Курсовая работа: Фасонный резец
Описание
ВАРИАНТ 130
СОДЕРЖАНИЕ
ВВЕДЕНИЕ…………………………………….………………………………..10
1 Проектирование фасонного резца …………………………………....13
1.1 Исходные данные и постановка задачи ……………………..……..13
1.2 Определение конструктивных и геометрических параметров фасонного резца …………………………………..……………………...……..13
1.3 Расчет глубины профиля и геометрических параметров резца ......18
1.4 Определение работоспособности резца………………………….….23
1.5 Расчет типовых участков профиля фасонных резцов………………………………………………………………………..……26
1.5 Расчет допусков на фасонные резцы …………………………….….28
1.6 Выбор материала инструмента ……………………………………...31
1.7Технические требования……………………………………............…31
ЗАКЛЮЧЕНИЕ……………………….………………….…………………...…40
СПИСОК ИСПОЛЬЗУЕМЫХ ИСТОЧНИКОВ………………...…………..…41
ВВЕДЕНИЕ
Основной целью курсового проектирования является формирование следующей компетенции ПК-4 способность участвовать в разработке проектов изделий машиностроения, средств технологического оснащения, автоматизации и диагностики машиностроительных производств, технологических процессов их изготовления и модернизации с учетом технологических, эксплуатационных, эстетических, экономических, управленческих параметров и использованием современных информационных технологий и вычислительной техники, а также выбирать эти средства и проводить диагностику объектов машиностроительных производств с применением необходимых методов и средств анализа. А так же подготовка студентов к выполнению выпускной квалификационной работы и самостоятельной инженерной деятельности. Этой цели подчинено содержание курсовой работы, как комплекса расчетно-графических задач.
В современном машиностроении обработка резанием является главным технологическим методом, обеспечивающим высокое качество обработки поверхностей деталей.
Режущий и вспомогательный инструмент, средства предварительной настройки инструмента вне станка и системы инструментального обеспечения играют важную роль в достижении высокой экономической эффективности дорогостоящего оборудования с ЧПУ.
Для выполнения этой роли необходимо применять инструмент, отличающийся следующими качествами: высокая надёжность при работе; быстросменность; высокий уровень унификации; переналаживаемость; относительно низкая стоимость.
Таким образом, генеральная линия развития машиностроения - компактная автоматизация проектирования и производства.
Резцы - наиболее распространённый вид режущего инструмента. Они отличаются большим многообразием. Применяются на токарных,
долбёжных, строгальных, расточных станках (соответственно этому резцы делятся на токарные, строгальные, расточные и долбёжные) и могут выполнять практически все виды обработки.
Резцы также различают по форме (призматические или дисковые) и по перемещению относительно обрабатываемой заготовки (радиальные и тангенциальные).
Резцы с радиальной подачей получили наибольшее применение за счёт простоты крепления и выбора геометрических параметров режущей части. Резцы с тангенциальной подачей применяют на токарных автоматах и полуавтоматах в тех случаях, когда основным требованием является шероховатость обрабатываемой поверхности. По направлению подачи резцы бывают правые и левые; по конструкции - цельные, составные, сварные, составные с механическим креплением пластин и т. д.; по материалу режущей части - из быстрорежущей стали, с пластинами из твёрдого сплава, минералокерамики и сверхтвёрдых синтетических материалов.
Фасонные резцы применяют для одновременной обработки нескольких поверхностей детали и фасонных профилей в крупносерийном и массовом производстве. Фасонные резцы обеспечивают высокую точность размеров и формы поверхности детали, высокую производительность и простоту заготовки. Они классифицируются:
а) по конструкции: призматические, круглые, стержневые;
б) по перемещению относительно оси детали: радиальные и тангенциальные;
в) по расположению основного отверстия или базы крепления по отношению к основной детали: с параллельным и наклонным расположением.
Дисковые фасонные резцы применяют для обработки наружных и внутренних поверхностей детали. Призматические - только для наружных поверхностей. Призматические резцы обладают, по сравнению с дисковыми, высокой точностью обработки конических и фасонных участков профиля детали. Для обработки отверстий применяются различные инструменты в зависимости от служебного назначения детали и технологического процесса её изготовления.
Наиболее распространенными осевыми инструментами являются сверла, зенкеры, зенковки, развёртки. Выбор осевого инструмента зависит от параметров отверстия: диаметра, глубины, точности, требований и расположения геометрической оси. Спиральное сверло относится к основным и наиболее распространенным видам режущего инструмента при обработки отверстий в сплошном материале. По конструкции спиральное сверло соответствует двойному назначению - быть режущим инструментом и шнеком, транспортирующим стружку из зоны резания. Основные размеры и углы стандартизованы.
1 Проектирование призматического фасонного резца
1.1 Исходные данные и постановка задачи
Исходные данные выбираем в соответствии варианта задания (Рис. 1, табл. 1):
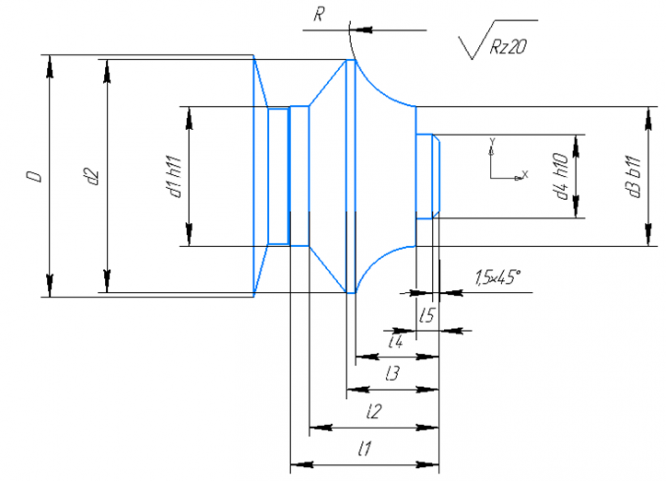
Рисунок 1 – Чертёж детали
Таблица 1 - Исходные данные на фасонный резец
№ варианта | Размеры в мм. | Материал | в кгс/мм2 | НВ | |||||||||
D | d1 | d2 | d3 | d4 | l1 | l2 | l3 | l4 | R | ||||
130 | 52 | 30 | 50 | 30 | 18 | 32 | 28 | 20 | 18 | 15 | Сталь 20 | 45 | 122 |
Примечания - предельные отклонения приведенных в таблице размеров указаны на соответствующих рисунках. Свободные размеры по 14 квалитету СТ СЭВ 144-75; 145-75.