Курсовая работа: Система управления ГПМ на базе 5-координатного многоцелевого фрезерного станка с ЧПУ для изготовления корпусных деталей
Описание
Руководитель: Руднев С.К.

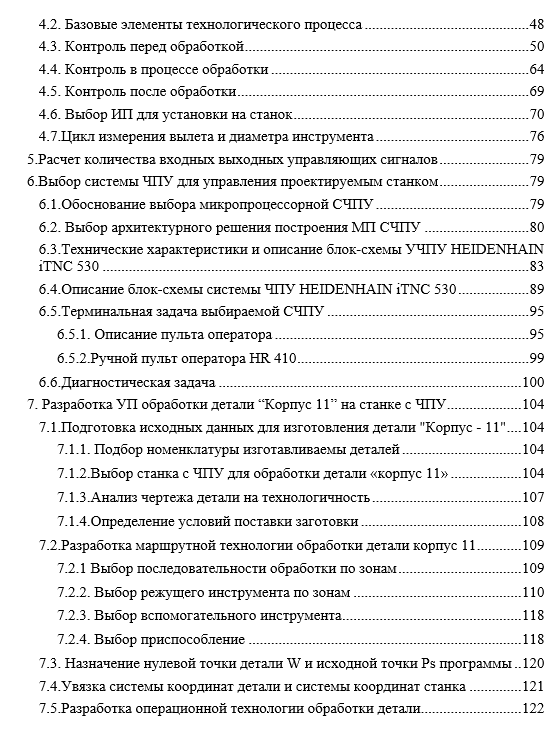
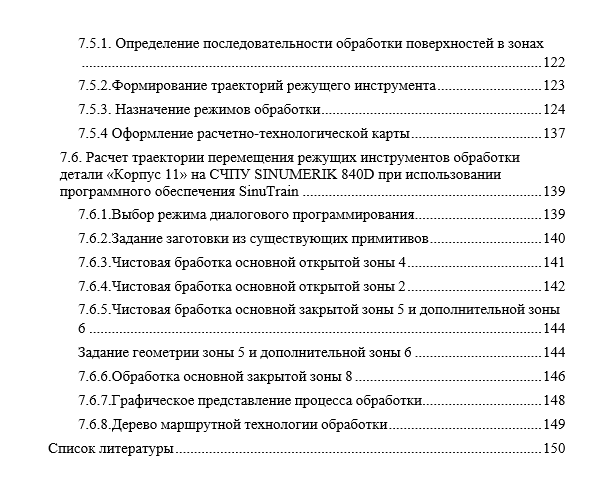
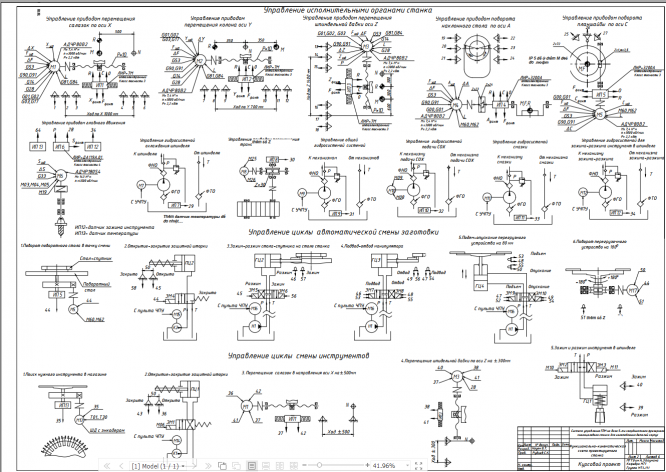
Тема проекта:
Система управления ГПМ на базе 5-ти координатного фрезерного многоцелевого станка для изготовления деталей корпус
II. Техническое задание: На основе анализа номенклатуры типовых обрабатываемых деталей обосновать разработку ГПМ и выбрать систему ЧПУ для его управления. Характеристики типовой детали " Корпус ": габаритные размеры- 400х300х300 мм; квалитет точности - 7 ; шероховатость- 1,25 ; материал – чугун СЧ15, сталь 45 и алюминиевый сплав Д16Т .
III. Объем и содержание проекта.
План пояснительной записки:
1. Чертеж детали " Корпус ".
2. Обзор и анализ номенклатуры типовых обрабатываемых деталей.
3. Принципиальная схема проектируемого ГПМ.
4. Расчет и обоснование диапазона частот вращения шпинделя и пределов подач рабочих органов ГПМ по наиболее и наименее нагруженным технологическим переходам для обработки поверхностей типовой детали " Корпус ".
5. Расчет мощности и выбор электродвигателей рабочих органов ГПМ.
6. Задачи и функции, решаемые выбираемой СЧПУ на проектируемом ГПМ с указанием номенклатуры обменных сигналов.
7. Технологическая задача СЧПУ.
8. Расчет количества входных выходных управляющих сигналов.
9. Основные технические характеристики проектируемого ГПМ.
10 Обоснование архитектурного решения построения СЧПУ и описание блок-схемы.
11. Терминальная задача выбираемой СЧПУ.
12. Диагностическая задача СЧПУ.
13. Технические характеристики СЧПУ.
14. Расчетно-технологическая карта изготовления детали, автоматизированное или диалоговое программирование при подготовке УП.
Графическая часть:
1. Технологические возможности проектируемого ГПМ – лист (ов).
2. Функционально-кинематическая схема ГПМ – лист (ов).
3. Технологическая задача, решаемая выбранной СЧПУ – лист (ов).
4. Блок-схема выбранной СЧПУ – лист (ов).
5. Исследовательская часть – лист (ов).
Содержание
1.Обзор и анализ номенклатуры типовых обрабатываемых деталей. 11
1.1 Обзор обрабатываемых зон типовых деталей. 11
1.2.Требования, выполняемые системой ЧПУ.. 8
1.3. Принципиальная схема проектируемого ГПМ.. 11
2.Назначение режимов обработки. 12
2.1.Черновое фрезерование зоны 10. Обрабатываемый материал – чугун СЧ15. 12
2.2. Чистовое фрезерование зоны 22. Обрабатываемый материал – чугун СЧ15. 15
2.3. Чистовое фрезерование зоны 10. Обрабатываемый материал – сталь 45. 16
2.4.Сверление отверстий 22. Обрабатываемый материал – сплав Д16Т. 18
2.5.Результаты расчета режимов резания. 18
2.6. Расчет электродвигателя привода подачи. 19
3.1.1.Ввод и хранение СПО.. 23
3.1.2.Ввод, редактирование и хранение УП.. 23
3.1.5.Управление приводами. 25
3.1.6.Функция работы с постоянными технологическими циклами обработки 31
3.1.7. Функция коррекции УП с учетом фактических размеров и величины износа инструментов. 33
3.2.1.Управление приводом главного движения. 35
3.2.2. Управление циклом автоматической смены инструмента. 36
3.2.3.Управление циклом смены заготовки. 40
4.Технологическая задача, решаемая СЧПУ.. 43
4.1.Обзор и анализ измерительных преобразователей и измеряемых ими параметров. 43
4.2. Базовые элементы технологического процесса. 48
4.3. Контроль перед обработкой. 50
4.4. Контроль в процессе обработки. 64
4.5. Контроль после обработки. 69
4.6. Выбор ИП для установки на станок. 70
4.7.Цикл измерения вылета и диаметра инструмента. 76
5.Расчет количества входных выходных управляющих сигналов. 79
6.Выбор системы ЧПУ для управления проектируемым станком. 79
6.1.Обоснование выбора микропроцессорной СЧПУ.. 79
6.2. Выбор архитектурного решения построения МП СЧПУ.. 80
6.3.Технические характеристики и описание блок-схемы УЧПУ HEIDENHAIN iTNC 530. 83
6.4.Описание блок-схемы системы ЧПУ HEIDENHAIN iTNC 530. 89
6.5.Терминальная задача выбираемой СЧПУ.. 95
6.5.1. Описание пульта оператора. 95
6.5.2.Ручной пульт оператора HR 410. 99
6.6.Диагностическая задача. 100
7. Разработка УП обработки детали “Корпус 11” на станке с ЧПУ.. 104
7.1.Подготовка исходных данных для изготовления детали "Корпус - 11". 104
7.1.1. Подбор номенклатуры изготавливаемы деталей. 104
7.1.2.Выбор станка с ЧПУ для обработки детали «корпус 11 » . 104
7.1.3.Анализ чертежа детали на технологичность. 107
7.1.4.Определение условий поставки заготовки. 108
7.2.Разработка маршрутной технологии обработки детали корпус 11. 109
7.2.1 Выбор последовательности обработки по зонам. 109
7.2.2. Выбор режущего инструмента по зонам. 110
7.2.3. Выбор вспомогательного инструмента. 118
7.2.4. Выбор приспособление. 118
7.3. Назначение нулевой точки детали W и исходной точки Ps программы.. 120
7.4.Увязка системы координат детали и системы координат станка. 121
7.5.Разработка операционной технологии обработки детали. 122
7.5.1. Определение последовательности обработки поверхностей в зонах. 122
7.5.2.Формирование траекторий режущего инструмента. 123
7.5.3. Назначение режимов обработки. 124
7.5.4 Оформление расчетно-технологической карты.. 137
7.6.1.Выбор режима диалогового программирования. 139
7.6.2.Задание заготовки из существующих примитивов. 140
7.6.3.Чистовая бработка основной открытой зоны 4. 141
7.6.4.Чистовая бработка основной открытой зоны 2. 142
7.6.5.Чистовая бработка основной закрытой зоны 5 и дополнительной зоны 6 144
Задание геометрии зоны 5 и дополнительной зоны 6. 144
7.6.6.Обработка основной закрытой зоны 8. 146
7.6.7.Графическое представление процесса обработки. 148
7.6.8.Дерево маршрутной технологии обработки. 149
На основании проведенного анализа зон обработки можно сформулировать следующие требования к системе ЧПУ:
- Черновая, получистовая и чистовая обработка зон (1-4, 6-10, 13, 14, 16-24, 28) при использовании линейной интерполяции по координатам X, Y, Z от 1 до 3 одновременно.
