Курсовая работа: ГПМ на базе токарного многоцелевого станка для изготовления деталей газотурбинных установок
Описание
Руководитель: В.Б.Мещерякова
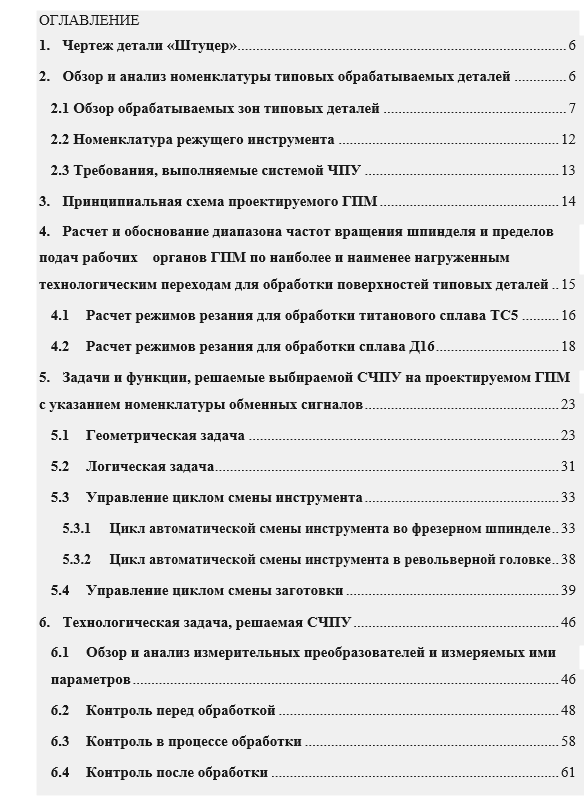
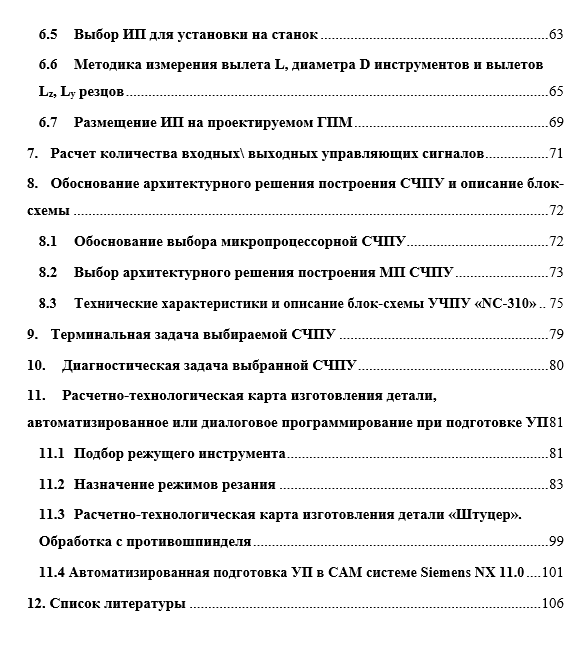
План пояснительной записки:
1. Чертеж детали " Штуцер ".
2. Обзор и анализ номенклатуры типовых обрабатываемых деталей.
3. Принципиальная схема проектируемого ГПМ.
4. Расчет и обоснование диапазона частот вращения шпинделя и пределов подач рабочих органов ГПМ по наиболее и наименее нагруженным технологическим переходам для обработки поверхностей типовой детали " Штуцер ".
5. Расчет мощности и выбор электродвигателей рабочих органов ГПМ.
6. Задачи и функции, решаемые выбираемой СЧПУ на проектируемом ГПМ с указанием номенклатуры обменных сигналов.
7. Технологическая задача СЧПУ.
8. Расчет количества входных выходных управляющих сигналов.
9. Основные технические характеристики проектируемого ГПМ.
10 Обоснование архитектурного решения построения СЧПУ и описание блок-схемы.
11. Терминальная задача выбираемой СЧПУ12. Диагностическая задача СЧПУ.
13. Технические характеристики СЧПУ.
14. Расчетно-технологическая карта изготовления детали, автоматизированное или диалоговое программирование при подготовке УП.
- Обзор и анализ номенклатуры типовых обрабатываемых деталей
Номенклатура деталей:
- Штуцер. Материал – Д16. Габаритные размеры: 560х417х417
- Вал. Материал – 40ХН. Габаритные размеры: 300х300х358
- Лопатка турбины. Материал - ТС5. Габаритные размеры: 265х68х45
Номенклатура режущего инструмента
Поскольку все детали изготовлены по 7 квалитету точности, все зоны подлежат черновой, получистовой и чистовой обработке.
Для токарной обработки зон 1, 2, 4-6, 9, 10-16, 25, 30-33, 39, 45, 50-52, 55, 57-64, 67, 68, 72 требуются черновые, получистовые и чистовые проходные и расточные резцы с твердосплавными пластинами.
Для токарной обработки зон 3, 8, 54, 56 требуются канавочные резцы различных размеров.
Для обработки зон 7, 53 требуются резьбовые резцы.
Зоны 17, 22, 45, 66 требуют для обработки сверло, зенкер и развертку.
Зона 17 обрабатывается метчиком.
Для обработки зон 18, 19, 44, 71 требуется цековка.
Для фрезерной обработки зон 20, 21, 27, 26, 24, 23, 43, 42, 41, 38, 48, 69, 70 требуются черновые, получистовые и чистовые концевые и торцевые фрезы различных диаметров и углов заточки.
Для обработки зоны 28 требуется резьбовая фреза.
Для обработки зон 47, 49 требуется сферическая фреза.
Для обработки зон 65, 73 требуются две чашечные фрезы.
В итоге получаем, что минимальное число инструментов в инструментальном магазине должно быть не менее 20 шт, а также в револьверной головке 8 шт.
2.3 Требования, выполняемые системой ЧПУ
- Черновая, получистовая и чистовая обработка зон (24, 28, 38, 39, 43, 44, 48) при использовании линейной интерполяции по координатам X, Y, Z от 1 до 3 одновременно.
- Черновая, получистовая и чистовая обработка зон (1, 3 – 6, 8 – 11, 14, 15, 23, 26, 30 – 33, 35, 40, 41, 42, 45, 52 – 54, 56 – 59, 61 – 66, 71, 72) при использовании линейной интерполяции по координатам V, W от 1 до 2 одновременно.
- Черновая, получистовая и чистовая обработка зон (2, 13, 24, 29, 37, 39, 43, 50, 60, 65, 70, 71) при использовании круговой интерполяции по координатам в плоскостях OXY, OXZ, OZY, OVW
- Черновая, получистовая и чистовая обработки зон при использовании оси C как позиционной (16, 17, 18, 68, 69), как формообразующей (7, 55).
