Используются подготовительные функции: G40, G41, G42, G43, G44.
3.2. Логическая задача
В рамках логической задачи осуществляется управление цикловой автоматикой станка.
В логическую задачу входит:
- Управление приводом главного движения:
- включение и выключение привода главного движения:
- задание частоты вращения и диапазона частот вращения:
- реализация обратной связи по скорости:
Рис. 17. Привод главного движения
- реверс:
Реверс дает возможность обрабатывать зеркальные детали по одной УП, а также необходим при выходе метчика из отверстия с нарезанной резьбой. Реализуется вспомогательной функцией М04.
- согласование частоты вращения с величиной подачи при резьбонарезании:
Согласование частоты вращения с величиной подачи осуществляется при задании подготовительной функции G33, сигнал от которой подается на привод главного движения. С ИП7 Heidenhine EQN 425 привода главного движения снимается сигнал «Р», который подается на привод перемещения рабочего органа, участвующего в процессе резьбонарезания.
- аварийный останов привода:
Привод главного движения автоматически останавливается в аварийном режиме при превышении допустимой частоты вращения.
- ориентированный останов шпинделя:
Ориентированный останов шпинделя необходим для автоматического доворота до нужного положения шпинделя для последующего выполнений цикла автоматической смены инструмента. Задается при помощи вспомогательной функции М19. Осведомительный сигнал ? с ИП7 говорит о том, что шпиндель довернулся до нужного положения и можно начинать цикл смены инструмента.
- Управление циклом автоматической смены инструмента.
До начала цикла рабочие органы станка должны быть выведены в точку смены инструмента N по сигналу, соответствующему подготовительной функции G14 (см. рис.13-15): колонна отводится в крайнее заднее положение, шпиндельная бабка поднимается в крайнее верхнее положение. Также по сигналу М19 выполняется ориентированный останов шпинделя.
Определим вспомогательные функции, используемые в цикле автоматической смены инструмента:
Т01-Т20 – выбор инструмента в инструментальном магазине;
М06 – цикл смены инструмента в шпинделе.
Операции по поиску необходимого режущего инструмента в инструментальном магазине, выполняемые по функции Т, производятся во время обработки для уменьшения времени смены инструмента.
Логико-временная последовательность сигналов при управлении циклом смены инструмента приведена в таблице 5.
Табл. 5
Фун-я | № | Выполняемая операция | Входной сигнал | Выходной сигнал |
Т01-Т20 | Поиск инструмента в инструментальном магазине | Т01-Т20 | 33 | |
Перемещение корпуса автооператора на – 200 мм вдоль оси Y (захват оправки) | 33 | 34 | ||
Перемещение руки автооператора на -200 мм вдоль оси Z (вытаскивание оправки) | 34 | 35 | ||
Перемещение корпуса автооператора на +200 мм вдоль оси Y (возврат в позицию смены инструмента) | 35 | 36 | ||
Перемещение руки автооператора на +200 мм вдоль оси Z (возврат в позицию смены инструмента) | 36 | 37 | ||
М11 | Разжим инструмента в шпинделе | М11 | 38 | |
М06 | Перемещение руки автооператора на -200 мм вдоль оси Z (вытаскивание оправки) | 38 | 39 | |
Поворот руки автооператора на -180o вокруг оси Z | 39 | 40 | ||
Перемещение руки автооператора на +200 мм вдоль оси Z (вставка оправки) | 40 | 41 | ||
М10 | Зажим инструмента в шпинделе | М10 | 42 | |
Т01-Т20 | Перемещение руки автооператора на -200 мм вдоль ось Z | 42 | 43 | |
Перемещение корпуса автооператора на -200 мм вдоль оси Y | 43 | 44 | ||
Перемещение руки автооператора на +200 мм вдоль оси Z (вставка оправки) | 44 | 45 | ||
Перемещение корпуса автооператора на +200 мм вдоль оси Y (отпускание оправки) | 45 | 46 | ||
Поворот руки автооператора на 180o вокруг оси Z | 46 | 47 |
Рис. 18. 1) Поиск инструмента в инструментальном магазине
Рис. 19. 2,4,12,14) Перемещение корпуса автооператора вдоль оси Y на ±200 мм
Рис. 20. 3,5,7,9,11,13) Перемещение руки автооператора вдоль оси Z на ±200 мм
Рис. 21. 6,10)Зажим/разжим инструментальной оправки в шпинделе
Рис. 22. 8.15) Поворот руки автооператора вокруг оси Z на ±180°
- Управление циклом автоматической смены заготовки.