- Черновая, получистовая и чистовая обработка зон (5, 10-12, 15, 23) при использовании круговой интерполяции в трех плоскостях: OXY – поверхность 10, 11, 12, OXZ – поверхность 23, OYZ – поверхность 5
- Черновая, получистовая и чистовая обработки зон (8, 24, 26) при использовании оси C.
- Позиционирование: 26
- Формообразование: 8, 24
- Черновая, получистовая и чистовая обработки зон (14, 16, 17) при использовании оси А.
- Позиционирование: 14, 16, 17
- Черновая, получистовая и чистовая обработки зон (14, 16, 17) при использовании оси А.
5 одновременно управляемых координат.
Для обработки данных деталей от рабочих органов станка и системы ЧПУ требуется:
- управление вращением шпинделя станка (осуществление процесса резания);
- управление вертикальным перемещением шпиндельной бабки (ось Z);
- управление продольным перемещением (ось Х);
- управление поперечным перемещением (ось Y);
- управление поворотом план-шайбы по координате C.
- управление поворотом наклонного стола по координате A.
Для обработки данной корпусной детали станок для осуществления главного движения должен иметь шпиндель вертикальной компоновки с регулируемым приводом. Для обработки на станке корпусных деталей средних и малых размеров с 4-х сторон без переустановок необходим поворотная план-шайба (Ось С). Для обеспечения возможности обработки с помощью одновременно пяти управляемых координат необходим поворот наклонного стола (Ось A). На многоцелевом станке с вертикальным шпинделем может производиться получистовое и чистовое фрезерование деталей концевыми, торцевыми и дисковыми фрезами, а также растачивание, сверление, зенкерование, развертывание и нарезание резьбы.
На многоцелевом станке с вертикальным шпинделем может производиться получистовое и чистовое фрезерование деталей концевыми, торцевыми и дисковыми фрезами, а также растачивание, сверление, зенкерование, развертывание и нарезание резьбы.
Наличие на станке ЧПУ дает возможность реализовать программы обработки деталей с практически неограниченным количеством различных операций. Переход на новую номенклатуру деталей производиться сменой управляющих программ.
В связи с наличием отверстий различных диаметров и способов их обработки в инструментальном магазине предусмотрены 30 позиции.
Режимы обработки детали колеблются в широком диапазоне, т.к. необходима и предварительная обработка с большими усилиями резания, и чистовая с высокими скоростями резания. Кроме того, также может быть широка номенклатура обрабатываемых материалов. От станка требуется обеспечение 7-го квалитета точности и 7-го класса шероховатости (Ra 1,6) обрабатываемых повершностей детали. Станок назначаем повышенной точности – «П » , – что отображает технологические требования, предъявляемые как к обрабатываемым деталям, так и требования ко всем станкам с ЧПУ. Необходимые размеры рабочей зоны станка: 530х450х450 мм.
Вывод: СЧПУ должна управлять ГПМ на базе пятикоординатного многоцелевого фрезерного станка с ЧПУ.
1.3. Принципиальная схема проектируемого ГПМ
Поскольку обработка ведется большим количеством инструмента, а также в связи с наличием необходимости переустановки заготовки на станок, с целью экономии времени вводятся устройство смены столов спутников и смены инструмента.
Компоновочное решение проектируемого ГПМ приведено на рисунке 7.
Рис. 1.3. Компоновка проектируемого ГПМ
2.Назначение режимов обработки
Назначение режимов обработки проведем по справочнику [2] для наиболее и наименее нагруженных переходов для разных обрабатываемых материалов: чугун СЧ15 ГОСТ 1412-85, сталь 45 и алюминиевый сплав Д16Т. Наиболее нагруженным переходом является черновое фрезерование зоны 10, наименее нагруженным – сверление отверстий 22.
2.1.Черновое фрезерование зоны 10. Обрабатываемый материал – чугун СЧ15.
Исходные данные для расчета:
Инструмент – фреза торцевая диаметром 40 мм с механическим креплением твердосплавных пластин с износостойким покрытием (марка твердого сплава ВК6, количество пластин 8), с главным углом в плане 75°.
Период стойкости инструмента T = 60 мин.
Ширина фрезерования B = 35 мм. Глубина фрезерования t = 5 мм соответственно.
Материал – чугун СЧ15. Твердость HB не более 2200 МПа (ГОСТ 1412-85).
Рекомендуемое значение подачи на зуб:
где – подача на зуб в зависимости от обрабатываемого материала, диаметра и числа зубьев фрезы, ширины и глубины фрезерования, а также от жесткости системы станок — приспособление — инструмент —деталь (группа подач I – фрезерование жестких деталей закрепленных непосредственно на столе станка, при небольших вылетах фрез);
– коэффициент твердости обрабатываемого материала;
– коэффициент материала режущей части;
– коэффициент главного угла в плане;
– коэффициент способа крепления пластины и наличия покрытия;
– коэффициент схемы установки фрезы (симметричная);
– коэффициент отношения фактической ширины фрезерования к нормативной (120 мм);
– коэффициент группы обрабатываемого материала.
Подача на оборот:
где – количество зубьев фрезы.
Значения скорости и мощности резания:
где – скорость (м/мин) и мощность (кВт) резания в зависимости от обрабатываемого материала, глубины резания и выбранного значения подачи (0,135 мм/зуб);
– коэффициенты твердости обрабатываемого материала;
– коэффициент материала режущей части;
– коэффициенты состояния поверхности заготовки (с коркой);
– коэффициент главного угла в плане;
– коэффициент отношения ширины фрезерования к диаметру фрезы;
– коэффициент периода стойкости режущей части фрезы;
– коэффициент способа крепления пластины и наличия покрытия;
– коэффициент наличия охлаждения (с охлаждением);
– коэффициент группы обрабатываемого материала.
Частота вращения шпинделя:
Подача:
Проведем проверочный расчет по мощности. Касательная составляющая силы резания:
где – касательная составляющая силы резания, выбираемая в зависимости от обрабатываемого материала, диаметра и числа зубьев фрезы, ширины и глубины фрезерования, а также выбранного значения подачи;
– коэффициент материала режущей части фрезы;
– коэффициент главного угла в плане;
– коэффициент отношения фактической ширины фрезерования к нормативной;
– коэффициент отношения фактического количества зубьев к нормативному.
Расчетная мощность резания:
Выбираем наибольшее значение мощности .
2.2. Чистовое фрезерование зоны 22. Обрабатываемый материал – чугун СЧ15.
Инструмент – сверло твердосплавное Ø19 мм (марка твердого сплава ВК6. Период стойкости инструмента 35 мин.
Подача на оборот:
где – подача в зависимости от обрабатываемого материала, диаметра отверстия и отношения длины режущей части к диаметру инструмента;
– коэффициент твердости обрабатываемого материала;
Скорость резания:
где – скорость резания в зависимости от обрабатываемого материала, диаметра отверстия и отношения длины режущей части к диаметру инструмента;
– коэффициент твердости обрабатываемого материала;
– коэффициент наличия охлаждения;
– коэффициент состояния поверхности заготовки;
– коэффициент инструментального материала;
– коэффициент формы заточки инструмента;
– коэффициент длины рабочей части;
– коэффициент покрытия инструментального материала;
– коэффициент отношения фактического периода стойкости к нормативному.
Частота вращения шпинделя:
Подача:
2.3. Чистовое фрезерование зоны 10. Обрабатываемый материал – сталь 45.
Исходные данные для расчета:
Инструмент – фреза торцевая диаметром 40 мм с механическим креплением твердосплавных пластин с износостойким покрытием (марка твердого сплава ВК8, количество пластин 8), с главным углом в плане 75°.
Период стойкости инструмента T = 60 мин.
Ширина фрезерования B = 35 мм. Глубина фрезерования t = 5 мм соответственно.
Материал – сталь 45. Твердость HB не более 2080 МПа.