- Черновая, получистовая и чистовая обработки зон при использовании оси C1 как позиционной (19, 20, 21, 22, 46, 47), как формообразующей (27).
- Черновая, получистовая и чистовая обработки зон при использовании оси А как позиционной (27), как формообразующей (75).
- Черновая, получистовая и чистовая обработки зон при использовании сплайновой интерполяции (49).
- Нарезание резьбы в зонах обработки (53, 17) в направлении осей Z и Y.
- Одновременное вращение шпинделя и противошпинделя при обработке зон (38-40, 42-47, 49).
- Черновая получистовая и чистовая обработка зон (52,55) при управлении осями XYZA (фрезерная головка) и осями VW (револьверная головка), при одновременном управлении Z и W.
- Перехват заготовки при управлении задней бабкой (осью R).
- Поворот фрезерного шпинделя (ось B) на 180 градусов при управления обработкой в противошпинеделе.
- Принципиальная схема проектируемого ГПМ
На основе проведенного анализа зон детали выбирается ГПМ. Поскольку детали являются телами вращения в которых присутствуют сложные поверхности, поэтому выбираем ГПМ на основе токарного многоцелевого станка.
Поскольку обработка ведется большим количеством инструмента, а также в связи с наличием необходимости переустановки заготовки на станок, с целью экономии времени вводятся устройство смены столов спутников и смены инструмента.
Компоновочное решение проектируемого ГПМ приведено на рисунке 6.
Рисунок 6. Компоновка проектируемого ГПМ
- Расчет и обоснование диапазона частот вращения шпинделя и пределов подач рабочих органов ГПМ по наиболее и наименее нагруженным технологическим переходам для обработки поверхностей типовых деталей
Для расчета диапазона частот вращения шпинделя и пределов рабочих подач необходимо о определить самый тяжёлый для обработки материал и самый легкий. Это мы можем сделать, оценив удельную силу резания – сила резания, приходящаяся на 1 мм2 снимаемой стружки, каждого материала из номенклатуры обрабатываемых изделий.
Удельные силы резания:
Сталь 40Х – 1675 Н/мм2
Сплав Д16 – 700 Н/мм2
Титановый сплав ТС5 – 3300 Н/мм2
Следовательно, максимальные усилия резания будут возникать при обработке титанового сплава ТС5, наименьшие при обработке алюминиевого сплава Д16.
Так как в проектируемом ГПМ присутствует токарный и фрезерный шпиндели, то расчет режимов резания будет вести как для токарных операций, так и для фрезерных операций. Наибольшие усилия резания возникают при черновых проходах, а наибольшие скорости резания – при чистовых проходах.
- Расчет режимов резания для обработки титанового сплава ТС5
Режимы резания для титанового сплава ТС5 назначаются согласно справочнику «Режимы резания труднообрабатываемых материалов » . [7]
Точение
Наиболее нагруженная зона – предварительная токарная обработка зоны 47. Величина снимаемого припуска за проход – 8 мм. Диаметр заготовки – 320 мм. Сечение державки резца – 32х25 мм.
Тогда, согласно [7], выбираем величину подачи S = 0,5 мм/об.
Скорость резания V рассчитывается по следующей формуле:
для сплава ТС5
Осевая составляющая силы резания Pz рассчитывается по нижеприведенной формуле:
для сплава ТС5
Частота вращения привода главного движения n, рассчитывается по следующей формуле:
Мощность привода главного движения:
Следовательно, для наиболее нагруженной зоны 47, при обработке титанового сплава ТС5 принимаются режимы резания, приведенные в таблице 1.
Таблица 1. Режимы токарной обработки сплава ТС5
t, мм | S, мм/об | V, м/мин | Pz, Н | n, мин-1 | N, кВт |
8 | 0,5 | 32 | 12000 | 31,8 | 9,33 |
Фрезерование
Далее рассчитаем необходимую мощность двигателя фрезерного шпинделя.
Диаметр концевой фрезы – 50 мм.; число зубьев фрезы – 6; ширина срезаемого слоя – 50 мм, глубина резания – 5 мм.
Подача на зуб выбирается по справочнику [7], тогда Sz = 0,12 мм/зуб.
Скорость резания при обработке титановых сплавав концевыми фрезами:
Режимы резания при черновом фрезеровании сплава ТС5 концевой фрезой приведены в таблице 2.
Таблица 2. Режимы фрезерования сплаваТС5
t, мм | S, мм/об | V, м/мин | S, мм/мин | n, мин-1 | N, кВт |
5 | 0,12 | 67 | 305 | 425 | 6,59 |
- Расчет режимов резания для обработки сплава Д16
Точение
Значения подач при наружном продольном точении и подрезании торцов выбирают в зависимости от обрабатываемого материала, диаметра детали, глубины резания. Выбранное значение умножают на поправочные коэффициенты. [6]
Наименее нагруженная зона при токарной обработки детали из сплава Д16 – это чистовая обработка зоны 2 наружного контура
Подача при чистовом точении определяется по формуле:
где – справочная подача, мм/об
– поправочный коэффициент, зависящий от свойств обрабатываемого материала
- поправочный коэффициент, зависящий от схемы установки заготовки
– поправочный коэффициент, зависящий от радиуса вершины резца
– поправочный коэффициент, зависящий от кинематического угла в плане
– поправочный коэффициент, зависящий от квалитета обрабатываемой детали
Скорость резания при чистовом точении определяется по следующей формуле:
где
– поправочный коэффициент, зависящий от группы обрабатываемости материала
– поправочный коэффициент, зависящий от жесткости станка
– поправочный коэффициент, зависящий от твердости обрабатываемого материала
– поправочный коэффициент, зависящий от геометрических параметров резца
– поправочный коэффициент, зависящий от периода стойкости инструмента
поправочный коэффициент, зависящий от наличия охлаждения
Чистовая обработка зоны 2
Инструмент – проходной резец, главный угол в плане 93°, радиус вершины 0,4 мм, материал пластины – ВК6.
Глубина резания 0,5 мм.
Подача:
= 0,09 мм/об; =1,25; =1,0; =0,85; =1,0; = 0,85;
Скорость резания:
=577 м/мин; =1,5; =1,0; =1,0; =1,5; =1,0; =1,0
Частота вращения шпинделя:
Фрезерование
Для чистовой обработки величину подачи определяют в зависимости от обрабатываемого материала, диаметра и числа зубьев фрезы, ширины и глубины фрезерования, а также жесткости системы станок-приспособление-инструмент-деталь. Выбранное значение умножают на поправочные коэффициенты. [6]
Подача при черновом, получистовом и чистовом фрезеровании концевыми фрезами определяется по формуле:
где – справочная подача на зуб, мм/зуб
– поправочный коэффициент, зависящий от твердости обрабатываемого материала
– поправочный коэффициент, зависящий от материала режущей части фрезы
– поправочный коэффициент, зависящий от отношения фактического числа зубьев к нормативному
– поправочный коэффициент, зависящий от отношения вылета фрезы к ее диаметру
Величину скорости резания выбирают в зависимости от обрабатываемого материала, диаметра и числа зубьев фрезы, ширины и глубины фрезерования, а также выбранного значения подачи.
