Классификация интегральных микросхем
1. Классификация интегральных микросхем, подготовительные операции, базовые элементы БИС и СИС, особенности производства и применяемых расходных материалов
1.1. Классификация интегральных микросхем, особенности их производства
Укрупнённая классификация интегральных микросхем, БИС и СИС. Особенности технологии БИС при их масштабировании. Общемировой рынок продаж. Тенденции развития спроса. Изделия микроэлектроники, выпускаемые предприятиями электронной промышленности Республики Беларусь.
Все интегральные микросхемы (ИС) можно классифицировать по конструктивно-технологическим признакам, функциональному назначению, структуре базового элемента и др.
По характеру обработки электрического сигнала ИС делятся на два больших класса: логические (цифровые) и линейные (аналоговые). По конструктивно-технологическим признакам все ИС можно разделить на три группы:
1 - полупроводниковые и совмещенные ИС (ППИС);
2 - гибридные ИС (ГИС);
3 - пленочные и прочие ИС (к ним также относят вакуумные и керамические ИС).
Полупроводниковые ИС - это ИС, все элементы и межэлементные соединения которой выполнены в объеме и на поверхности полупроводникового кристалла.
Совмещенная ИС - это ИС, часть элементов которой выполнено на поверхности полупроводниковых кристалла в виде металлических пленок.
Рекомендуемые материалы
ГИС - это ИС, часть элементов которой (обычно пассивные) выполнены в виде пленок (1-2 мкм - тонкопленочная, 10-70 мкм - толстопленочная), а другая часть - в виде кристаллов полупроводниковых ИС или микроминиатюрных ЭРЭ, расположенных на диэлектрической подложке и электрически связанных между собой пленочными межэлементными соединениями.
Пленочная ИС - это схема, все элементы и межэлементные соединения которой выполнены в виде пленок на диэлектрической подложке (при этом элементы преимущественно изготовлены методами вакуумного нанесения).
Толстопленочная ИС - это схема с толщиной пленок 10-70 мкм, элементы которой изготавливаются методами трафаретной печати (сеткография).
Различия между тонко- и толстопленочными ИС может быть количественным и качественным. К тонкопленочным ИС относят ИС с толщиной пленок < 1 мкм, к толстопленочным ИС - ИС с толщиной пленок 10-70 мкм. Качественные различия определяются технологией изготовления пленок. Элементы ТП ИС формируют вакуумными методами, а элементы толстопленочных ИС получают преимущественно методом сеткографии с последующим вжиганием.
Все ИС разделяются по степени интеграции. Степень интеграции ИС - показатель степени сложности микросхемы, характеризуемый числом содержащихся в ней элементов и компонентов. Кроме степени интеграции (показатель К) используется термин плотности упаковки ИС, который определяет отношение числа элементов и компонентов ИС к ее объему (объем выводов не учитывается). Степень интеграции К определяется как :
,
где N - число элементов и компонентов, находящихся в кристалле и на поверхности ИС. Показатель К округляется до ближайшего целого числа.
ГОСТом предусмотрена классификация по показателю К (ГОСТ 17021-75):
1 степень: N <= 10 , 0 < К < 1 ;
2 степень: 10 < N < 100, К = 2 ;
3 степень: 100 < N < 1000, К = 3 и т. д.
В технической литературе используют также следующие термины: ИС (малой степени интеграции), СИС (средней степени интеграции), БИС (большие ИС), СБИС (сверхбольшие ИС) и УБИС (ультрабольшие ИС). Такое деление правомерно для цифровых ИС. Для них берется:
,
ИС - К = 1-5; СИС - К = 6-10; БИС - К = 11-16; СБИС - К = 16-21.
Подавляющее число логических ИС выпускаются в виде полупроводниковых, в то время как линейные ИС в основном изготавливаются по гибридной технологии.
Основные принципы технологии микроэлектроники - групповой метод и планарная технология - были известны еще до изготовления ИС. Эти методы были освоены в дискретной транзисторной технике в конце 50-х годов. При изготовлении транзисторов, например, осуществлялась их технологическая интеграция (по времени), обусловленная групповым методом изготовления. Групповой метод состоит в том, что на одной или чаще многих полупроводниковых пластинах одновременно формируют определенное число ЭРЭ (резистор, транзистор, диод). Сущность планарной технологии заключается в том, что одновременно формируемые элементы расположены или на поверхности подложки (ГИС) или в приповерхностном слое полупроводниковых пластины (plane плоскость).
Затем подложки или пластины разрезают (скрайбируют) на кристалл или платы. Каждый кристалл при этом будет содержать определенный ЭРЭ (R, D, T и т.д. – рисунок 1.1).
Если же на исходной пластине вместо отдельных ЭРЭ формируют такими же методами комплекс ЭРЭ функционального узла (R + D + T ), то после соответствующего разделения пластины на кристаллы получаются уже кристаллы ИС, выполняющих определенную функцию (рисунок 1.2).