С началом цикла рабочие органы станка должны быть выведены в точку смены инструмента F по соответствующим координатам.
Определим вспомогательные функции, используемые в цикле автоматической смены инструмента:
М60 – цикл загрузки заготовки в станок.
М62 – цикл выгрузки готовой детали из станка.
Логико-временная последовательность сигналов при управлении циклом смены заготовки приведена в таблице 6.
Табл. 6
Фун-я | № | Выполняемая операция | Входной сигнал | Выходной сигнал |
М60 | Перемещение колонны вдоль оси Z в точку F | М60 | 22 | |
Перемещение шпиндельной бабки вдоль оси Y в точку F | 22 | 23 | ||
Перемещение стола станка вдоль оси X в точку F | 23 | 24 | ||
Поворот накопителя вокруг оси О2 на -90о | 24 | 48 | ||
Перемещение Т-образного захватного устройства на +500 мм вдоль оси X | 48 | 49 | ||
Подъем стола-спутника на накопителе вдоль оси О2 на -50 мм | 49 | 50 | ||
Перемещение Т-образного захватного устройства на -500 мм вдоль оси X | 50 | 51 | ||
Поворот перегрузочного устройства вокруг оси O1 на -180о | 51 | 52 | ||
Перемещение Т-образного захватного устройства на -500 мм вдоль оси X | 52 | 53 | ||
Зажим стола-спутника на столе станка с его перемещением вдоль оси Y на +50 мм | 53 | 54 | ||
Перемещение Т-образного захватного устройства на +500 мм вдоль оси X | 54 | 55 | ||
М62 | Перемещение Т-образного захватного устройства на -500 мм вдоль оси X | М62 | 56 | |
Разжим стола-спутника на столе станка с его перемещением вдоль оси Y на -50 мм | 56 | 57 | ||
Перемещение Т-образного захватного устройства на +500 мм вдоль оси X | 57 | 58 | ||
Поворот перегрузочного устройства вокруг оси O1 на +180о | 58 | 59 | ||
Перемещение Т-образного захватного устройства на +500 мм вдоль оси X | 59 | 60 | ||
Опускание стола-спутника на накопителе вдоль оси О2 на +50 мм | 60 | 61 | ||
Перемещение Т-образного захватного устройства на -500 мм вдоль оси X | 61 | 62 | ||
Поворот накопителя вокруг оси О2 на -90о | 62 | 63 | ||
Перемещение стола станка вдоль оси X в референтную точку | 63 | R(X) | ||
Перемещение шпиндельной бабки вдоль оси Y в референтную точку | R(X) | R(Y) | ||
Перемещение колонны вдоль оси Z в референтную точку | R(Y) | R(Z) (сним.М62) |
Рис. 23.
Рис. 24.
Рис. 25.
Рис. 26.
Рис. 27
Рис. 28
Раздел 4. Технологическая задача, решаемая СЧПУ
4.1. Обзор и анализ измерительных преобразователей и измеряемых ими параметров
В настоящее время практически все металлорежущие станки с ЧПУ оснащаются измерительными системами. Измерительные системы позволяют многократно сократить число брака и простои технологического оборудования на производстве, связанные с выполнением контроля и наладки вручную.
Методы контроля классифицируются по временной последовательности технологического процесса изготовления детали:
Рис. 29. Классификация методов контроля по временной последовательности
4.1.1. Виды проверок, относящихся к уровню базовых элементов технологического процесса (контроля задолго до обработки):
- Проектирование с учетом пригодности для массового производства состоит в подходе к конструированию изделий с учетом существующих технологических возможностей производства.
- Контроль входных характеристик процесса – включает анализ характера и последствий отказов и аналогичные методы, применение которых позволяет понимать и контролировать все существующие факторы, которые могут повлиять на результаты процесса обработки.
- Контроль стабильности параметров окружающей среды направлен на учет тех внешних источников отклонений, которые не могут быть устранены заблаговременно, поскольку являются неотъемлемой характеристикой среды, в которой выполняется процесс.