Скорость резания при чистовом, фрезеровании концевыми фрезами определяется по следующей формуле:
где
– поправочный коэффициент, зависящий от группы обрабатываемости материала
– поправочный коэффициент, зависящий от твердости обрабатываемого материала
– поправочный коэффициент, зависящий от материала режущей части фрезы
– поправочный коэффициент, зависящий от периода стойкости инструмента
– поправочный коэффициент, зависящий от отношения вылета фрезы к ее диаметру
– поправочный коэффициент, зависящий от состояния поверхности заготовки
поправочный коэффициент, зависящий от наличия охлаждения
Рассчитаем режимы резания при чистовом фрезеровании зоны 23
Концевая фреза Dфрезы = 4 мм, z = 3, lрч = 80, Материал – Р6М5
B = 5 мм, t = 0,5 мм.
Согласно [6], выбираем справочную подачу, скорости резания и определяем поправочные коэффициенты.
Подача
= 0,06 мм/зуб; = 1,1; = 1,0; = 1,0; = (20/5=4)=0,85
Тогда,
Скорость резания:
= 62 м/мин; = 1,25; =1,0; = 1,0; = 1,25; = (5/6=0,83)=1,0; = 1,0; =1,0
Тогда скорость резания будет равна:
Частота вращения фрезерного шпинделя:
Подача в мм/мин:
Получаем следующие результаты:
Необходимая мощность двигателя фрезерного шпинделя – 6,59 кВт
Необходимая максимальная частота вращения фрезерного шпинделя – 7722 мин-1
Необходимая мощность двигателя главного шпинделя – 9,33 кВт
Необходимая максимальная частота вращения главного шпинделя–4134 мин-1
Поэтому выбираем в качестве привода главного движения выбираем мотор-шпиндель фирмы Siemens модели 2SP1202-1
- Максимальная частота вращения – 6000 мин-1
- Мощность – 12 кВт
В качестве привода фрезерного шпинделя также выбираем мотор-шпиндель фирмы Siemens модели 2SP1102-1
- Максимальная частота вращения – 12000 мин-1
- Мощность – 9 кВт
- Задачи и функции, решаемые выбираемой СЧПУ на проектируемом ГПМ с указанием номенклатуры обменных сигналов
- Геометрическая задача
В рамках геометрической задачи осуществляется формообразование поверхности детали.
В геометрическую задачу входит:
- Ввод и хранение СПО
- Ввод, редактирование и хранение УП
- Интерпретация кадра
- Интерполяция
- Управление приводами
- реализация обратной связи по положению
- реализация обратной связи по скорости
- аварийный останов
- работа УЧПУ в относительных или абсолютных координатах
- согласование УЧПУ и ИП
- автоматический выход в точку М
- автоматический выход в точку R
- автоматический выход в точку N
- автоматический выход в точку F
- Работа с технологическими циклами
- Коррекция УП
Ввод и хранение СПО
Специальное программное обеспечение (СПО) обеспечивает распределение ресурсов устройства ЧПУ, а также организацию процесса обработки, ввода – вывода, редактирования и управления данными [Error! Reference source not found.]. Для СПО используется энергонезависимая память. Ввод СПО осуществляется с ЭВМ верхнего уровня, с USB или дискового носителя.
Ввод, редактирование и хранение УП
Управляющая программа (УП) изменяется при изготовлении разных деталей. Она может вводиться покадрово или целиков следующими способами: с USB или дискового носителя, с ЭВМ верхнего уровня, с пульта УЧПУ.
Интерпретация кадра
Функция интерпретации кадра необходима для того, чтобы перевести команды, записанные в кадрах УП, в вид, понятный СЧПУ.
При интерпретации кадра решаются следующие задачи:
- Распределение информации кадра по адресам памяти, соответствующим буквенно-цифровому коду, в том числе перевод чисел из десятичной системы в двоичную.
- Анализ вспомогательной функции М и формирование кодов управления электроавтоматикой станка.
- Перевод размерных величин перемещений и скоростей в машинные единицы путём умножения на масштабные коэффициенты.
- Анализ кодов учёта корректирующих поправок на размеры инструмента и коррекции траектории.
- Расчёт исходных данных для интерполяции, анализ признаков торможения и расчёт тормозного пути.
Интерполяция
Интерполяция - процесс получения с требуемой точностью координат промежуточных точек траектории по координатам вспомогательных опорных точек аппроксимируемого контура с величиной дискреты СЧПУ и заданной функцией интерполяции.
На разрабатываемом ГПМ СЧПУ обеспечивает следующие виды интерполяции: G01 – линейная; G02, G03 – круговая в плоскостях ХУ, XZ, YZ.
Управление приводами
Реализация обратной связи по положению
Реализацию обратной связи по положению рассмотрим на примере управления приводом перемещения фрезерной шпиндельной бабки (Ось X). На двигатель М1 из СЧПУ подается сигнал Xзад о перемещении рабочего органа на заданное расстояние. Двигатель через муфту связан с ШВП, которая осуществляет перемещение рабочего органа. Оптический линейный измерительный преобразователь ИП1 модели ЛИР – 9М посылает в СЧПУ сигнал Хфакт о фактическом положении рабочего органа. Если разница фактического Хфакт и заданного Xзад положения рабочего органа не равна нулю и превышает допустимое значение, то на двигатель М1 посылается сигнал ΔX= Хфакт – Xзад о перемещении рабочего органа для устранения рассогласования.
Рисунок 6. Управление приводом перемещения фрезерной шпиндельной бабки (Ось X)
Перемещение каретки осуществляется за счет синхронного вращения двигателей М4 и М5. На каждый двигатель из СЧПУ поступает сигнал Yзад о перемещении каретки на заданное расстояние. На данном приводе установлены два измерительных преобразователя ИП4 и ИП5 модели ЛИР – 9М, которые посылают в СЧПУ сигналы Y1факт и Y2факт о фактическом положении. Затем каждый из них сравнивается с Yзад и, если есть разница, превышающая допустимое значение, то на соответствующие двигатели подаются сигналы ΔY1=Y1факт – Yзад и ΔY2=Y2факт – Yзад. Применение двух измерительных преобразователей при такой компоновке позволяет устранить возможные перекосы каретки, возникающие в процессе работы станка.