Рекомендуемое значение подачи на зуб:
где – подача на зуб в зависимости от обрабатываемого материала, диаметра и числа зубьев фрезы, ширины и глубины фрезерования, а также от жесткости системы станок — приспособление — инструмент —деталь (группа подач I – фрезерование жестких деталей закрепленных непосредственно на столе станка, при небольших вылетах фрез);
– коэффициент твердости обрабатываемого материала;
– коэффициент материала режущей части;
– коэффициент главного угла в плане;
– коэффициент способа крепления пластины и наличия покрытия;
– коэффициент схемы установки фрезы (симметричная);
– коэффициент отношения фактической ширины фрезерования к нормативной (120 мм);
– коэффициент группы обрабатываемого материала.
Подача на оборот:
где – количество зубьев фрезы.
Значения скорости и мощности резания:
где – скорость (м/мин) и мощность (кВт) резания в зависимости от обрабатываемого материала, глубины резания и выбранного значения подачи (0,085 мм/зуб);
– коэффициенты твердости обрабатываемого материала;
– коэффициент материала режущей части;
– коэффициенты состояния поверхности заготовки (с коркой);
– коэффициент главного угла в плане;
– коэффициент отношения ширины фрезерования к диаметру фрезы;
– коэффициент периода стойкости режущей части фрезы;
– коэффициент способа крепления пластины и наличия покрытия;
– коэффициент наличия охлаждения (с охлаждением);
– коэффициент группы обрабатываемого материала.
Частота вращения шпинделя:
Подача:
Проведем проверочный расчет по мощности. Касательная составляющая силы резания:
где – касательная составляющая силы резания, выбираемая в зависимости от обрабатываемого материала, диаметра и числа зубьев фрезы, ширины и глубины фрезерования, а также выбранного значения подачи;
– коэффициент материала режущей части фрезы;
– коэффициент главного угла в плане;
– коэффициент отношения фактической ширины фрезерования к нормативной;
– коэффициент отношения фактического количества зубьев к нормативному.
Расчетная мощность резания:
Выбираем наибольшее значение мощности .
2.4.Сверление отверстий 22. Обрабатываемый материал – сплав Д16Т.
Инструмент – сверло твердосплавное Ø19мм (марка твердого сплава ВК6). Период стойкости инструмента 35 мин.
Подача на оборот:
Скорость резания:
Частота вращения шпинделя:
Подача:
2.5.Результаты расчета режимов резания
Табл. 1
Режимы обработки
Зона обработки | Обрабатываемый материал | n, об/мин | S, мм/мин | N |
10 | Чугун СЧ15 | 687 | 742 | 11,48 |
Сталь 45 | 1402 | 2062 | 17,7 | |
22 | Чугун СЧ15 | 3037 | 820 | 0,23 |
Д16Т | 5857 | 1757 | 0,46 |
2.6. Расчет электродвигателя привода подачи
Для станков с ЧПУ могут быть применены различные виды приводов подачи: механический, гидравлический, пневматический и электрический. Однако электрический привод вытесняет все другие виды приводов из-за их существенных недостатков и служит для регулирования скорости в широком диапазоне с высокой точностью и быстродействием, имеет широкий ряд мощностей, моментов и скоростей.
Частота оборотов двигателя определяется скоростью перемещения рабочих органов станка и передаточным отношением механической передачи.
где – шаг ходового винта, мм (
– передаточное отношение (
v – скорость ускоренного хода, м/мин (v = 8 м/мин).
Момент инерции поступательного перемещающегося узла, приведенный к валу двигателя:
где и – массы узла станка и детали соответственно, кг (т.е. масса подвижной части исполнительного механизма соответствующей координаты станка).
Момент инерции ходового винта, кг м, приведенный к валу двигателя:
где – средний диаметр винта, м;
– длина винта, м.
Суммарный момент инерции механизма:
Общий вращающий момент двигателя складывается из статического и динамического моментов:
Статический момент определяется усилием, передаваемым в направлении подачи при установившемся движении рабочего органа станка, т.е. тяговым усилием Р. Тогда статический момент на двигателе подачи передачи винт-гайка:
Предварительно выбираем двигатель с номинальным моментом при максимальной скорости соответствующей скорости быстрого хода.
Выбираем асинхронный двигатель АДЧР80В2.
Динамический момент на двигателе определяется суммарным моментом инерции механизма , приведенным к валу двигателя, и собственным моментом инерции двигателя с учетом моментов инерции датчиков скорости и угла поворота, если они имеются, и ускорением Ɛ, которое должен развить двигатель:
Ускорение двигателя определяется по времени переходного процесса, заданному закону изменения скорости.
Таким образом, при разгоне до скорости быстрого хода за время двигатель должен иметь ускорение:
где – время переходного процесса (0,1…1 сек), выбирается в зависимости от массы подвижных частей (500 – 1500 кг).
Тогда динамический момент при скачкообразном изменении управляющего сигнала:
Находим момент от сил трения:
где f – коэффициент трения в направляющих;
η – КПД механической передачи.
Находим момент от сил резания:
Проверка электродвигателя на пригодность. Должны соблюдаться следующие 3 условия:
Проверяем:
16,3 Нм > 6,68 Нм
7,4 Нм > 2,68 Нм
- 3000 об/мин > 667 об/мин
Все условия соблюдаются, электродвигатель нам подходит.
Выбор двигателей
Привод | Модель двигателя |
|
| Мощность, кВт |
X | АДЧР80В2 | 7,4 | 3000 | 2,2 |
Y | АДЧР80В2 | 7,4 | 3000 | 2,2 |
Z | АДЧР80В2 | 7,4 | 3000 | 2,2 |
A | АДЧР80В2 | 7,4 | 3000 | 2,2 |
B | АДЧР80В2 | 7,4 | 3000 | 2,2 |
Главного движения | АДЧР180S4 | 143 | 4500 | 11 |
3.Задачи и функции, решаемые выбираемой СЧПУ на проектируемом ГПМ с указанием номенклатуры обменных сигналов
3.1.Геометрическая задача
В рамках геометрической задачи осуществляется формообразование поверхности детали.
В геометрическую задачу входит:
- Ввод и хранение СПО
- Ввод, редактирование и хранение УП
- Интерпретация кадра
- Интерполяция
- Управление приводами
- реализация обратной связи по положению
- реализация обратной связи по скорости
- аварийный останов
- работа УЧПУ в относительных или абсолютных координатах
- согласование УЧПУ и ИП
- автоматический выход в точку М
- автоматический выход в точку R
- автоматический выход в точку N
- автоматический выход в точку F
- Работа с технологическими циклами
- Коррекция УП
Для ввода системного программного обеспечения в станке используется ЭВМ верхнего уровня, память для СПО должна быть энергонезависимой, т. е. способной сохранять информацию при пропадании питающего напряжения. Системное ПО обеспечивает распределение ресурсов СЧПУ, организацию процесса обработки, ввод-вывод, редактирование и управление данными.
3.1.2.Ввод, редактирование и хранение УП
Управляющая программа вводиться в СЧПУ с дискового накопителя, с пульта управления или по каналам связи с ЭВМ высшего уровня. Память для хранения управляющей программы, которая обычно представляется в коде ИСО, должна быть энергонезависимой. В СЧПУ высших классов управляющая программа обычно вводиться сразу и целиком и запоминается в оперативной памяти системы. Однако в ряде СЧПУ используется также метод покадрового ввода управляющей программы - путем поэтапного (покадрового) чтения перфоленты фотосчитывающим устройством системы управления.
В выбираемой системе введенная управляющая программа после отладки и редактирования с использованием СЧПУ может быть введена на какие-либо внешние устройства: автоматическое печатающее устройство, графопостроитель, дисплей, накопитель на магнитных дисках и т.д.
3.1.3.Интерпретация кадра
Так как УП состоит из кадров. Отработка очередного кадра требует проведения ряда предварительных процедур называемых интерпретацией. Для обеспечения непрерывного контурного управления процедуры интерпретации последующего кадра должны быть реализованы во время управления задаваемого кадра. Во время отработки станком очередного кадра система ЧПУ считывает следующий кадр, анализируя при этом информацию которую несет в себе этот кадр.
Кадры содержат подготовительные функций, функции перемещения и вспомогательные функции. Каждый кадр заканчивается знаком “конец кадра” (LF). Этот символ должен быть записан всегда. Программа начинается %.
При интерпретации кадра решаются следующие задачи:
- Распределение информации кадра по адресам памяти, соответствующим буквенно-цифровому коду, в том числе перевод чисел из десятичной системы в двоичную.
- Анализ вспомогательной функции М и формирование кодов управления электроавтоматикой станка.
- Перевод размерных величин перемещений и скоростей в машинные единицы путём умножения на масштабные коэффициенты.
- Анализ кодов учёта корректирующих поправок на размеры инструмента и коррекции траектории.
- Расчёт исходных данных для интерполяции, анализ признаков торможения и расчёт тормозного пути.
3.1.4.Интерполяция
Интерполяция - процесс получения с требуемой точностью координат промежуточных точек траектории по координатам вспомогательных опорных точек аппроксимируемого контура с величиной дискреты СЧПУ и заданной функцией интерполяции.