Термин кристалл официально принят для готовых полупроводниковых приборов и ИС без внешних выводов и корпуса. Однако этот принцип несколько неудачен, т.к. он совпадает с общим физическим понятием кристалла. В зарубежной литературе используется специальный термин "чип" - (chip).
Таким образом, интегральной микросхемой (ИС) называют изделие, выполняющее определенную функцию преобразования и обработки сигнала, и имеющую высокую плотность упаковки электрически соединенных элементов (или элементов и компонентов) и кристаллов, рассматриваемое с точки зрения требований к испытаниям, приемке и эксплуатации как единое целое. ИС - содержит элементы и компоненты.
Элементом ИС называется часть схемы, реализующая функцию какого-либо электрорадиоэлемента (например, транзистора, диода, резистора). Эта часть выполняется неразделимо от кристалла или ее подложки. Элемент не может быть отделен от ИС как самостоятельное изделие, поэтому его нельзя испытать и эксплуатировать.
Компонентом ИС также называется её часть, реализующая функции какого-либо электрорадиоэлемента. Однако эта часть перед компонентом является самостоятельным изделием. Компонент в принципе может быть отделен от изготовленной ИС.
Подложка ИС - диэлектрическое основание для пленочных или гибридных ИС.
Плата ИМС - часть подложки пленочной или гибридной ИС.
Пластина - монокристаллическая полупроводниковая подложка, вырезанная из слитка полупроводникового материала и предназначенная для изготовления полупроводниковой ИС.
Кристалл ИМС - часть полупроводниковой пластины в объёме и на поверхности которого сформированы элементы единичной ИС.
Рисунок 1.1 – Групповой метод изготовления дискретных элементов (транзисторов) |
Рисунок 1.2 – Групповой метод изготовления ИС |
1.2. Технология изготовления кремниевых пластин для БИС и СИС
Кремний, как основной материал полупроводниковых БИС и СИС. Технологический маршрут получения пластин. Методы ориентации монокристаллов. Методы резки слитков на пластины. Абразивные материалы для механической обработки. Технологические особенности изготовления пластин для СБИС. Автоматизация обработки пластин. Технохимические методы удаления материалов с поверхности пластин.
Основным полупроводниковым материалом для электронной промышленности является Si, встречающийся в природе в виде кремнозема или силикатов. ИМЭ на основе Si составляет 98% всех производимых в мире полупроводниковых приборов. Кремний по степени распространения в природе находится на втором месте, уступая только кислороду. Он составляет 25% по весу всей земной коры. Доминирующее использование Si в полупроводниковой электронике связано не только с его широким распространением в природе, но и его свойствами. Так ширина запрещенной зоны Si составляет 1,12 эВ, а для Ge 0,66 эВ, что сказывается на стабильности характеристик приборов (для Ge приборов выше токи утечки). Рабочий диапазон Si приборов доходит до 150oС, а Ge - до 100oС.
Собственный Si имеет высокое удельное сопротивление ~230000 Ом×см, а Ge только 47 Ом×см, что затрудняет изготовление на основе Ge приборов с высокими пробивными напряжениями. Кроме того стоимость кремния высокого уровня чистоты в 10 раз ниже стоимости Ge. Однако же основные достоинства Si по сравнению с Ge и GaAs связаны с его высокой технологичностью: на Si легко получать защитные окисные пленки (окислы Ge растворяются в воде, а на GaAs очень сложно вырастить окисные пленки, т.к. элементы Ge и As окисляются с различной скоростью); Si легко легировать и т.д.
Основной объем монокристаллического Si (80 - 90%), потребляемого электронной промышленностью, выращивается по методу Чохральского. Фактически весь Si, используемый для производства ИС, производится этим методом. Сырьем для получения монокристаллического Si является электронный Si, представляющий собой поликристаллический материал высокого уровня чистоты. Основные примеси в электронном Si это В, С2 и О2. Концентрация легирующих элементов в чистом Si не должна превышать 10-7 ат.%, а углерода - 2×10-4 ат.%. Методом Чохральского получают монокристаллы диаметром до 250 мм и длиной до 3 м. Монокристаллы, полученные данным методом, содержат примеси и дефекты.
Кислород - случайная примесь в Si, образующаяся в результате растворения материала тигля (Si3N4, SiO2 и др.). Диапазон концентраций О2 в слитке 5.1017 - 1018 см-3. Наличие О2 в слитке приводит к формированию доноров и образованию дефектов за счет собственной преципитации О2. Наличие доноров изменяет удельное сопротивление кристаллов за счет легирования.
Донорные комплексы нестабильны при Т > 500оС, поэтому для их растворения используется отжиг слитков при температурах 600 - 700оС.
Преципитат представляет собой фазу SiO2. С формированием преципитатов связано образование в слитке ряда дефектов, включая дефекты упаковки. Эти дефекты захватывают примеси быстро диффундирующих металлов, приводя к увеличению токов утечки р-n-переходов. Способность дефектов захватывать нежелательные примеси (эффект геттерирования) может быть использован для улучшения свойств подложек (электрофизических).