Рисунок 7. Управление приводом перемещения каретки (Ось Y)
Реализация обратной связи по скорости
Реализацию обратной связи по скорости рассмотрим на примере управления приводом перемещения вертикально суппорта (Ось V). На двигатель М7 из СЧПУ подается сигнал Fзад о перемещении рабочего органа с заданной скоростью. Оптический линейный измерительный преобразователь ИП7 модели ЛИР – 9М посылает в СЧПУ сигнал Fфакт о фактической скорости рабочего органа. Если разница фактической Fфакт и заданной Fзад скорости рабочего органа не равна нулю и превышает допустимое значение, то на двигатель М7 посылается сигнал ΔF= Fфакт – Fзад о изменении скорости перемещения рабочего органа для устранения рассогласования.
Рисунок 8. Управление приводом перемещения вертикального суппорта (Ось V)
При управлении скоростью перемещения салазок на каждый двигатель М2 и М3 из СЧПУ поступает сигнал Fзад о перемещении каретки с заданной скоростью. Измерительные преобразователи ИП2 и ИП3 модели ЛИР – 9М, установленные на данном приводе посылают в СЧПУ сигналы F1факт и F2факт о фактической скорости. Затем каждый из них сравнивается с Fзад и, если есть разница, превышающая допустимое значение, то на соответствующие двигатели подаются сигналы ΔF1=F1факт – Fзад и ΔF2=F2факт – Fзад. Система ЧПУ работает с двигателями М2 и М3 для поддержания их синхронного вращения.
Рисунок 9. Управление приводом перемещения салазок (Ось Z)
Аварийный останов привода
Чтобы исключить перемещение рабочего органа за пределы рабочего органа устанавливают 6 концевых выключателей: 2 – для плавного торможения, 2 – для отключения двигателя, крайние 2 – для авариного отключения СЧПУ.
Работа УЧПУ в абсолютной или относительной системе координат
Эта функция задается в УП с помощью подготовительных функций G90, G91. Без сигналов, соответствующих этим функциям не будет реализованы алгоритмы интерполяции и рабочие органы не начнут перемещаться.
Согласование СЧПУ и ИП
Так как в проектируемом ГПМ применяются только дискретные ИП марки ЛИР, поэтому необходимости в согласовании СЧПУ и ИП нет.
Автоматической выход рабочего органа в нулевую точку станка
Положение рабочего органа в точке М фиксируется ИП, установленным на данном рабочем органе. На двигатели подается сигнал, соответствующий подготовительной функции G53. При достижении точки М, ИП выдает сигнал «0 » . Особенностью работы ГПМ на базе станка DMG NT4200 является то, что рабочие органы не могут выйти в точку М ни одновременно, ни последовательно. Рабочие органы могут занят положение, соответствующее проекции точки М на данную ось только при движении из референтной точки R. Поэтому для перемещения рабочих органов в точку М в моем случае используются подготовительные функции М51, М52 и М52, осуществляющие выход рабочих органов в точку М по осям X, Y и Z соответственно.
Реферирование
Функция предполагает автоматический выход рабочего органа в референтную точку R станка. На проектируемом ГПМ точка R необходима для уменьшения величин холостых ходов. На двигатели рабочих органов, участвующих продается сигнал, соответствующий подготовительной функции G28. При достижении рабочими органами точки R каждый ИП посылает сигнал «R » на УЧПУ.
Автоматический выход рабочих органов в точку смены инструмента
Перед сменой инструментов необходимые рабочие органы выходят в точку N по сигналу, соответствующему подготовительной функции G14. При достижении рабочими органами точки N в СЧПУ подаются осведомительные сигналы 5, 22, 28, 13, 20, снятые с концевых выключателей.
Автоматический выход рабочего органа в точку смены заготовки
При выполнении цикла смены заготовки рабочие органы должны выйти в точку F, в которой развернется цикл смены. На проектируемом ГПМ точка выход в точку смены заготовки осуществляется перемещением задней бабки, однако, это величина этого перемещения будет задаваться технологом в УП перед циклом смены заготовки для каждой партии деталей. Таким образом автоматический выход в точку F является программируемым и не входит в цикл смены заготовки.
Работа с постоянными технологическими циклами
СЧПУ может автоматически рассчитывать и формировать траектории движения инструмента, если в УП заданы постоянные технологические циклы обработки.
Цикл – процесс отдельных движений станка для различных видов обработки, выполняемых специальными инструментами. Каждый постоянных цикл имеет определенный формат записи, который записывается и вызывается при необходимости в кадрах основной УП.
На проектируемом ГПМ применяются следующие циклы: G70, G81, G82, G83, G89, G84, G110, G792, G817, G836. Отмена технологических циклов осуществляется при помощи подготовительной функции G80.
Коррекция УП
СЧПУ может автоматически пересчитывать координаты опорных точек траекторий, заданных в УП, с учетом фактически используемых параметров инструмента. Используются подготовительные функции: G40, G41, G42, G43, G44.
- Логическая задача
В рамках логической задачи осуществляется управление цикловой автоматикой станка.
В логическую задачу входит:
- Управление приводом главного движения
- включение и выключение привода главного движения
- задание частоты вращения и диапазона частот вращения
- реализация обратной связи по скорости
- реверс
- согласование частоты вращения с величиной подачи при резьбонарезании
- аварийный останов привода
- управление приводом главного движения как угловой координаты
- ориентированный останов шпинделя
- Реализация цикла автоматической смены инструмента
- Реализация цикла автоматической смены заготовки
- Компенсация УЧПУ кинематических погрешностей станка
Рисунок 10. Управление приводом вращения шпинделя
Включение и выключение привода главного движения
Включение и выключение привода главного движения осуществляется при помощи вспомогательных функций М03, М05.
Задание частоты вращения и диапазона частот вращения шпинделя
Задание частоты вращения шпинделя осуществляется в УП при задании слова S.
Реализация обратной связи по скорости
Осуществляется подобно реализации обратной связи по скорости линейного перемещения, описанного в разделе 5.1.
Реверс
Реверс дает возможность обрабатывать зеркальные детали по одной УП, а также необходим при выходе метчика из отверстия с нарезанной резьбой. Реализуется вспомогательной функцией М04.
Согласование частоты вращения с величиной подачи при резьбонарезании
Согласование частоты вращения с величиной подачи осуществляется при задании подготовительной функции G33, сигнал от которой подается на привод главного движения. С ИП привода главного движения снимается сигнал «Р » , который подается на привод перемещения рабочего органа, участвующего ы разьбонарезании.
Аварийный останов привода
Привод главного движения автоматический останавливается в аварийном режиме при увеличении частоты вращения больше допустимой.