В задачу ЧПУ и входит расчет текущих координат. Одной из основных задач, решаемой системой ЧПУ, является обеспечение движения инструмента относительно детали по заданной траектории. Каждый участок задается координатами начальной и конечной точек и параметрами уравнения участка.
На станке осуществляется:
- линейная интерполяция,
- круговая интерполяция,
- винтовая интерполяция,
При линейной интерполяции в кадре указываются тип интерполяции (G01) и координаты конечной точки участка. Координаты конечной точки являются координатами начальной точки следующего участка. При круговой интерполяции указывают плоскость интерполяции (G17-G19), ее направление и тип (G02, G03) и перемещение из начальной точки дуги в конечную, а также координаты начальной точки дуги в интерполяционной системе координат. Алгоритмы интерполяций можно разделить на 2 группы. К 1-ой группе относятся алгоритм оценочной функции и метод цифрового дифференциального анализатора, ко 2-ой группе относится метод цифрового интегрирования (МЦИ). В многоцелевых системах ЧПУ применяются алгоритмы интерполяции относящиеся ко 2-ой группе.
3.1.5.Управление приводами
Сложность управления зависит от типа привода. В общем случае задача сводится к организации цифровых позиционных следящих систем для каж-дой координаты. На вход такой системы поступают коды, соответствующие результатам интерполяции. Этим кодам должно отвечать положение по коор-динате — линейное или угловое перемещение.
Реализация обратной связи по положению рабочего органа рассмотрим на примере управления приводом перемещения салазки (Ось X). На двигатель М1 из СЧПУ подается сигнал Xзад о перемещении рабочего органа на заданное расстояние. Двигатель через муфту связан с ШВП, которая осуществляет перемещение рабочего органа. Оптический линейный измерительный преобразователь ИП1 модели Hendenhain LC415 посылает в СЧПУ сигнал Хфакт о фактическом положении рабочего органа. Если разница фактического Хфакт и заданного Xзад положения рабочего органа не равна нулю и превышает допустимое значение, то на двигатель М1 посылается сигнал ΔX = Хфакт – Xзад о перемещении рабочего органа для устранения рассогласования.
Для обеспечения точности обработки необходимо иметь информацию о текущем истинном положении рабочего органа. Имеется двигатель, который принимает сигнал на перемещение, но вследствие погрешности ШВП, погрешностей коробки скоростей, износа и погрешностей, вносимых тепловым расширением, истинное перемещение будет отличным от заданного. Для реализации обратной связи по положению в качестве измерительного преобразователя используются аналоговые датчики, которые установлены на ШВП, они осуществляют косвенное измерение перемещений через угол ходового винта. Эти ИП являются дешевыми и легко устанавливаются на винт двигателя.
Рис. 3.1 Управление приводом перемещения столь (ось Х)
Реализация обратной связи по скорости рабочего органа рассмотрим на примере управления приводом перемещения салазок (Ось Y). На двигатель М2 из СЧПУ подается сигнал Fзад о перемещении рабочего органа с заданной скоростью. Оптический линейный измерительный преобразователь ИП2 модели ЛИР–7М посылает в СЧПУ сигнал Fфакт о фактической скорости рабочего органа. Если разница фактической Fфакт и заданной Fзад скорости рабочего органа не равна нулю и превышает допустимое значение, то на двигатель М2 посылается сигнал ΔF = Fфакт – Fзад о изменении скорости перемещения рабочего органа для устранения рассогласования.
Рис. 3.2 Управление приводом перемещения суппорта (ось Y)
Рис. 3.3 Управление приводом перемещения шпиндельной бабки (ось Z)
Управление приводом Ось A
Рис. 3.4 Управление приводом перемещения наклонного стола (ось А)
Управление приводом Ось C
Рис. 3.5. Управление приводом поворотного стола (ось C)
Функция аварийного останова привода
Данная функция позволяет исключить поломку элементов, вследствие несанкционированного выхода рабочего органа за пределы диапазона перемещений. Чтобы исключить перемещение рабочего органа за пределы рабочего органа устанавливают 6 концевых выключателей: 2 – для плавного торможения рабочего органа до фиксированной скорости, 2 – для отключения двигателя, крайние 2 – для авариного отключения устройство ЧПУ.
Торможение может также осуществляться программным способом, т. е. периодическим сравнением истинной скорости рабочего органа с константой, соответствующей максимальной скорости его перемещения.
Функция работы УЧПУ в абсолютной или относительной системе координат
Эта функция задается в УП при помощи подготовительных функций G90 и G91. Без сигналов, соответствующих этим функциям, не будут ре-ализованы алгоритмы интерполяции (сигналы от функций G01, G02, G03, G17 и т. п.) и рабочие органы станка не начнут перемещаться.
Функция согласования УЧПУ и ИП
При использовании в следящих системах ИП типа вращающегося трансформатора или индуктосина необходимо выполнить согласования перед первым включением привода. Согласования заключается в подборе кода задания из СЧПУ отвечающему истинному положению ИП. Так как в проектируемом ГПМ применяются только дискретные ИП марки ЛИР, поэтому необходимости в согласовании СЧПУ и ИП нет.
Функция автоматического выхода рабочего органа в нулевую точку станка
При включении станка рабочий орган автоматически перемещается в начало системы координат станка (нулевую точку М станка). Этот режим позволяет привести в соответствие координаты в УП с истинным положением рабочих органов. Положение рабочего органа в точке М фиксируется специальным ИП. Для перемещения рабочих органов в точку М используется подготовительная функция G53, осуществляющая выход рабочих органов в точку М по осям X, Y, Z, А, С. При достижении нулевой точки ИП посылает сигнал 0 в устройство ЧПУ о выполнении данной функции.
Функция реферирования
Функция предполагает автоматический выход рабочего органа в референтную точку R станка. На проектируемом ГПМ точка R необходима для уменьшения величин холостых ходов. На двигатели рабочих органов, участвующих продается сигнал, соответствующий подготовительной функции G28. При достижении рабочими органами точки R каждый ИП посылает сигнал «R » на УЧПУ.
Автоматический выход рабочего органа в точку N смены инструмента
Перед сменой инструментов колонна и шпиндельная бабка выходят в точку N по сигналу, соответствующему подготовительной функции G14. При достижении рабочими органами точки N в СЧПУ подаются осведомительные сигналы от концевых выключателей 5 и 14.
Автоматический выход рабочего органа в точку смены заготовки. Для выполнения цикла смены заготовки рабочие органы перемещаются в точку F. Для этого используется функция М60. При достижении точки смены заготовки ИП выдают сигнал F.
3.1.6.Функция работы с постоянными технологическими циклами обработки
Выделение повторяющихся (стандартных) участков программы, называемых циклами, является эффективным методом сокращения УП. Так называемые фиксированные циклы характерны для определенных технологических операций (точения, расточка и т. д.) и встречаются при изготовлении многих изделий. Программные технологические циклы соответствуют повторяющимся участкам данного изделия.
Для облегчения подготовки УП и сокращения ее объема вводят технологические циклы. Наличие таких циклов позволяет всю последовательность указанных действий задать в одном кадре.
Цикл – процесс отдельных движений станка для различных видов обработки, выполняемых специальными инструментами. Каждый постоянных цикл имеет определенный формат записи, который записывается и вызывается при необходимости в кадрах основной УП.
На проектируемом ГПМ применяются следующие циклы: G81, G82, G83, G84. Отмена технологических циклов осуществляется при помощи подготовительной функции G80.
Расточные постоянные циклы (G80 – G89)
Постоянный цикл | Подход | Функция на дне отверстия | Возврат | |
Выдержка времени | Вращение шпинделя | |||
G-81 – сверление | рабочая подача | нет | нормальное | ускоренное перемещение к R1 или R2 |
G-82 – растачивание | рабочая подача | да | нормальное | ускоренное перемещение к R1 или R2 |
G-83 – глубокое сверление (с разгрузкой стружки) | в прерывистой работе (подход с рабочей скоростью с промежутком во время быстрого возврата или остановки | да/нет | нормальное | ускоренное перемещение |
G-84 – нарезание резьбы метчиком | рабочая подача: начало вращения | нет | обратное вращение | рабочая подача к R1, ускоренное перемещение к R2 |
G-85 – рассверливание или нарезание резьбы метчиком | рабочая подача | нет | нормальное | рабочая подача к R1, ускоренное перемещение к R2 |
G-86 – развертывание | рабочая подача: начало вращения шпинделя | нет | остановка | ускоренное перемещение |
G-89 – развертывание с растачиванием | рабочая подача | да | нормальное | рабочая подача к R1, ускоренное перемещение к R2 |
G-80 – отмена постоянных циклов |
|
|
|
|
3.1.7. Функция коррекции УП с учетом фактических размеров и величины износа инструментов.
Коррекция сводится к параллельному переносу системы координат, то есть к смешению рабочего органа. Учет фактического размера инструмента при коррекции сводится к формированию траектории эквидистантой запрограммированной.