Углерод – другой вид случайной примеси. Он является в Si примесью замещения. Его концентрация 1016 - 5.1017 см-3 . При таких концентрациях он не выделяется в преципитаты, подобно О2, и не становится электрически активным. Однако С оказывает влияние на преципитацию О2 и способствует дефектообразованию.
Конструктивным фундаментом любой ИС является подложка. В зависимости от конструктивно-технологического варианта ИС (п/п, ГИС) различают два вида подложек: активные (полупроводниковые: Si, Ge, GaAs, GaP) и пассивные (диэлектрические: стекло, ситалл). Полупроводниковые подложки называются пластинами.
Технологический процесс получения Si-пластин включает в себя ряд укрупненных процессов (операций):
1. Выращивание монокристалла.
2. Получение заданного диаметра монокристалла обдиркой.
3. Получение ориентированного базового среза.
4. Снятие механических напряжений травлением монокристалла.
5. Кристаллографическая резка кристалла на пластины.
6. Получение пластин заданной толщины односторонней или двусторонней шлифовкой, формирование плоскопараллельной поверхности и уменьшение дефектного слоя.
7. Получение округленных кромок пластин (фаска).
8. Удаление нарушений поверхности пластин травлением.
9. Создание геттеродефектов упаковки путем формирования нарушенного слоя с обратной стороны пластины.
10. Получение поверхности пластин 14 класса чистоты полировкой.
11. Очистка поверхности пластин от загрязнений "мокрыми" и "сухими" процессами.
12. Контроль геометрических, электрических, кристаллографических параметров и качества поверхности.
В интервале между основными операциями механической обработки осуществляется ряд операций контроля и оценки качества обработки. Готовая подложка должна удовлетворять целому ряду требований к геометрическим размерам, которые определяются условиями технологии производства полупроводниковых приборов.
Монокристаллы выращенные методом Чохральского или зонной плавки, имеют стандартную ориентацию [111] и [100] с отклонением до 2' и по спецзаказам - [110] и [011] . На монокристалле определяют плоскость базового и дополнительного срезов. Базовый и дополнительный срезы получают методом шлифовки монокристаллического слитка вдоль образующей. Самый большой базовый срез называют основным. Его обычно располагают определенным образом относительно некоторого кристаллографического направления. Основной базовый срез служит для :
1) ориентации пластины одинаковым образом в технологических установках с автоматизированным ориентированием;
2) ориентации ИС относительно кристаллографических направлений строго определенным образом.
Малые базовые срезы называются дополнительными и предназначены для распознавания ориентации и типа проводимости подложек.
Они обеспечивают быструю сортировку и идентификацию пластин при их случайном перемешивании.
При получении базовых срезов и при дальнейшей механической обработке слитка (резке и т.д.) учитывают его ориентацию.
Для большинства изделий микроэлектроники точность ориентации пластины относительно требуемого кристаллографического направления имеет определяющее значение для всех последующих технологических операций. Монокристаллы ряда полупроводников выращивают обычно по направлению [111]. Однако в процессе роста кристаллов возможны отклонения их ориентации от заданного направления так, что геометрическая ось цилиндрического слитка окажется отличающейся от кристаллографической оси [111]. Цель операции ориентации - нахождение несоответствия между геометрической осью слитка и заданным кристаллографическим направлением.
Существует два основных способа определения заданного кристаллографического направления:
1. Рентгенографический способ. Основан на том, что интенсивность рассеивания рентгеновских лучей зависит от плотности упаковки атомов в облучаемой плоскости. Для наиболее плотно упакованной плоскости [111] наблюдается и наибольшая интенсивность рассеивания. В тоже время для каждого вещества характеристическое рентгеновское излучение отражается от соответствующей кристаллографической плоскости под строго определенным углом (таблица 1.1).
Таблица 1.1 – Углы отражения от различных плоскостей для Ge и Si
Материал | Углы рассеивания для плоскостей | ||
[111] | [110] | [100] | |
Ge | 17о 14' | 28о 56' | 43о 10' |
Si | 17о 56' | 30о 12' | 45о 23' |
Явление дифракции рентгеновских лучей наблюдается при условии выполнении закона Вульфа-Брэгга
, (1.1)
d - межплоскостное расстояние;
Q - угол между падающим лучом и кристаллографической плоскостью;
n - период отражения (n = 1);
L - длина волны рентгеновского излучения.
Этот способ обеспечивает точность 3-5о при времени 15 - 30 мин.
2. Оптический метод. Основан на различии формы и характера симметрии фигур травления, образующихся в местах выхода на поверхность дислокаций. Эти фигуры появляются при обработке поверхности селективными травлениями. На плоскости [111] ямки травления имеют вид тетрагональных пирамид с треугольным основанием; на [110] - вид пирамид с ромбическим основанием и т.д. Отражаясь от граней ямок травления, световой пучок воспроизводит на экране соответствующие характерные теневые фигуры. При отклонении от заданного кристаллографического направления симметрия теневых фигур нарушается. Фигуры смещаются на некоторый угол и их очертания искажаются. Точность ориентации составляет 3 - 15'.