Управление приводом главного движения как угловой координаты
Переключение осуществляется по подготовительной функции G27. Данная функция позволяет задать функцию G01 для управления приводом главного движения, а слово S переложить на другой привод.
Ориентированный останов шпинделя
Ориентированный останов шпинделя необходим для автоматического доворота до нужного положения шпинделя для последующего выполнений цикла автоматической смены инструмента. Задается при помощи вспомогательной функции М19. Осведомительный сигнал 45 говорит о том, что шпиндель довернулся до нужного положения и можно начинать цикл смены инструмента.
Рисунок 11. Управление приводом вращения фрезерного шпинделя в режиме точения
- Управление циклом смены инструмента
- Цикл автоматической смены инструмента во фрезерном шпинделе
До начала цикла рабочие органы станка должны быть выведены в точку смены инструмента N по соответствующим координатам. В начале цикла в шпинделе нет инструмента.
Определим вспомогательные функции, используемые в цикле автоматической смены инструмента:
Т01-Т20 – выбор инструмента инструментальном магазине
М06 – цикл смены инструмента во фрезерном шпинделе
М10 – зажим инструмента
М11 – разжим инструмента
Операции, выполняемые по функции Т выполняются во время обработки для уменьшения времени смены инструмента.
Цикл осуществляется в следующей последовательности:
Фун-я | № | Выполняемая операция | Входной сигнал | Выходной сигнал |
Т01-Т20 | Поиск инструмента в инструментальном магазине | Т01-Т20 | 52 | |
Перемещение корпуса автооператора на – 450 мм вдоль оси Z | 52 | 53 | ||
Перемещение руки автооператора на -100 мм вдоль оси Y | 53 | 54 | ||
Перемещение корпуса автооператора на +450 мм вдоль оси Z | 54 | 55 | ||
Перемещение руки автооператора на +100 мм вдоль оси Y | 55 | 56 | ||
М06 | Открытие защитной шторки | М06 | 57 | |
Перемещение салазок на -200 мм вдоль оси Z | 57 | 58 | ||
Разжим инструмента в шпинделе | М11 | 59 | ||
Перемещение руки автооператора на -100 мм вдоль оси Y | 59 | 60 | ||
Поворот руки автооператора на 180o вокруг оси Y | 60 | 61 | ||
Перемещение руки автооператора на +100 мм вдоль оси Y | 61 | 62 | ||
Зажим инструмента в шпинделе | М10 | 63 | ||
Перемещение салазок на +200 мм вдоль оси Z | 63 | 64 (сним М06) | ||
Закрытие защитной шторки |
| 65 | ||
Т01-Т20 | Перемещение руки автооператора на -100 мм вдоль ось Y | 65 | 66 | |
Перемещение корпуса автооператора на -450 мм вдоль оси Z | 66 | 67 | ||
Перемещение руки автооператора на +100 мм вдоль оси Y | 67 | 68 | ||
Перемещение корпуса автооператора на +450 мм вдоль оси Z | 69 | 69 |
Рисунок 12. Схема поиска инструмента в инструментальном магазине
Рисунок 12. Схема перемещения корпуса автооператора на +- 450 мм вдоль оси Z
Рисунок 13. Схема перемещения руки автооператора на +- 100 мм вдоль оси Y
Рисунок 14. Схема открытия/ закрытия защитной шторки
Рисунок 15. Схема перемещения салазок на +- 200 мм вдоль оси Z
Рисунок 16. Схема разжима/зажима инструмента в шпинделе
Рисунок 17. Схема поворота руки автооператора на 180 вокруг оси Y
- Цикл автоматической смены инструмента в револьверной головке
Определим вспомогательные функции, используемые в цикле автоматической смены инструмента:
Т20-Т28 – выбор инструмента в револьверной головке
М15 – цикл смены инструмента в револьверной головке
Цикл осуществляется в следующей последовательности:
Фун-я | № | Выполняемая операция | Входной сигнал | Выходной сигнал |
М15 | Расфиксация механизма поворота револьверной головки | М15 | 70 | |
Т20-Т28 | Поворот револьверной головки | Т20-Т28 | 71 | |
М15 | Фиксация механизма поворота револьверной головки | 71 | 72 |
Рисунок 18. Схема расфиксации механизма поворота РГ
Рисунок 19. Схема поворота револьверной головки
Рисунок 20. Схема фиксации механизма поворота револьверной головки
- Управление циклом смены заготовки
До начала цикла рабочие органы станка должны быть выведены в точку смены инструмента F по соответствующим координатам.
Определим вспомогательные функции, используемые в цикле автоматической смены инструмента:
М50 –цикл захвата заготовки из накопителя заготовок
М52 – цикл складирования готовых деталей в накопитель
М54 – открытие защитной дверцы
М55 – зажим схвата автооператора смены заготовок
М56 – зажим кулачков трехкулачкового патрона шпинделя
М57 – разжим кулачков трехкулачкового патрона шпинделя
М58 – зажим кулачков трехкулачкового патрона противошпинделя
М59 – разжим кулачков трехкулачкового патрона противошпинделя
М60 – цикл загрузки заготовки в станок
М62 цикл выгрузки готовой детали из станка
Операции, выполняемые по функции М50 и М52 выполняются во время обработки для уменьшения времени смены заготовки.