Коррекция геометрической информации при линейной интерполяции осуществляется путем алгебраического сложения координат опорных точек эквидистанты с числом, заданным в корректоре. Коррекция геометрической информации при круговой интерполяции осуществляется путем алгебраического сложения модуля координат опорных точек эквидистанты с числом, заданным в корректоре. Функции коррекции соответствует сигнал L. Используются подготовительные функции: G40, G41, G42, G43, G44.
3.2. Логическая задача
Развитие логической задачи явилось следствием автоматизации на станке вспомогательной операции: зажим-разжим, подвод-отвод, переключение, пуск-стоп, автоматическая смена инструмента и т. д. Именно многообразие составляет специфику логической задачи и оно заключается в большом количестве обменных сигналов (их число измеряется десятками) между УЧПУ и станком.
Под системой цикловой автоматики понимают систему автоматического управления механизмами и группами механизмов, поведение которых определяется множеством параллельных и последовательных операций. Отдельные операции осуществляются электрическим управляющими сигналами, а условные смены операций формируются под влиянием так называемых осведомительных сигналов, поступающих от станка.
Все сложные циклические процессы, выполненные на станке с ЧПУ, можно представить в виде циклов автоматики.
Циклом автоматики станка с ЧПУ называют последовательность действий, вызываемых по имени одним из 3-х следующих слов кадра УП «Скорость главного движения » , «Функция инструмента » , «Вспомогательная функция » .
Цикл автоматики состоит из операций, причем под операцией можно понимать любое независимое действие отдельного механизма, включаемое одним двигателем, инициируемое самостоятельным управляющим сигналом, подтверждаемое осведомительным сигналом.
В рамках логической задачи осуществляется управление цикловой автоматикой станка.
В логическую задачу входит:
- Управление приводом главного движения
- включение и выключение привода главного движения
- задание частоты вращения и диапазона частот вращения
- реализация обратной связи по скорости
- реверс
- согласование частоты вращения с величиной подачи при резьбонарезании
- аварийный останов привода
- управление приводом главного движения как угловой координаты
- ориентированный останов шпинделя
- Реализация цикла автоматической смены инструмента
- Реализация цикла автоматической смены заготовки
- Компенсация УЧПУ кинематических погрешностей станка
- сигнал управления двигателем (включение, вращение по часовой стрелке M03, вращение против часов стрелке М04, стоп М05.
- сигнал задания частоты вращения S.
- сигнал рассогласование частоты вращения DS.
Рис. 3.6. Управление приводом главного движения
Включение и выключение привода главного движения осуществляется при помощи вспомогательных функций М03, М05.
Задание частоты вращения шпинделя осуществляется в УП при помощи функции S.
Реализация обратной связи по скорости осуществляется так же, как и для линейного перемещения, описанного в разделе 3.1.
Реверс дает возможность обрабатывать зеркальные детали по одной УП, а также необходим при выходе метчика из отверстия с резьбой. Реализуется вспомогательной функцией М04.
Согласование частоты вращения с величиной подачи при резьбонарезании осуществляется подготовительной функцией G33.
Аварийный останов привода. Привод главного движения автоматический останавливается, если частота вращения превышает допустимую.
Ориентированный останов шпинделя необходим для выполнения цикла автоматической смены инструмента. Задается при помощи вспомогательной функции М19. По достижении шпинделем требуемого углового положения ИП посылает в СЧПУ сигнал 28, который разрешает цикл смены инструмента.
3.2.2. Управление циклом автоматической смены инструмента
До начала цикла рабочие органы станка должны быть выведены в точку смены инструмента N по соответствующим координатам. В начале цикла в шпинделе нет инструмента.
Определим вспомогательные функции, используемые в цикле автоматической смены инструмента:
Т01-Т30 – выбор инструмента инструментальном магазине
М06 – цикл смены инструмента во фрезерном шпинделе
М10 – зажим инструмента
М11 – разжим инструмента
Цикл начинается с поиска необходимого режущего инструмента, предварительно установленного в ячейку инструментального магазина. Сигнал вспомогательной функции T с числовым значением, соответствующим номеру инструмента (T00-T30), включает двигатель М13 привода вращения инструментального магазина. Как только нужный инструмент найден, ИП13 выдает сигнал 35, который приходит на двигатель М13 и происходит его останов. Контроль положения позиций инструментального магазина осуществляется бесконтактным измерительным преобразователем ИП13.
Цикл раскрытия защитной шторки. По сигналу, соответствующему вспомогательной функции М06 и приходящему на ЭМ1 золотника пневмоцилиндра ПЦ1, сжатый воздух подается в левую полость ПЦ1, шток которого прозводит раскрытие защитной шторки. После ее раскрытия концевой выключатель выдает осведомительный сигнал 40.
По сигналу, соответствующему вспомогательной функции М19 и приходящему на двигатель М6 привода главного движения, шпиндель доворачивается до заданного углового положения. ИП6 формирует сигнал 28.
По сигналам 36, приходящим на двигатель М1 привода подачи по оси X и происходит перемещение салазок в направлении оси X 500 мм. По достижении требуемого положения ИП 1 подает сигнал 37, который останавливает привод салазок.
По сигналу 37, поступающему на двигатель М3 привода подачи по оси Z, происходит перемещение шпиндельной бабки в направлении оси +Z 300 мм. По достижении требуемого положения ИП3 подает сигнал 38, который останавливает двигатель М3.
По сигналу, соответствующему функции М11 и приходящему на ЭМ3 золотника гидроцилиндра ГЦ1, масло подается в левую полость ГЦ1, шток которого разжимает оправку с инструментом в шпинделе. При этом формируется сигнал 39.
По сигналу, соответствующему функции М10 и приходящему на ЭМ2 золотника гидроцилиндра ГЦ1, масло подается в правую полость ГЦ1, шток которого разжимает оправку с инструментом в шпинделе. При этом формируется сигнал 40.
По сигналу 40, поступающему на двигатель М3 привода подачи по оси Z, происходит перемещение шпиндельной бабки в направлении оси -Z 300 мм. По достижении требуемого положения ИП3 подает сигнал 41, который останавливает двигатель М3.
Сигнал 41 поступает на двигатель М1 привода подачи по оси X и происходит перемещение салазок в направлении оси -X 500 мм. По достижении требуемого положения ИП1 подает сигнал 42, который останавливает привод салазок и снимает сигнал М06 с электромагнита ЭМ1.
После снятия с ЭМ1 сигнала М06 происходит переключение золотника под действием пружины, сжатый воздух поступает в правую полость ПЦ1, шток которого закрывает защитную шторку. При этом формируется сигнал 43, завершающий цикл смены инструмента.
Логико-временная последовательность сигналов при управлении циклом смены инструмента приведена в таблице
Последовательность движений в цикле смены инструмента
Входной сигнал | Работа механизма | Выходной сигнал |
T01 – T30 | Поворот инструментального магазина – поиск инструмента | 35 |
35 | Раскрытие защитной шторки | 36 |
36 | Перемещение салазок в направлении оси X 500 мм | 37 |
37 | Перемещение шпидельной бабкой в направлении оси Z 300 мм | 38 |
М11 | Разжим инструмента в шпинделе | 39 |
М10 | Зажим инструмента в шпинделе | 40 |
40 | Перемещение шпидельной бабкой в направлении оси -Z 300 мм | 41 |
41 | Перемещение салазок в направлении оси -X 500 мм | 42 |
42 | Закрытие защитной шторки | 43 |
Рис 3.7. Логико-временная последовательность сигналов при управлении циклом смены инструмента на ГПМ
3.2.3.Управление циклом смены заготовки
С началом цикла рабочие органы станка должны быть выведены в точку смены инструмента F по соответствующим координатам.
Определим вспомогательные функции, используемые в цикле автоматической смены инструмента:
М60 – цикл загрузки заготовки в станок.
М62 – цикл выгрузки готовой детали из станка.
Рис. 3.8. Логико-временная последовательность сигналов при управлении циклом смены заготовки на ГПМ
По сигналу, соответствующему вспомогательной функции М60 (движение стола-спутника в рабочую зону) или М62 (движение из рабочей зоны), необходимые органы станка должны переместиться в точку N смены столов-спутников. По достижении этой точки ИП5 формирует осведомительный сигнал 44, останавливающий привод подачи.
Для движения стола-спутника из рабочей зоны станка по сигналу 44 от концевого выключателя привода станка, приходящему на ЭМ4 золотника пневмоцилиндра ПЦ2, сжатый воздух подается в правую полость ПЦ3, шток которого производит раскрытие защитной шторки. После ее раскрытия концевой выключатель выдает осведомительный сигнал 45.
Сигнал 45 является входным для ЭМ5 золотника ГЦ2. Увеличение давления масла в правой полости ГЦ2 позволяет осуществить разжим стола-спутника на столе станка. При достижении штоком ГЦ2 положения расфиксации стола-спутника концевой выключатель выдает осведоми-тельный сигнал 46.
Сигнал 46 является входным для ЭМ7 золотника ГЦ3. Увеличение давления масла в левой полости ГЦ3 заставляет манипулятор перемещаться в направлении стола станка. Перемещение продолжается до момента срабатывания концевого выключателя, выдающего осведомительный сигнал 47.