При резке Si-слитков на пластины в качестве режущего инструмента применяют металлические диски с внутренней алмазной режущей кромкой (рисунок 1.3). Инструмент представляет собой диск (металлический) с центральным отверстием, на кромку которого нанесена алмазная крошка. Толщина диска 0.1 - 0.15 мм, а диаметр отверстия зависит от диаметра разрезаемого слитка. Принцип резания заключается в следующем: режущий диск растягивается и закрепляется в специальном барабане на головке шпинделя. Слиток разрезается кромкой с алмазной крошкой при вращении шпинделя (Vвр = 3000 - 5000 об/мин). Скорость движения слитка ~40-50 мм/мин. После отрезания очередной пластины с помощью системы автоматики происходит возврат слитка в исходное положение, а также перемещения его на заданный шаг.
Аналогично происходит резанье слитка с использованием дисков с наружной режущей кромкой (рисунок 1.4).
Насыщение кромки алмазом производят методом шаржирования (горячая запрессовка в металл) или гальваническим способом. Ширина алмазной кромки ~1,5 – 2,0 мм.
Недостаток метода - большая толщина механически нарушенного слоя, сложность установки инструмента и наладки оборудования.
Кроме этих методов используют
1. Резанье слитков стальными полотнами с абразивной суспензией.
В настоящее время используется редко. Суть метода: стальные полотна из сталей марок У8А, У10А устанавливают в кассетах в количестве до 100 шт. в каждой и разделяют прокладками, толщина которых определяется толщиной пластины. В зону резания непрерывно подается абразивная суспензия. Скорость движения кассеты 600 двойных ходов в минуту. Скорость резания ниже, чем алмазосодержащими дисками 10-15 мм/ч. Преимущество метода - малая ширина реза (~2 ширины полотна) и меньшая толщина механически нарушенного слоя (рисунок 1.5).
2. Резанье слитков проволокой - метод аналогичен. Различие состоит только в геометрии носителя образива. Проволоку изготавливают из W или сплава МВ-50 (50% W + 50% Ме), диаметр проволоки 0,1-0,15 мм. Преимущество метода - еще меньший размер реза.
Недостаток - невозможность резания на большую глубину из-за увода проволоки и нарушения геометрии пластин (рисунок 1.6).
Абразивные материалы отличаются между собой размером (крупностью зерен), имеют номера 200, 160, 125, 100, ..., 3, М40, М7, М5, М3 и делятся на 4 группы :
1. Шлифзерно - 200-16;
2. Шлифпорошки - 12-3;
3. Микропорошки - М63-М14;
4. Тонкие микропорошки - М10-М3 (3 мкм).
К основным абразивным материалам относятся :
1. Электрокорунд - кристаллическая окись Al - Al2O3, получаемая в результате плавки глинозема. Твердость по шкале Мооса равна 9.
2. Карбид кремния (SiC)- химическое соединение Si с С , получаемое нагреванием смеси кварцевого песка с коксом в электропечах при Т>2000о С. Твердость по шкале Мооса равна 9.2. Это хороший абразивный материал с высокими режущими свойствами. Чем меньше размеры его зерен, тем больше их плотность.
3. Карбид бора (ВС) - тугоплавкое соединение В с С. По твердости карбид бора превосходит все абразивные материалы, уступая лишь алмазу. Однако по сравнению с другими абразивными материалами он хрупок.
![]() | ![]() |
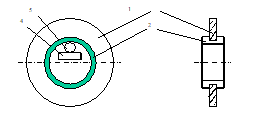
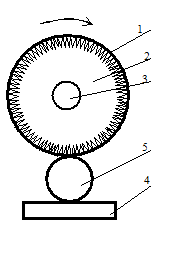
![]() | ![]() |
[VVB1]
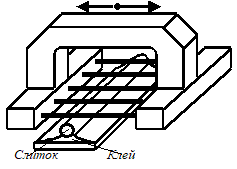
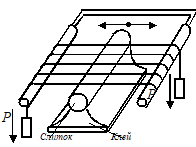
Шлифование - это обработка пластин на твердых шлифовальных дисках, выполненных из чугуна, стекла или латуни, абразивными порошками с размером зерна 28-3 мкм или алмазными шлифовальными кругами зернистостью 120-5 мкм. Шлифование позволяет получить 9-12 класс чистоты.
Шлифование полупроводниковых пластин классифицируют:
- по состоянию используемого абразива - свободным и связанным абразивом;
- по характеру обработки - односторонние и двусторонние;
- по качеству обработанной поверхности - предварительное и окончательное;
- по способу базирования пластин - с креплением пластины на оправку (наклейка, вакуумный режим) и со свободным положением пластин в кассетах и сепараторах.