- Системный подход к разработке технологического маршрута для того, чтобы оптимальным образом обеспечивались автоматизация и стабильность условий выполнения процесса для увеличения производительности.
- Проверка технического состояния станка является неотъемлемой частью подготовки оборудования, поскольку на неисправном станке невозможно стабильное изготовление точных деталей. Строгая процедура оценки эксплуатационных и технических характеристик станка, текущий ремонт, калибровка и, если необходимо, восстановление станка позволяют привести его параметры в соответствие с требованиями к технологическому процессу.
4.1.2. Контроль непосредственно перед обработкой
Рис. 30
Контроль наличия заготовки, определение ее размеров и положения осуществляют при помощи контактного измерительного щупа, установленного в шпинделе станка (рис.29).
Рис. 31. Контактный щуп Renishaw OMP60.
Фирма Renishaw предлагает следующие варианты конструктивного исполнения измерительных щупов:
- Электроконтактный датчик касания с механической системой срабатывания
Рис. 30. Устройство электроконтактного датчика касания фирмы Renishaw.
Три стержня (ролика), расположенные на одинаковом расстоянии друг от друга, опираются на шесть шариков из карбида вольфрама, обеспечивающих шесть точек контакта в системе точного базирования. Посредством этих контактов формируется электрическая цепь. Подпружиненный механизм позволяет щупу датчика отклоняться при соприкосновении с поверхностью детали и обеспечивает возвращение датчика в исходное положение с точностью в пределах 1 мкм, когда щуп отводится от поверхности (в отсутствие касания).
При нагружении пружины создаются пятна контакта, через которые может течь ток. Противодействующие силы в механизме датчика приводят к уменьшению некоторых пятен контакта, вследствие чего повышается сопротивление таких элементов. При контакте (соприкосновении) с деталью переменная сила, воздействующая на пятно контакта, измеряется как изменение электрического сопротивления. Когда сопротивление превышает некоторое пороговое значение, на выходе датчика подается сигнал о срабатывании.
Описанный принцип действия кинематического механизма определяет стадии генерации сигнала срабатывания, показанные ниже, на рисунке 31.
Рис 31. Принцип генерации сигнала срабатывания электроконтактного датчика.
- Электронный датчик касания с тензоэлементами
Следующей модификацией измерительного щупа стал более точный электронный датчик касания с тензоэлементами. Электронный датчик касания с тензоэлементами изображён на рисунке 33.
Тензометрические датчики размещаются на специально спроектированных элементах, установленных в конструкции датчика, но отдельно от кинематического механизма. Тензометрические датчики расположены таким образом, чтобы регистрировать все усилия на щупе в 3-х направлениях, которые затем суммируются.
При достижении порогового значения в любом направлении генерируется сигнал срабатывания под воздействием сил, которые намного слабее сил, необходимых для срабатывания обычного датчика. В то же время для удерживания щупа в датчиках используется кинематический механизм. Такая система, гарантирует повторяемость при возвращении щупа в исходное положение, что является ключевым фактором обеспечения точных измерений.
Рис. 32. Электронный датчик касания с тензоэлементами.
Процесс измерений полностью независим от кинематического механизма датчика, это обеспечивает высокую степень точности и стабильные характеристиками срабатывания, что обычно недостижимо при использовании датчиков обычной конструкции.
Фирма Heidenhain использует следующий принцип работы измерительных щупов (рис. 33): световой пучок, генерируемый
светодиодом, фокусируется системой линз на дифференциальном фотоэлементе. При отклонении стилуса дифференциальный фотоэлемент генерирует триггерный сигнал. Стилус жестко соединен с переключателем, который расположен в корпусе на трехточечной опоре. Опора в трех точках с физической точки зрения обеспечивает идеальные условия для положения покоя. Благодаря бесконтактному оптическому принципу сенсор не изнашивается. Таким образом, щупы обеспечивают долговременную стабильность при высокой повторяемости.
Рис. 33. Контактный щуп Heidenhain с оптическим сенсором.
Кроме классификации датчиков по типу срабатывания, существует несколько вариантов передачи сигналов от них в систему ЧПУ.
Выбор конкретной системы передачи сигналов определяется типом используемого датчика и типом станка, на котором он установлен.
Компании Heidenhain и Renishaw предлагают три способа связи СЧПУ и датчика:
Файлы условия, демо
Характеристики курсовой работы
Список файлов