По сигналу 47, поступающему на ЭМ9, происходит включение золотника ГЦ4. Под давлением масла в нижней полости ГЦ4 осуществляется подъем перегрузочного устройства. Как только оно достигнет нужного положения, вырабатывается сигнал 48.
По сигналу 48, приходящему на ЭМ8 золотника ГЦ3, масло подается в правую полость ГЦ5, шток которого вместе с манипулятором перемещается к перегрузочному устройству. Перемещение происходит до момента срабатывания концевого выключателя и выдачи осведомительного сигнала 49.
Сигнал 49 поступает на ЭМ10 золотника ГЦ4. Под давлением масла в верхней полости ГЦ4 осуществляется опускание перегрузочного устройства до момента срабатывания концевого выключателя, формирующего осведомительный сигнал 50.
Сигнал 50 запускает двигатель привода вращательного движения перегрузочного устройства, и перегрузочное устройство поворачивается на –180° до срабатывания концевого выключателя, формирующего осведомительный сигнал 51, останавливающий привод вращения.
Сигнал 51 запускает двигатель М17 привода вращательного движения перегрузочного устройства. Перегрузочное устройство поворачивается на +180° до срабатывания концевого выключателя, формирующего осведомительный сигнал 2, останавливающий привод вращения.
По сигнал у 49, поступающему на ЭМ 15, происходит включение золотника
гидроцилиндра ГЦ8. Под давлением масла в нижней полости ГЦ8 осуществляется подъем перегрузочного устройства. Как только оно достигнет нужного положения, вырабатывается сигнал 50.
По сигналу 52, поступающему на ЭМ9, происходит включение золотника гидроцилиндра ГЦ4. Под давлением масла в нижней полости ГЦ4 осуществляется подъем перегрузочного устройства. Как только оно достигнет нужного положения, вырабатывается сигнал 53.
Сигнал 53 является входным для ЭМ7 золотника ГЦ3. Увеличение давления масла в левой полости ГЦ3 заставляет манипулятор перемещаться в направлении стола станка. Перемещение продолжается до момента срабатывания концевого выключателя, выдающего осведомительный сигнал 54.
Сигнал 54 поступает на ЭМ10 золотника ГЦ4. Под давлением масла в верхней полости ГЦ4 осуществляется опускание перегрузочного устройства до момента срабатывания концевого выключателя, формирующего осведомительный сигнал 55.
По сигналу 55, приходящему на ЭМ8 золотника ГЦ3, масло подается в правую полость ГЦ, шток которого вместе с манипулятором перемещается к перегрузочному устройству. Перемещение происходит до момента срабатывания концевого выключателя и выдачи осведомительного сигнала 56.
Сигнал 56 поступает на ЭМ6 золотника гидроцилиндра ГЦ2, вызывая перемещение штока вправо, что позволяет осуществить зажим стола-спутника. По достижении положения фиксации стола-спутника вырабатывается осведомительный сигнал 57.
По сигналу 57 происходит снятие сигнала 44 с электромагнита ЭМ4 золотника пневмоцилиндра ПЦ2, шток которого перемещается вправо и производит закрытие защитной шторки. После ее раскрытия концевой выключатель выдает осведомительный сигнал 58.
4.Технологическая задача, решаемая СЧПУ
4.1.Обзор и анализ измерительных преобразователей и измеряемых ими параметров
Технологическая задача приветствует лишь в тех случаях, когда основной рабочий процесс сам становится объектом управления в целях его поддержания либо оптимизации. Выполняет следующие функции:
- Управление средствами контроля на станке. Как правило, на станке имеются ИП, обеспечивающие дополнительные измерения параметров стан-ка, инструмента, приспособления с заготовкой до процесса обработки, в ходе обработки и после нее. При этом микропроцессорное устройство ЧПУ управляет специальными измерительными циклами, формируемыми подготовительными функциями, например G65.
- Адаптивное управление механообработкой. Адаптация осуществляется изменением контурной скорости и скорости привода главного движения. Необходимая информация получаемая от дополнительно установленных датчиков – момента сопротивления, мощности привода главного движения, вибраций, температуры и т. д.
- Накопление статической информации К нему относятся фиксация текущего времени и времени работы, определение коэффициентов загрузки оборудования, учет информации и т. д.
Выбранная СЧПУ осуществляет реализацию активного контроля при помощи специальных измерительных щупов
Датчики касания Renishaw могут использоваться на обрабатывающих центрах и фрезерных станках с ЧПУ для привязки заготовки и измерения детали в процессе ее изготовления.
Контактные измерения позволяют отказаться от использования дорогостоящих зажимных приспособлений и длительной процедуры выставления заготовки относительно осей станка вручную с помощью циферблатных индикаторов. Устанавливаемые в шпиндель обрабатывающих центров датчики касания обеспечивают следующие преимущества:
- сокращение простоя станка;
- автоматизацию крепления заготовки, ее выравнивания по отношению к осям станка и корректировки углового положения поворотной оси;
- отсутствие ошибок, связанных с неточными действиями оператора;
- снижение объема брака;
- повышение производительности и универсальность по отношению к объему серии обрабатываемых деталей.
Устанавливаемые в шпиндель датчики касания могут применяться для измерения размеров заготовки в процессе ее обработки и для контроля первой обработанной после переналадки станка детали, в то время как успешное использование ручных измерительных приспособлений зависит от навыков оператора, а перенос детали со станка на КИМ не всегда целесообразен.
Преимущества:
- измерение детали в процессе ее изготовления с автоматическим вводом необходимой коррекции;
- уверенность в отсутствии сбоев при автоматической обработке;
- проверка размеров первой обработанной детали при переходе на новую партию деталей с последующим автоматическим вводом коррекции;
- уменьшение времени простоя станка, связанного с ожиданием результатов проверки первой детали.
В настоящее время практически все металлорежущие станки с ЧПУ оснащаются измерительными системами. Измерительные системы позволяют многократно сократить число брака и простои технологического оборудования на производстве, связанные с выполнением контроля и наладки вручную.
Принцип работы контактного датчика:
Датчики, устанавливаемые на станках, часто называют триггерными контактными датчиками (или датчиками касания): в них реализована система срабатывания при контакте измерительного наконечника (щупа) датчика с деталью при ее измерении или установке. Степень повторяемости срабатывания является очень высокой.
При срабатывании датчик посылает сигнал в систему управления через интерфейс, и система управления (почти одновременно) автоматически фиксирует положение станка по его энкодерам (система обратной связи).
Рис.4.1 Датчик, установленный в шпиндель
Датчики для наладки инструмента:
Датчики, используемые для наладки инструмента, обычно крепятся к столу или станине станка. В датчиках этого типа используются контактный или бесконтактный методы для генерации сигнала при срабатывании.
В контактных датчиках для наладки инструмента для обнаружения, измерения и автоматической наладки режущего инструмента используется щуп с реализацией принципа срабатывания при касании.
Бесконтактные датчики для наладки инструмента выполняют те же функции, но при этом используется лазерная система, в которой срабатывание происходит при пересечении инструментом лазерного пучка.
Рис.4.2 Контактная наладка инструмента
Рис. 4.3 Бесконтактная наладка инструмента с использованием лазерной системы
Методы контроля классифицируются по временной последовательности изготовления детали:
Рисунок 4.4. Классификация методов контроля по временной последовательности
До обработки, системы компании Renishaw, обеспечивающие базовые элементы технологического процесса, позволяют добиться максимальной стабильности характеристик станка и техпроцессов.
При использовании непосредственно перед обработкой, системы компании Renishaw, обеспечивают настройки техпроцесса.
При обработки системы компании Renishaw, обеспечивающие контроль в процессе, позволяют учитывать неизбежные отклонения при работе на станке и фактические условия в конкретный момент.
После завертки системы компании Renishaw, обеспечивающие контроль готовой детали, позволяют запротоколировать результат технологического процесса и выполнить проверку полученной детали и устойчивости технологического процесса.
4.2. Базовые элементы технологического процесса
Виды контроля, представленные на самом нижнем уровне, направлены на обеспечение максимальной стабильности параметров среды, в которой осуществляется технологический процесс. Такие профилактические проверки позволяют устранять некоторые причины колебаний параметров, влияющих на процесс обработки.
Виды проверок, относящихся к уровню базовых элементов технологического процесса:
- Проектирование с учетом пригодности для массового производства состоит в подходе к разработке процессов и изделий, основанных на всестороннем понимании существующих возможностей и на стремлении к реализации передового опыта.
- Контроль входных характеристик процесса – включает анализ характера и последствий отказов и аналогичные методы, применение которых позволяет понимать и контролировать все существующие к началу выполнения процесса факторы, которые могут повлиять на результаты процесса обработки.
- Контроль стабильности параметров окружающей среды направлен на учет тех внешних источников отклонений, которые не могут быть устранены заблаговременно, поскольку являются неотъемлемой характеристикой среды, в которой выполняется процесс.