Наиболее распространенным видом шлифования является одностороннее шлифование свободным абразивом с наклейкой пластин на оправу. При шлифовании формируется нарушенный слой.
Шлифование можно вести сухим абразивом, но, как правило, используют абразивные суспензии, роль жидкости (чаще всего воды) в которых сводится к распределению зерен по поверхности шлифовальника и удалению разрушенных частиц полупроводника. При обработке связанным абразивом зерна закреплены в материале шлифовального круга.
Полирование пластин производят на мягких подложках из фетра велюра, батиста, пропитанных абразивными пастами на жировой основе с крупностью зерна 3-0.25 мкм. Класс чистоты при этом 14 и выше.
При полировании полупроводниковых пластин используют алмазные порошки и пасты. Пасты на основе кубического нитрида бора (эльбора), оксида алюминия, оксидов церия, хрома, кремния.
После шлифовки и полировки пластин возможно возникновение различных дефектов.
Основные виды дефектов формы пластин показаны на рис. 10.
Отклонение от параллельности (непараллельность) плоскостей (а) h; отклонение от плоскости (неплоскостность) (б) и (в); прогиб пластины - f (г).
Контроль дефектов формы пластин проводят на промежуточных операциях и после окончательной обработки. Во избежание повреждений поверхности контроль производят бесконтактными оптическими или фотоэлектрическими методами. Толщина механически нарушенного слоя определяется рентгенографическим или электронографическим способом.
Поверхности 8 - 14 класса чистоты контролируют с помощью профилографов - профилометров, принцип действий которых основан на контактном слежении алмазной иглой за профилем поверхности с последующим преобразованием ее перемещений в электрические сигналы.
Поверхности 13 - 14 класса чистоты контролируют интерференционным способом с помощью микроскопов Линника, например МИИ-4.
После финишной обработки поверхность должна иметь не хуже 14, неплоскостность не выше 4 мкм/см, отклонение от номинала по толщине
±10 и по диаметру ±5мм.
В настоящее время используются подложки из Si, GaAs и сапфира, но доминирует Si.
Монокристаллы Si получают методом Чохральского (до 300 мм в диаметре) и методом зонной плавки (~120 мм). Стандартная ориентация [111] и [100] с отклонением до 2'.
Основные этапы изготовление пластин:
1. Калибровка монокристалла Si заключается в его шлифовке для формирования цилиндрической поверхности заданного диаметра с допусками ±0.2-0.5 мм и создание плоских срезов - базового и дополнительного. Базовый срез необходим для идентификации ориентации подложек; дополнительный срез меньшей ширины - типа проводимости.
2. Резка на пластины осуществляется ленточными или дисковыми пилами, свободным или связанным абразивом.
3. Формирование фаски. Фаска формируется на периферийной части пластины после резки или шлифовки. В поперечном сечении фаска имеет форму овала. Фаску формируют шлифовкой, полировкой или травлением. Для формирования фаски используют только автоматизированные системы.
Наличие фаски предотвращает образование линии скольжения, царапание фотошаблонов, износ автоматизированного оборудования, трудности установки пластин в кварцевые и другие лодочки, скопление фоторезисторов по краю подложки, скол края и износ алмазного инструмента при скрайбировании. Существенное увеличение прочности края пластин с фаской демонстрирует такой пример: после тысячи операций загрузки и выгрузки в кварцевую лодочку 95% пластин с фаской не имеют сколов, в то время как пластины без фаски практически все непригодны.
4. Шлифовка и полировка. Шлифуются пластины свободным либо связанным абразивом, полируются же только свободным абразивом, чаще суспензией.
Обычно выход годных от резки монокристаллов до полировки пластин ~90 %. Остальные пластины забраковываются или обрабатываются повторно.
5. Травление пластин обычно осуществляется между операциями резки, шлифовки и полировки. Наибольшую производительность этой операции обеспечивают групповая технология в кассетах или специальных корзинах.
6. Полировка обычно имеет две стадии - предварительную и финишную. Предварительная полировка удаляет нарушенный слой до глубины ~25 мкм в течении менее 20 мин. Финишные - снимают малое количество материала до полного удаления нарушенного слоя.
7. Введение геттера в подложку осуществляется для устранения
быстро диффундирующих примесей и кластеров точечных дефектов из приповерхностной рабочей зоны подложки. Геттер может быть расположен с рабочей, нерабочей стороны подложки и внутри ее. Соответственно он называется внешним и внутренним. Последнее время отдается введению внешнего геттера путем внесения нарушений шлифования, лазерным лучом, а также внутреннему оксидному геттеру.
8. Очистка поверхности пластин. Это обычно очистки кистями, промывка, центробежная сушка и обдувка азотом.
9. Упаковка и хранение пластин. Для предохранения пластин от влияния внешней среды используется герметичная упаковка типа "FLIP-TRAN". Кассету герметично упаковывают в металлическую банку, заполненную чистым азотом при повышенном давлении. Если пластины сразу же идут в дальнейшую работу, то их не герметизируют.