Цикл осуществляется в следующей последовательности:
Фун-я | № | Выполняемая операция | Входной сигнал | Выходной сигнал |
М50 | Перемещение основания автооператора на – 800 мм вдоль оси Z | М50 | 73 | |
Поворот корпуса автооператора на -90о вокруг оси Y | 73 | 74 | ||
Перемещение руки автооператора на – 200 мм вдоль оси X | 74 | 75 | ||
Зажим схвата | М55 | 76 | ||
Перемещение корпуса руки автооператора на +100 мм вдоль оси Y | 76 | 77 | ||
Перемещение руки автооператора на + 200 мм вдоль оси X | 77 | 78 | ||
Перемещение корпуса руки автооператора на - 100 мм вдоль оси Y | 78 | 79 | ||
Поворот корпуса автооператора на +90о вокруг оси Y | 79 | 80 | ||
Перемещение основания автооператора на + 800 мм вдоль оси Z | 80 | 81 | ||
М54 | Открытие защитной дверцы | М54 | 82 | |
М60 | Поворот корпуса автооператора на +90о вокруг оси Y | М60 | 83 | |
Перемещение руки автооператора на + 200 мм вдоль оси X | 83 | 84 | ||
Разжим кулачков трехкулачкового патрона шпинделя | М57 | 85 | ||
Перемещение основания автооператора на – 200 мм вдоль оси Z | 85 | 86 | ||
Зажим кулачков трехкулачкового патрона шпинделя | М56 | 87 (сним М55) | ||
Разжим схвата |
| 88 | ||
Перемещение основания автооператора на + 200 мм вдоль оси Z | 88 | 89 | ||
М62 | Перемещение основания автооператора на + 200 мм вдоль оси Z | М62 | 90 | |
Зажим схвата | М55 | 91 | ||
Разжим кулачков трехкулачкового патрона противошпинделя | М59 | 92 | ||
Перемещение основания автооператора на - 200 мм вдоль оси Z | 92 | 93 | ||
Перемещение руки автооператора на - 200 мм вдоль оси X | 93 | 94 | ||
Поворот корпуса автооператора на - 90о вокруг оси Y | 94 | 95 (сним М54) | ||
М54 | Закрытие защитной дверцы |
| 96 | |
М52 | Перемещение основания автооператора на + 800 мм вдоль оси Z | М52 | 97 | |
Поворот корпуса автооператора на - 90о вокруг оси Y | 97 | 98 | ||
Перемещение корпуса руки автооператора на + 100 мм вдоль оси Y | 98 | 99 | ||
Перемещение руки автооператора на - 200 мм вдоль оси X | 99 | 100 | ||
Перемещение корпуса руки автооператора на - 100 мм вдоль оси Y | 100 | 101 (сним М55) | ||
Разжим схвата |
| 102 | ||
Перемещение руки автооператора на + 200 мм вдоль оси X | 102 | 103 | ||
Поворот корпуса автооператора на + 90о вокруг оси Y | 103 | 104 | ||
Перемещение основания автооператора на + 800 мм вдоль оси Z | 104 | 105 |
Рисунок 21. Схема перемещения основания автооператора на +- 800 мм вдоль оси Z
Рисунок 22. Схема поворота корпуса автооператора на +-90 вокруг оси Y
Рисунок 23. Схема перемещения руки автооператора на +- 200 мм вдоль оси X
Рисунок 24. Схема разжима/зажима схвата
Рисунок 25. Схема перемещения корпуса руки автооператора на +-100 мм вдоль оси Y
Рисунок 26. Схема открытия/закрытия защитной дверцы
Рисунок 27. Схема разжима/зажима кулачков в шпинделе
Рисунок 28. Схема перемещения основания автооператора на +-200 мм вдоль оси Z
Рисунок 29. Схема разжима/зажима кулачков в противошпинделе
- Технологическая задача, решаемая СЧПУ
- Обзор и анализ измерительных преобразователей и измеряемых ими параметров
В настоящее время практически все металлорежущие станки с ЧПУ оснащаются измерительными системами. Измерительные системы позволяют многократно сократить число брака и простои технологического оборудования на производстве, связанные с выполнением контроля и наладки вручную.
Методы контроля классифицируются по временной последовательности изготовления детали:
Рисунок 30. Классификация методов контроля по временной последовательности
Базовые элементы технологического процесса (заранее)
Виды проверок, относящихся к уровню базовых элементов технологического процесса:
- Проектирование с учетом пригодности для массового производства состоит в подходе к разработке процессов и изделий, основанных на всестороннем понимании существующих возможностей и на стремлении к реализации передового опыта.
- Контроль входных характеристик процесса – включает анализ характера и последствий отказов и аналогичные методы, применение которых позволяет понимать и контролировать все существующие к началу выполнения процесса факторы, которые могут повлиять на результаты процесса обработки.
- Контроль стабильности параметров окружающей среды направлен на учет тех внешних источников отклонений, которые не могут быть устранены заблаговременно, поскольку являются неотъемлемой характеристикой среды, в которой выполняется процесс.
- Системный подход к выбору последовательности операций (технологического маршрута) в процессе изготовления изделий для того, чтобы оптимальным образом обеспечивались автоматизация и стабильность условий выполнения процесса. При этом подразумевается введение на критических этапах обратной связи о ходе процесса.
- Оптимизация состояния станка является неотъемлемой частью всего набора базовых элементов технологического процесса, поскольку на неточном станке невозможно стабильное изготовление точных деталей. Строгая процедура оценки эксплуатационных характеристик станка, калибровка и, если необходимо, восстановление станка позволяют привести его параметры в соответствие с требованиями к технологическому процессу.
- Контроль перед обработкой
Контроль наличия заготовки и определение ее размеров осуществляют при помощи контактного измерительного щупа, установленного во фрезерном шпинделе станка.
В настоящее время на рынке представлено несколько видов измерительных щупов. Фирма Renishaw предлагает следующие варианты конструктивного исполнения измерительных щупов:
- Электроконтный датчик касания с механической системой срабатывания
Рисунок 31. Электроконтактный датчик касания на трех призмах фирмы Renishaw
Три стержня (ролика), расположенные на одинаковом расстоянии друг от друга, опираются на шесть шариков из карбида вольфрама, обеспечивающих шесть точек контакта в системе точного базирования. Посредством этих контактов формируется электрическая цепь. Подпружиненный механизм позволяет щупу датчика отклоняться при соприкосновении с поверхностью детали и обеспечивает возвращение датчика в исходное положение с точностью в пределах 1 мкм, когда щуп отводится от поверхности (в отсутствие касания).
При нагружении пружины создаются пятна контакта, через которые может течь ток. Противодействующие силы в механизме датчика приводят к уменьшению некоторых пятен контакта, вследствие чего повышается сопротивление таких элементов. При контакте (соприкосновении) с деталью переменная сила, воздействующая на пятно контакта, измеряется как изменение электрического сопротивления. Когда сопротивление превышает некоторое пороговое значение, на выходе датчика подается сигнал о срабатывании.
Описанный принцип действия кинематического механизма определяет стадии генерации сигнала срабатывания, показанные ниже, на рисунке 32.
Рисунок 32. Стадии генерации сигнала срабатывания электроконтактного датчика с механической системой срабатывания
Недостаток электроконтактного датчика с тремя базирующими призмами заключается в изменении плеча, в связи с этим наличии погрешности срабатывания в зависимости от направления воздействия на измерительный наконечник.
- Электронный датчик касания с тензоэлементами
Следующей модификацией измерительного щупа стал более точный электронный датчик касания с тензоэлементами. Электронный датчик касания с тензоэлементами изображён на рисунке 33.
Тензометрические датчики размещаются на специально спроектированных элементах, установленных в конструкции датчика, но отдельно от кинематического механизма. Тензометрические датчики расположены таким образом, чтобы регистрировать все усилия на щупе в 3-х направлениях, которые затем суммируются.
При достижении порогового значения в любом направлении генерируется сигнал срабатывания под воздействием сил, которые намного слабее сил, необходимых для срабатывания обычного датчика. В то же время для удерживания щупа в датчиках используется кинематический механизм. Такая система, гарантирует повторяемость при возвращении щупа в исходное положение, что является ключевым фактором обеспечения точных измерений.