- Системный подход к выбору последовательности операций (технологического маршрута) в процессе изготовления изделий для того, чтобы оптимальным образом обеспечивались автоматизация и стабильность условий выполнения процесса. При этом подразумевается введение на критических этапах обратной связи о ходе процесса.
- Оптимизация состояния станка является неотъемлемой частью всего набора базовых элементов технологического процесса, поскольку на неточном станке невозможно стабильное изготовление точных деталей. Строгая процедура оценки эксплуатационных характеристик станка, калибровка и, если необходимо, восстановление станка позволяют привести его параметры в соответствие с требованиями к технологическому процессу.
4.3. Контроль перед обработкой
Настройка на технологические операции представляет собой ряд операций, выполняемых на станке непосредственно перед резкой металла; осуществление таких операций позволяет прогнозировать успешное выполнение технологического процесса.
При наладке инструмента:
- определяется длина от базовой поверхности шпинделя с целью задания коррекции на высоту и для проверки того, соблюдается ли допуск на длину;
- определяется диаметр при вращении с целью задания коррекции на размер инструмента
При установке заготовка:
- выполняется идентификация заготовки с целью выбора соответствующей программы в системе ЧПУ;
- устанавливается положение базового элемента для задания рабочей системы координат;
- определяется размер заготовки для того, чтобы установить характеристики оставшегося припуска и последовательность черновых проходов;
- осуществляется ориентация заготовки (относительно осей станка) с целью задания поворота системы координат.
При наладке станка:
- выставляются поворотная ось, делительно-поворотный стол или крепежная оснастка, необходимая для выполнения установки и фиксации деталей;
- устанавливается положение центра поворота делительно-поворотного стола и/или контрольные точки на крепежных приспособлениях.
Контроль наличия заготовки и определение ее размеров осуществляют при помощи контактного измерительного щупа, установленного в шпинделе станка.
Принципы работы контактных датчиков:
Всё зависит от правильности выбора инструмента для решения конкретной задачи. Требования к процессу обработки отличаются большим разнообразием, а диапазон требований, предъявляемых к технологическим процессам и инструменту для их выполнения, также чрезвычайно широк.
Какая бы не стояла задача, от измерения простой призматической детали до обеспечения субмикронной точности и работы со сложными формами, – для любого конкретного случая у компании Renishaw всегда есть разработанное, изготовленное и испытанное на практике изделие. Изделия различного типа описаны ниже.
В настоящее время на рынке представлено несколько видов измерительных щупов. Фирма Renishaw предлагает следующие варианты конструктивного исполнения измерительных щупов:
Конструкция резистивного контактного датчика с механической системой срабатывания
Выбор последовательности обработки детали является одной из наиболее важных задач, решаемых при проектировании технологического процесса. Последовательность обработки, указанная с комплексом оснастки и режущего инструмента, полностью определяет маршрут обработки детали на станке с ЧПУ.
Для фрезерной обработки при определении последовательности обработки важно соблюдать условие получения максимальной жесткости детали на каждом участке обработки.
Прежде всего необходимо определить необходимое количество установов детали на столе станка. Заготовка должна быть обработана со всех 6 сторон, поэтому необходимо как минимум два установа, а для получения IT8, следует выполнить 3 установа.
Для представленной детали применима типовая схема обработки для двусторонней детали. Последовательность следующая:
Установ на базу А;
- Черновое фрезерование основной открытой зоны 1;
- Черновое фрезерование основной открытой зоны 2;
- Черновое фрезерование основной закрытой зоны 3;
Установ на базу Б;
- Черновое фрезерование основной открытой зоны 4;
- Чистовое фрезерование основной открытой зоны 4;
- Черновое фрезерование основной закрытой зоны 5;
- Чистовое фрезерование основной закрытой зоны 5 и дополнительных зон 6;
Установ на базу А;
- Чистовое фрезерование основной открытой зоны 1;
- Чистовое фрезерование основной закрытой зоны 3 и дополнительных зон 7;
- Черновое сверление основной закрытой зоны 8;
- Чистовое зенкерование зоны 8.
- Чистовое фрезерование основной открытой зоны 2;
7.2.2. Выбор режущего инструмента по зонам
Процесс выбора инструментов для станков с ЧПУ может быть условно разбит на четыре этапа:
- первый этап — назначение совокупности видов инструмента, определяющего маршрут обработки данной детали;
- второй этап — выбор технологических параметров каждого вида инструмента (материала режущей части, углов заточки режущей кромки, количества зубьев), который производится по машиностроительным нормам;
- третий этап — расчет геометрических параметров выбранного инструмента, отражающих специфику обработки на станке с ЧПУ и определяющих содержание операции;
- четвертый этап — определение конструктивных особенностей специальных режущих инструментов.
Этап 1. Назначение совокупности видов инструмента
Для обработки больших участков плоской поверхности рекомендуется использовать насадные торцовые фрезы со вставными ножами из быстрорежущей стали или пластинами из ТС по ГОСТ 9304-69.
Наружный и внутренней контуры следует обрабатывать концевыми фрезами с коническим хвостовиком по ГОСТ 17026-71.
Получение сквозных отверстий возможно с помощью спиральных сверл с коническим хвостовиком по ГОСТ 10903-77. Угол наклона стружечных канавок должен обеспечивать надежный отвод стружки из отверстия. Для обработки алюминиевых сплавов целесообразно применять сверла с большим углом наклона на винтовой канавки – и более.
Для получения отверстий 8-го квалитета необходима дополнительная обработка зенкером цельным с коническим хвостовиком по ГОСТ 12489-71.
Этап 2. Выбор технологических и геометрических параметров каждого вида инструмента
Основными критериями при выборе технологических параметров являются жесткость, стойкость, точность и универсальность. Для назначения параметров инструментов необходимо знать основные требования, предъявляемые к ним при работе на станках с ЧПУ.
При черновом фрезеровании торцовыми фрезами медных и алюминиевых сплавов используют инструменты с материалом режущей части - ВК4, ВК6, ВК8, Р6М5.
При чистовом фрезеровании торцовыми фрезами медных и алюминиевых сплавов применяют инструменты с материалом режущей части – ВК3, ВК3М, ВК4, ВК6М, ВК8, Р6М5.
При черновом и чистовом фрезеровании концевыми фрезами медных и алюминиевых сплавов применяют инструменты с материалом режущей части - Р6М5.
Материалом сверл для обработки медных и алюминиевых сплавов являются - ВК4, ВК6, ВК8, Р6М5.
Материалом зенкеров для обработки медных и алюминиевых сплавов являются - ВКЗ, ВКЗМ, ВК4, ВК6М, ВК6М, ВК8, Р6М5.
Этап 3. Расчет геометрических параметров режущего инструмента, отражающих специфику обработки на станке с ЧПУ
Переход 1 – черновое фрезерование основной открытой зоны 1
Для фрезерования открытой зоны 1 берется торцовая фреза.
Глубина чернового фрезерования принята равной .
Для обработки следует взять фрезу с диаметром, позволяющим обработать поверхность в 2 строки, так как схема закрепления не позволяет провести обработку в одну строку.
Ширина заготовки принимается (прилив обработается частично, не затрагивая отверстия), количество проходов . Выбег фрезы примем . Из этого следует, что минимальный диаметр фрезы должен быть равен:
Примем ближайшее большее значение Фреза 2210-0073 ГОСТ 9304-69.
Переход 2 - Черновое фрезерование основной открытой зоны 2
Так как, методом копирования требуемую точность соблюсти не удастся, то фрезу следует выбрать с учетом радиусов сопряжений – . Обработка будет проводиться методом – обкатки.
Также учитываем, что при чистовой обработке требуется пройти между отверстием прилива и стенкой детали, не задев отверстие с находящимся в нем базовом пальце.
С учетом данных требованием принимаем
По условию жесткости
Так как выбираем концевую фрезу с осевым врезанием. Фреза 2223-2959R по легким сплавам.
Расчет длины режущей части:
Переход 3 - Черновое фрезерование основной закрытой зоны 3
Для определения диаметра обработки внутреннего контура справедлива формула:
, где
- максимальный припуск при обработке внутреннего угла должен быть не более (0,2…0,3)D ( )
- припуск для чистовой обработки контура, мм ( )
- наименьший угол сопряжения сторон в данном контуре, град ( )
D – диаметр окружности, сопрягающей стороны контура, равный диаметру фрезы при чистовой обработке ( ) тогда:
Предварительно примем диаметр концевой фрезы для черновой обработки закрытой зоны 3: ГОСТ 17026-71.
Так как величина радиуса сопряжения rтип стенки с полкой меньше величин припусков по стенке и полке, то радиус заточки примем r=0,5мм.
Расчет длины режущей части:
Переход 4,5 - Черновое и чистовое фрезерование основной открытой зоны 4
Аналогично первому переходу примем фреза 2210-0073 ГОСТ 9304-69.
Переход 6 - Черновое фрезерование основной закрытой зоны 5
Так как в случае необходимости врезания по наклонной линии должно быть обеспечено перемещение фрезы без зарезов колодца на длине не менее трех диаметров фрезы. По условию радиус сопряжения равен 10, то примем диаметр фрезы равный .