В настоящее время существует 4 уровня автоматизации технологического процесса изготовления и обработки пластин:
- перенос пластин;
- обработка (оператор загружает кассеты и устанавливает параметр ТП);
- контроль и выбор режимов операций (оператор загружает кассеты, управляет работой, включая выбор режима работы ЭВМ);
- полный цикл, включая перенос кассет и отдельных пластин, а также выбор режима и последовательности операций.
Важной частью автоматизации является исключение операции ручного манипулирования, т.к. масса пластин велика (25 пластин Si диаметром 150 мм в кассете весят ~2 кг). При ручном манипулировании точность установки пластин в лодочку или другую оснастку снижается, при этом на оснастке или пластине появляются сколы. Исключение этого повышает выход годных на 2%.
В ряде фирм реализуется два варианта автоматизации и транспортировки пластин и подложек от одного рабочего места к другому:
1. Транспортер с дорожками, по которому перемещаются пластины (в кассетах или без них) в потоке фильтруемого воздуха.
2. Использование робота для подъема передачи и опускания пластин на рабочих участках.
Последняя схема наиболее предпочтительна, т.к. позволяет разместить оборудование в нужном месте. Обе системы используют ЭВМ для контроля и записи перемещения пластин.
Основными целями технохимических процессов являются:
- получение чистой поверхности пластин (подложек);
- удаление с поверхности подложек механически нарушенного слоя;
- снятия с полупроводниковой пластины слоя исходного материала определенной толщины;
- локальное удаление исходного материала с поверхности подложек;
- создание определенных электрофизических свойств подложки;
- выявление структурных дефектов кристаллической решетки подложки;
- получение мезаструктур и профилированных поверхностей;
- осаждение гальванических покрытий.
Чистая поверхность необходима для качественного проведения процессов диффузии, эпитаксии, окисления и др. Поэтому основной целью технохимических процессов является удаление с поверхности исходных подложек различного рода загрязнений. Получение технологически чистой. поверхности достаточно сложный процесс, который достигается проведением комплекса различных процессов: промывка в Н2О, УЗК-промывка в растворителях и т.д. Технологически чистой считается поверхность, которая имеет концентрацию примесей, не препятствующих воспроизводимому получению требуемых значений и стабильности параметров ИС. Для нежестких требований к ИС эта величина концентрации составляет 105-80 - 105-70 г/см2.
Удаление нарушенного слоя, образовавшегося в результате шлифовки и полировки, необходимо для получения атомарно-совершенной структуры поверхностного слоя. Именно в этом слое затем формируются активные элементы ИС и других изделий. Удаление механически нарушенного слоя можно осуществить химическим и газовым травлением, а также ионно-плазменной и плазмохимической обработкой.
Удаление с поверхности пластин слоя определенной толщины проводят для получения нужных толщин подложек. Требуемая толщина подложек определяется конкретным типом ИМЭ. Наиболее часто для цели удаления используют химическое травление полупроводниковых материалов в различных травителях.
Локальное удаление полупроводниковых материалов проводят для создания рельефа, который дает возможность решать конкретные вопросы конструирования и технологии. Локальное удаление обычно осуществляют электрохимической обработкой в электролите либо химическим травлением через защитную маску.
Технохимические процессы дают возможность регулировать и изменять электрофизические свойства поверхности полупроводниковой подложки такие как: поверхностную проводимость и скорость поверхностной рекомбинации. Наиболее эффективны при этом процессы химического травления, плазменной и плазмохимической обработки.
Технохимические процессы позволяют выявлять структурные дефекты полупроводниковых материалов на различных этапах обработки. К таким дефектам относятся: дислокации, дефекты упаковки, двойники и др. Их выявление проводят селективным химическим или ионным травлением.
Получение мезаструктур ("меза" - mesa - плато) - широко распространенный технологический прием при получении большого класса дискретных полупроводниковых приборов. Это касается mesa приборов с повышенным быстродействием т.к. площадь p-n-перехода, а значит и Cp-n снижается. Форма и геометрические размеры мезаструктур определяются локальной маской, а глубина типом, составом и режимом процесса травления.
Осаждение гальванических покрытий из металлов и сплавов позволяет создавать на поверхности полупроводниковой пластины токопроводящие дорожки, невыпрямленные контакты и пассивные элементы.
1.3. Базовые элементы биполярных БИС и СИС
Положение БИС и СИС в общей классификации изделий электронной техники. Структура базовых элементов биполярных БИС и СИС. Структура базовых элементов униполярных БИС и СИС. Базовые элементы с инжекционным питанием. Интегрированные приборы с зарядовой связью. Особенности применения биполярных БИС и СИС.
По структуре базового элемента различают биполярные и униполярные ИС. В основе биполярных ИС лежат n-р-п и р-n-р транзисторы (рисунок 1.7).