Рисунок 33. Электронный датчик касания с тензоэлементами
Процесс измерений полностью независим от кинематического механизма датчика, это обеспечивает высокую степень точности и стабильные характеристиками срабатывания, что обычно недостижимо при использовании датчиков обычной конструкции.
Кроме классификации датчиков по типу срабатывания, существует несколько вариантов передачи сигналов от датчиков в систему ЧПУ.
Выбор конкретной системы передачи сигналов определяется типом используемого датчика и типом станка, на котором он установлен.
Существуют три способа связи СЧПУ и датчика:
- проводная система передачи сигналов
- оптическая система передачи сигналов
- система передачи сигналов по радиоканалу
Проводная система передачи сигналов изображена на рисунке 34. При помощи этой системы соединяют ИП неподвижно установленные на станине или неподвижных узлах станка или на специальном подводящем или быстросъемном приспособлении. Таким образом, чтобы провод не мешал подвижным узлам станка.
Рисунок 34. Кабельная система передачи сигналов
Оптическая система передачи сигналов применяется на многоцелевых станках, на которых датчик касания обычно находится в инструментальном магазине станка и устанавливается в шпиндель. Поэтому датчик не может иметь провода, который будет мешать его перемещениям в рабочей зоне станка, а передача сигналов должна быть бесконтактная и на достаточно большое расстояние.
Рисунок 35. Оптическая система передачи сигналов
Датчик получает сигналы от системы СЧПУ станка и, в свою очередь, передает в систему СЧПУ сигналы о своем состоянии. У датчика два активных режима: режим ожидания и рабочий режим. В режиме ожидания датчик периодически передает и получает сигналы в ожидании сигнала, который переведет его в рабочий режим. В рабочем режиме датчик передает в приемник сигналы о своем состоянии, в том числе данные об уровне зарядке батареи.
Необходимо, чтобы датчик и приемник оптической передачи не выходили за границы конусов излучения друг друга, и между ними все время существовала прямая видимость. Оптическая связь осуществляется с помощью инфракрасных свето- и фотодиодов. На датчике касания установлены один фотодиод для приема сигнала включения и несколько светодиодов для передачи управляющих сигналов. Датчик касания имеет встроенный источник автономного питания. Преимущество оптической связи – в большом расстоянии (до 3–6 м) между датчиком касания и приемо-передающим устройством.
Система передачи сигналов по радиоканалу позволяет установить связь между датчиком касания и СЧПУ станка на больших расстояниях. Частотный диапазон 2,4–2,48 ГГц. Взаимное расположение датчика касания и приемо-передающего устройства должно быть таким, чтобы они находились в пределах рабочих диапазонов друг друга. Прямая видимость между ними не требуется: необходимо лишь, чтобы длина траектории распространения отраженных радиоволн между ними не превышала 15 м. Датчик снабжен приемником и передатчиком и имеется приемо-передающее устройство, установленное неподвижно на станке и соединенное кабелем с системой ЧПУ.
Рисунок 36. Система передачи сигналов по радиоканалу
Контроль наличия инструмента, его целостности и определение его геометрических параметров осуществляется при помощи специальных датчиков. В зависимости от принципа работы датчики наладки инструмента разделяются на 2 категории:
- контактные
- бесконтактные
Фирма Renishaw предлагает следующие датчики для наладки инструмента:
- Устройства наладки инструмента с контактным срабатыванием
- Бесконтактная наладка инструмента с использованием лазерной системы
- Обнаружение неисправного инструмента на базе лазерной одномодульной системы
В устройствах наладки инструмента с контактным срабатыванием применяется те же самые механизмы срабатывания, что и в щуповых контактных датчиках. Все эти механизмы применяются независимо от выполняемых задач, будь то размерный контроль или контроль целостности инструмента. На рисунке 37 показан принцип действия контактного ИП на примере электроконтактного метода срабатывания, рассмотренного ранее.
Рисунок 37. Принцип действия электроконтакного датчика наладки инструмента
Электроконтактные датчики наладки инструмента предназначены для проверки наличия инструмента в шпинделе, измерения его геометрических параметров, таких как, вылет инструмента L и диаметр D.
Рисунок 38. Параметры, контролируемые элетроконтактным датчиком наладки инструмента
В бесконтактных лазерных системах наладки инструмента используется лазерный пучок, идущий от передатчика (источника излучения) к приемнику (рисунок 39). Передатчик и приемник устанавливаются на станке так, чтобы было возможно пересечение траектории пучка режущим инструментом.
Рисунок 39. Бесконтактный датчик наладки инструмента с использованием лазерной системы
При прохождении инструмента сквозь пучок лазерного излучения количество света, попадающего на приемник, уменьшается, в результате чего формируется сигнал срабатывания. В этот момент положение станка фиксируется для получения данных, позволяющих определить размер инструмента. Осуществляя подходы по нескольким направлениям, можно также точно определить все данные по геометрии инструмента. Кроме того, эти системы могут использоваться для обнаружения неисправного инструмента: инструмент быстро перемещается в положение, где он должен пересечь лазерный пучок, и если на приемник попадает свет, то это означает, что режущая кромка инструмента отсутствует.
На рисунке 40 показана последовательность генерации сигнала срабатывания бесконтактного датчика с использованием лазерной системы.
Рисунок 40. Последовательность генерации сигнала срабатывания датчика с использованием лазерной системы
Лазерная одномодульная система для обнаружения неисправного инструмента отличается от вышеприведенного бесконтактного датчика тем, что передатчик и приемник помещен в одном корпусе, но в отличие от предыдущих ИП на приемник не попадает непосредственное излучение от лазера, а только его отражение.
Такие системы предназначены только для контроля целостности инструмента и не могут быть применены для размерного контроля. Однако, они могут применятся для контролирования целостности инструмента непомредственно в процессе обработки.
На рисунке 41 изображен прицип действия лазерной одномодульной системы обнаружения неисправного инструмента.
Рисунок 41. Лазерная одномодульная система обнаружения неисправного инструмента.
Последовательность генерации сигнала срабатывания одномодульной системы обнаружения неисправности инструмента показана на рисунке 42.
Рисунок 42. Последовательность генерации сигнала срабатывания одномодульной системы обнаружения неисправности инструмента
Передача сигналов с СЧПУ осуществляется, как и в случае измерительных щупов, при помощи трех способов связи: проводным, оптическим и по радиоканалу.
- Контроль в процессе обработки
Данный вид контроля широко используется на станках с адаптивной системой управления. Такие станки оснащены большим количеством датчиков, передающих информацию системе ЧПУ для адаптивного контроля процессом обработки.
Усилие резания в случае моем случае можно определить только косвенным путем. Усилие резания пропорционально силе тока, потребляемого двигателем привода главного движения в процессе обработки.