По условию жесткости Так как высота колодца равна , то обработка будет проводиться в 2 прохода.
С учетом всех условий выбираем фрезу – Фреза концевая 2223-2935R по легким сплавам.
Так как величина радиуса сопряжения стенки с полкой rтип=2 мм больше величины припуска по стенке , и полке , то
Выберем из стандарта 2 мм
Расчет длины режущей части: .
Переход 7 - Чистовое фрезерование основной закрытой зоны 5 и дополнительных зон 6
Соответствует переходу №6. Фреза концевая 2223-2935R по легким сплавам.
Переход 8 - Чистовое фрезерование основной открытой зоны 1
Аналогично переходу №5. Фреза 2210-0073 ГОСТ 9304-69.
Переход 9 - Чистовое фрезерование основной закрытой зоны 3 и дополнительных зон 7
Для чистовой обработуи выбираем данные параметры.
Dчист=10мм
,но так как чистовая обработка осуществляется обкаткой ( то примем
Радиус галтели равен 0,5 мм, следовательно радиус заточки возьмем r=0,5мм
Расчет длины режущей части:
Переход 10 - Черновое сверление основной закрытой зоны 8
Параметры РИ:
Тип – сверло спиральное (Сверло 2301-3554 ГОСТ 10903-77).
Материал режущей части – Р6М5.
Припуск на зенкерование определяется по формуле:
, где D = 8 – диаметр отверстия
Необходимый диаметр сверла определим по формуле:
Принимаем ближайшее меньшее значение диаметра для сверл с коническим хвостовиком из стандартного ряда: d = 5,8 мм.
Переход 11 - Чистовое зенкерование основной закрытой зоны 8.
Параметры РИ:
Тип – зенкер цельный (Зенкер 2320-2552 ГОСТ 12489-71).
Материал режущей части – Р6М5.
Диаметр РИ -
Глубина резания t := мм
Переход №12 – чистовое фрезерование основной открытой зоны 2.
Аналогично переходу №2.
Параметры режущего инструмента:
Тип – концевая фреза. Фреза 2223-2959R по легким сплавам;
Материал режущей части фрезы – Р6М5.
Диаметр
Скомпонуем полученные расчеты в таблицу:
Таблица 2. Сводная таблица расчета геометрических параметров выбранного инструмента.
№ Перехода | Расчетный диаметр РИ | Расчетный радиус заточки РИ | Расчетная длина режущей части инструмента | Количество проходов |
№1 (чер.фрез зоны №1) | 80 мм | 1 | 10 | 1 |
№2 (чер.фрез зоны №2) | 16 мм | 2 | 36 | 2 |
№3 (чер.фрез зоны №3) | 22 мм | 0,5 | 10 | 1 |
№4 (чер.фрез зоны №4) | 80 мм | 1 | 10 | 1 |
№5 (чист.фрез зоны №4) | 80 мм | 1 | 10 | 1 |
№6 (чер.фрез зоны №5) | 8 мм | 2 | 25 | 2 |
№7 (чист.фрез зон № 5 и №6) | 8 мм | 2 | 25 | 2 |
№8 (чист.фрез зоны №1) | 80 мм | 1 | 10 | 1 |
№9 (чист.фрез зон №3, №7) | 8 мм | 0,5 | 10 | 1 |
№10 (черн.св. зоны №8) | 5,8 мм | - | - | 1 |
№11 (чист.зен. зоны №8) | 8 мм | - | - | 1 |
№12 (чист.фрез зоны №2) | 16 мм | 2 | 36 | 2 |
Проанализировав расчеты, составим таблицу инструментов в соответствии со стандартом:
Таблица 3. Выбранный инструмент в соответствии со стандартом.
№ Перехода |
|
|
|
| Тип крепления | Стандарт |
№1 (чер.фрез зоны №1) | 80 мм | 1 | 45 | 16 | Торцовая шпонка | 2210-0073 ГОСТ 9304-69 |
№2 (чер.фрез зоны №2) | 16 мм | 2 | 50 | 2 | Конус Морзе по СТП. 7109-2001 | 2223-2959R |
№3 (чер.фрез зоны №3) | 22 мм | 0,5 | 30 | 2 | См. №2 | 2223-2973R |
№4 (чер.фрез зоны №4) | 80 мм | 1 | 45 | 16 | См. №1 | См. №1 |
№5 (чист.фрез зоны №4) | 80 мм | 1 | 45 | 16 | См. №1 | См. №1 |
№6 (чер.фрез зоны №5) | 8 мм | 2 | 40 | 2 | См. №2 | 2223-2935R |
№7 (чист.фрез зон № 5 и №6) | 8 мм | 2 | 40 | 2 | См. №2 | 2223-2935R |
№8 (чист.фрез зоны №1) | 80 мм | 1 | 45 | 16 | См. №1 | См. №1 |
№9 (чист.фрез зон №3, №7) | 8 мм | 0,5 | 20 | 2 | См. №2 | 2223-2933R |
№10 (черн.св. зоны №8) | 5,8 мм | - | 63 | - | Конус Морзе 1 | 2301-3554 ГОСТ 10903-77 |
№11 (чист.зен. зоны №8) | 8 мм | - | 75 | - | Конус Морзе 1 | 2320-2552 ГОСТ 12489-71 |
№12 (чист.фрез зоны №2) | 16 мм | 2 | 50 | 2 | См. №2 | 2223-2959R |
7.2.3. Выбор вспомогательного инструмента
Выбор инструментальной оправки
Для крепления торцовой фрезы требуется оправка (рис. 5) ГОСТ 26538-85.
Рис. 7.5 Оправка с конусом 7:24 для насадных торцовых фрез
Для крепления инструмента с конусом Морзе требуется сборная оправка.
Рис. 7.6 Сборная оправка для инструмента с коническим хвостовиком
1 – корпус; 2 – шпонка; 3 – втулка; 4 – винт; 5 – гайка; 6 – винт; 7 – прокладка; 8 – инструмент
Рис. 7.7 Параметры, задаваемые в УП для фрезы, установленной в оправку
7.2.4. Выбор приспособление
Приспособление требуется для поднятия заготовки над столом. Это нужно, чтобы выполнить сверление сквозных отверстий. Приспособления должны обеспечивать условия для быстрой, точной, многократной установки и зажима заготовки, удобный доступ к ней режущего инструмента при минимальном количестве ее перестановок.
Приспособление требуется для поднятия заготовки над столом. Это нужно, чтобы выполнить сверление сквозных отверстий. Приспособления должны обеспечивать условия для быстрой, точной, многократной установки и зажима заготовки, удобный доступ к ней режущего инструмента при минимальном количестве ее перестановок.
Для правильного выбора приспособления для изготовления детали «Корпус 11 » необходимо удовлетворить следующие требования, предъявляемые к приспособлениям:
- Точная ориентация приспособления с закрепленной на нем заготовкой в системе координат станка и размерная увязка контура обрабатываемой детали с точкой начала обработки Ps.
- Рациональное размещение приспособления с деталью, обеспечивающее равномерный износ передачи.
- Обеспечение максимальной жесткости системы «деталь – приспособление – стол » .
- Обеспечение минимальной высоты выступающих над деталью элементов приспособления в целях уменьшения длины инструмента, следовательно, повышения его жесткости.
- Использование откидных прихватов в целях обеспечения полного цикла обработки детали.
Для базирования детали будет использоваться специальная подкладная плита. Для этого в приспособлении выполнены 2 ступенчатых отверстия, при перевороте на базу Б сменные пальцы остаются на том же месте, так как заготовка имеет два прилива с отверстиями на одной оси. Для расположения приспособления на столе станка в приспособлении выполнены сквозное центровое отверстие и шпоночный паз.
7.3. Назначение нулевой точки детали W и исходной точки Ps программы
Задание нулевой точки детали W в системе координат станка. Расположение нулевой точки детали задается относительно нулевой точки станка М. Расстояние между нулем станка М и нулевой точкой детали W называется смещением нуля отсчета. Оно определяется как смещение по каждой из трех осей координат и обозначается как ZMW, XMW, YMW
Точку начала координат детали назаначают свободно, однако, стремятся к совмещннию точки с началом отсчета размеров на чертеже. В этом случае можно использовать размерные данные непосредственно с чертежа. Поэтому помести точку начала отсчёта координат детали W в левый нижний угол.
Рис.9.8. Положение нулевой точки детали W в системе координат
Задание исходной точки Ps программы
Исходная точка программы Рs будет являться первой точкой движения инструмента по УП. Ее положение назначают исходя из удобства доступа оператора к детали, установленной в приспособлении в рабочей зоне станке (удобство настройки станка). А также для минимизации рабочих ходов исполнительного органа. Инструментальный магазин станка находится в левом верхнем углу рабочей области станка. Поэтому для вертикальных фрезерных станков точку Рs назначают в верхнем левом углу системы координат детали Хд, Yд, Zд (Рис.6).
Рис.9.9. Положение исходной точки программы Ps в системе координат детали W
Минимальное расстояние для выбранного приспособления
Файлы условия, демо
Характеристики курсовой работы
Список файлов