Одним из перспективных направлений развития цифровых БИС являются схемы с инжекционным питанием. В этих схемах энергия, необходимая для преобразования или хранения информации, вводится инжекцией неравновесных носителей в базу через специальный инжекторный переход, смещаемый в прямом направлении. Простейшая конструкция транзистора с инжекционным питанием показана на рисунке 1.8. В отличие от обычного п-р-п транзистора данная структура содержит еще один электрод-инжектор (Р1-облость). Второе отличие заключается в изменении функций электронных областей N1 и N2: N1-эмиттер, N2-коллектор.
В этой структуре образуется практически два транзистора:
1. Транзистор р-n-р-типа образован инжекторной областью Р1, играющей роль эмиттера, частью эмиттерной N1-области, служащей базой, и базовой Р2-областью, выполняющей функции коллектора.
2. Транзистор n-р-n вертикального типа образован частью эмиттерной N1-области, примыкающей к ней, частью базовой Р2-области и коллекторной N2-областью.
Если на инжекторный переход подано напряжение от внешнего источника питания Е, смещающее его в прямом направлении, то инжектированные в эмиттер (N1-область) дырки диффундируют к эмиттерному переходу, захватываются полем перехода и комплексируют часть объемного заряда перехода N2-Р2 со стороны базы. Вследствие этого эмиттерный переход сужается, потенциальный барьер снижается, т.е. переход смещается в прямом направлении. В результате начинается инжекция электронов из Э в Б и их дрейф к К, где они комплексируют часть объемного заряда коллекторного перехода, снижая тем самым его потенциальный барьер. К-переход смещается в прямом направлении, а транзистор переходит в режим насыщения, т.е. имеет малое R. Если соединить базу с эмиттером переключателем S, то напряжение между Б и Э будет равно "0", через транзистор потечет ток близкий к току инжекции и транзистор перейдет в активный режим, близкий к режиму отсечки. Сопротивление его при этом велико. Транзистор работает в режиме ключа.
Инжекционные схемы подразделяются по количеству используемых при их создании процессов (начинающихся на букву "И") на следующие :
ИЛ - интегральная логика; И2Л - интегральная инжекционная логика; И3Л - интегральная логика с изопланарной изоляцией; И4Л - интегральная ионно-имплантированная логика (без изоляции) И5Л - интегральная ионно-имплантированная логика с изопланарной изоляцией.
В полупроводниковых ИС, кроме биполярных и МОП-транзисторов, базовыми элементами являются приборы с зарядовой связью (ПЗС). Технология создания ПЗС аналогична технологии МОП-структур (рисунок 1.9). На поверхности полупроводниковой подложки находятся близко расположенные металлические затворы (З1, З2, З3, З4 и т.д.). Для инжекции зарядов на входе структуры выполняется диффузионный диод. Если по всем затворам приложить пороговое отрицательное смещение U1, то у поверхности полупроводника n-типа образуется равномерный обедненный электронами слой. Увеличение смещения до U2 > U1 на затворе З1 приведет к появлению в приповерхностной под ним зоне потенциальной ямы, в которую при наличии напряжения на входном диоде будут инжектироваться дырки. Если после окончания процесса инжекции к затвору З2 приложить U3 > U2, то под ним возникает более глубокая потенциальная яма. При этом под затворами З1 и З2 возникает продольное поле, под действием которого в приповерхностном слое полупроводника произойдет дрейф носителей заряда от З1 к З2. Аналогично происходит перемещение зарядов к следующим электродам.
Рисунок 1.7 – Базовые элементы биполярных ИС |
Рисунок 1.8 – Транзистор с инжекционным питанием |
Рисунок 1.9 – Структура прибора с зарядовой связью |
1.4. Базовые элементы МОП БИС
Основные МОП транзисторные структуры в составе БИС и СИС. Особенности работы МОП транзисторных структур в составе БИС и СИС. МОП транзисторные структуры с затвором из поликристаллического кремния и тугоплавкого металла. D-МОП, V-МОП структуры и МОП транзисторы на диэлектрической подложке. Структуры КМОП БИС. Особенности применения МОП БИС.
Принцип действия МОП-транзистора основан на управлении током, протекающим в приповерхностном слое полупроводника, при помощи напряжения, приложенного к металлическому электроду, отделенному от поверхности полупроводника тонким диэлектриком. Различают n-МОП, р-МОП, КМОП ИС, где в качестве базового активного элемента используются р-канальные, n-канальные МОП-транзисторы, либо комплементарная пара на их основе (рисунок 1.10).
Рисунок 1.10 – Базовые элементы униполярных ИС |
![Описание: ris6.wmf]()
1.5 Требования к производству БИС и СИС. Технологический микроклимат
Общие требования к производству изделий микроэлектроники. Технологический микроклимат и его основные характеристики. Определение и классификация "чистых" технологических помещений (ЧТП): "чистые" технологические помещения, комнаты, коридоры, и модули. Принципы проектирования ЧТП. Особенности водо-, газо- и энергоснабжения ЧТП. Системы кондиционирования и поддержания микроклимата в ЧТП. Вакуумная гигиена. Спецодежда персонала ЧТП. Приёмы работы обслуживающего персонала и операторов в ЧТП. Базовые среды – технологические газы и технологическая вода, их основные характеристики.