Датчики контроля силы тока в приводе главного движения основаны на эффекте Холла - явление возникновения поперечной разности потенциалов при помещении проводника с постоянным током в магнитное поле.
Ток, протекающий в проводнике, создает вокруг него магнитное поле. Это поле концентрируется в ферромагнитном сердечнике. Сердечник имеет зазор, в котором располагается элемент Холла, чувствительный к плотности магнитного потока в зазоре. Выходной сигнал элемента Холла преобразуется таким образом, чтобы он был в точности пропорционален величине тока в проводнике.
Датчики компенсационного типа, (также называемые датчиками с нулевым потоком) имеют встроенную компенсационную цепь, с помощью которой характеристики датчиков тока, использующих эффект Холла, могут быть существенно улучшены. Диапазон компенсационных датчиков позволяет измерять номинальные токи от нескольких ампер до нескольких сотен кА с точностью около 1 %.
Рисунок 43. Принцип работы датчика тока на эффекте Холла компенсационного типа
Достоинства датчиков тока на основе эффекта Холла
- широкий диапазон измеряемых токов с частотой до 50–100 кГц и выше;
- измеряет постоянный и переменный ток;
- гальваническая развязка;
- высокая точность;
- низкий температурный дрейф;
- линейность;
- небольшие масса-габаритные показатели;
- низкое энергопотребление.
Недостатки:
- высокая стоимость.
Уровень вибрации в основном определяют с помощью акселерометров, они устанавливаются на корпус шпиндельного узла над опорами шпинделя и имеют аналоговый тип выходного сигнала. Резкое повышение уровня вибрации может сигнализировать о неправильном выборе режимов резания. Вибрации, возникающие в станке в процессе обработки в значительной степени, влияют на стойкость инструмента. СЧПУ при необходимости может остановить процесс обработки значительном превышении уровня вибрации или плавно уменьшать скорость вращения шпинделя до момента, когда уровень вибрации не окажется в установленном допуске.
Схема простейшего акселерометра приведена на рисунке 44. Акселерометр состоит из пружины, подвижной массы и демпфера. Пружина крепится к неподвижной поверхности, к пружине крепится масса. С другой стороны, ее поддерживает демпфер, который гасит собственные вибрации груза. Во время ускорения массы деформируется пружина. На этих деформациях и основываются показания прибора. Три таких прибора, объединенные в одну систему и сориентированные по осям позволяют получать информацию о положении предмета в трехмерном пространстве.
Рисунок 44. Схема простейшего акселерометра
Контроль температуры осуществляется в таких местах, как подшипниковые узлы, а также на корпус узлов вблизи обмоток при использовании прямых приводов с целью сохранения работоспособности станка. Термопары устанавливаются непосредственно в место, где необходимо измерить температуру, выходной сигнал является аналоговым.
Принцип работы термопары показан на рисунке 45.
Рисунок 45. Принцип работы термопары
Работа термопары основывается на термоэлектрическом эффекте, открытым Зеебеком в 1821 году. Данный эффект заключается в том, что если последовательно соединить друг с другом два разнородных металлических проводника, образуя таким образом замкнутую электрическую цепь, и в одном месте соединения проводников произвести нагрев, то в цепи возникает электродвижущая сила (ЭДС). Данную электродвижущую силу называют термо-ЭДС. Под действием термо-ЭДС в замкнутой цепи начинает протекать электрический ток.
Таким образом, если место соединения разнородных проводников термопары нагреть, то между несоединёнными (свободными) концами проводников возникнет разность потенциалов, которую можно измерить электроизмерительным прибором. Благодаря современным преобразователям возникающую разность потенциалов можно преобразовать в аналоговый сигнал.
Контроль после обработки
Деталь измеряется уже рассмотренными выше измерительными щупами разных типов, в этом случае измерительные циклы будут более трудоемкие, поскольку конфигурация детали сложнее заготовки.
В настоящее время набирает популярность метод измерения деталей 3Д сканированием (рисунок 46). Такой метод позволяет намного быстрее (по сравнению с щуповыми ИП) проводить измерение деталей, так как измерение проводится не точечным способом, а плоским или объемным фронтом (в зависимости от типа сканера).
Рисунок 46. Измерение детали 3D сканером
Основным достоинством 3D сканеров является то, что по ходу измерения формируется твердотельная модель, которую можно сравнить с базовой моделью и оценить ее точность изготовления.
Однако, таким устройствам присущи два недостатка, которые препятствует массовому внедрению в метрологическое и станочное оборудование: пока еще низкая точность измерения (самые точные экземпляры способны выдавать точность до 0,01 мм) и очень высокая стоимость. Таким образом, на данный момент щуповые ИП сохраняют свои позиции на рынке метрологического оборудования.
- Выбор ИП для установки на станок
Для измерения инструмента во фрезерном шпинделе выберем электроконтакный датчик наладки инструмента OTS ½ AAA исполнения фирмы Renishaw, который устанавливается в одну из позиций револьверной головки и имеющую технические характеристики:
- Точность ±1 мкм (2s (т е в 95% случаев))
- Повторяемость ±1 мкм (2s)
- Передача оптического сигнала (модулированного) инфракрасного диапазона
- Измерение в 3-х направлениях
На рисунке 47 показаны габаритные и установочные размеры датчика наладки инструмента Renishaw OTS ½ AAA.
Рисунок 47. Габаритные и установочные размеры датчика наладки инструмента Renishaw OTS ½ AAA
Для измерения инструмента во револьверной головке выберем датчик с кинематическим механизмом для наладки инструмента RP3 фирмы Renishaw, который устанавливается в оправку HSK, а затем во фрезерном шпинделе станка. Данный датчик имеет следующие технические характеристики:
- Точность ±1 мкм (2s)
- Повторяемость ±1 мкм (2s)
- Передача оптического сигнала (модулированного) инфракрасного диапазона
- Измерение в трех направлениях
На рисунке 48 показаны габаритные и установочные размеры датчика наладки инструмента Renishaw RP3.
Рисунок 48. Габаритные и установочные размеры датчика наладки инструмента Renishaw RP3
Для размерного контроля детали необходимо средство измерения с точностью на порядок выше измеряемой величины. Из этих соображений Выбрана щуповая головка с тензоэлементами модели OMP400 фирмы Renishaw.
- Повторяемость ±0,25 мкм (2s)
- Точность ±0,25 мкм (2s)
- Передача оптического сигнала инфракрасного диапазона в пределах 360° (модулированного или обычного)
На рисунке 49 показаны габаритные и установочные размеры датчика наладки инструмента Renishaw OMP400.
Файлы условия, демо
Характеристики курсовой работы
Список файлов