Источники и виды загрязнений пластин и подложек - абразивные и клеящие материалы; пыль (находящаяся в помещении), оборудование, инструмент, оснастка, тара для транспортировки и хранения; технологические среды; органические и неорганические реагенты; вода и др.
Т.к. загрязнение подложек возможно практически на всех операциях, то процесс очистки поверхности осуществляется многократно.
Виды загрязнений разделяются по их физико-химическим свойствам, т.к. последние определяют выбор методов удаления загрязнений:
а) органические загрязнения - это в основном жировые неполярные загрязнения клеящими веществами, маслом от станков, от рук операторов;
б) растворимые в воде полярные загрязнения - соли, кислоты, остатки травителей, флюсы;
в) физические загрязнения - пылинки, ворсинки, абразивная пыль и другие посторонние частицы, химически не связанные с поверхностью пластин (подложек);
г) загрязнения, химически связанные с поверхностью - оксидные, нитридные, карбидные и др. соединения;
д) газы, адсорбированные поверхностью.
На поверхности пластин (подложек) ИС могут присутствовать одновременно многие виды загрязнений. Наиболее трудноудалимыми являются органические и некоторые химически связанные с поверхностью загрязнения. Из физических загрязнений наиболее трудно удаляются мелкие зерна абразива, внедренные в поверхность. Из растворимых в воде полярных загрязнений трудно удаляются подвижные ионы металлов (Na, K и т.д.).
С точки зрения механизма процессов все методы очистки можно условно разделить на химические и физические, при этом используются различные технологические среды. Под последними понимают различные жидкостные и газовые реагенты, оказывающие влияние на поверхность подложек, окружающую среду (Ar, N2, О2 и т.д.), в которой осуществляются те или иные технологические процессы (очистка, окисление, диффузия и т.д.).
Классификация приведена на рисунке 1.11.
![]() |
Рисунок 1.11 – Классификация методов очистки поверхности пластин |
В органических растворителях (четыреххлористом углероде CCl4 , бензоле, толуоле и др.) эффективно растворяются почти все жировые загрязнения. При погружении образцов в растворитель от поверхности отрываются молекулы жира. Их отделение вызвано их собственными колебательными движениями и притяжением со стороны молекул растворителя. Растворимость жиров увеличивается с ростом температуры, поэтому обезжиривание ведут в горячих или кипящих растворителях. Однако применение органических растворителей не желательно, т.к. молекулы жиров уходят в раствор без химического разрушения и могут снова попасть на поверхность пластин.
Химическое обезжиривание .выполняется в составах, разрушающих молекулы жиров.
В производстве ИЭОТ иногда применяют обработку поверхности в мыльных растворах, которая служит для перевода омыляемых жиров в мыла, представляющие собой растворимые в воде соли. Последние удаляются с поверхности промывкой. К омыляемым жирам относятся все растительные и животные жиры, которые представляют собой сложные эфиры глицерина и высокомолекулярных органических кислот (стеариновой, олеиновой и др.).
В настоящее время для химического обезжиривания Si применяется горячий 75-80° C "универсальный" перекисно-амиачный раствор, .состоящий из водного раствора смеси перегидроли Н2О2 и щелочи NH4OH.
В технологии БИС и СИС иногда особенно важно получить атомарно чистую поверхность перед проведением ряда технологических процессов, таких как эпитаксия, окисление и др. Для этого используют процесс газового травления кремния, при этом помимо удаления загрязнений с поверхности происходит стравливание слоя Si с механическими нарушениями. Газовое травление применяется в тех технологических процессах, в которых особую роль играет структура поверхностного слоя, например, при эпитаксиальном наращивании или при получении подзатворного окисла в МДП-структурах.
В качестве травителей используют смеси водорода (Н2) или гелия (Не) с галогенами (F, Cl, Br), галогеноводородами (НВr, HCl), сероводородом (Н2S), гексафторидом серы (SF6). Молярное содержание этих веществ в Н2 или Не может изменяться от десятых долей до единиц процентов. Обработка производится при Т = 800 - 1300°С либо в установках для окисления, либо в реакторах для эпитаксиального наращивания. При травлении Si в НСl происходит следующая реакция:
(1.2)
Аналогично и для НВr. При травлении в сероводороде идут следующие реакции:
(1.3)
(1.4)
Продуктами реакции при газовом травлении являются только газообразные вещества, чем и обусловлена высокая эффективность очистки поверхности.
Химическое травление в жидкостях происходит на границе твердой и жидких сред и может рассматриваться как гетерогенная реакция. Процесс травления состоит из 5 стадий:
1. Диффузия реагента к поверхности;
2. Адсорбция реагента;
3. Химическая реакция;
4. Десорбция продуктов реакции;
5. Диффузия продуктов реакции от поверхности.
Скорость всего процесса определяется скоростью наиболее
медленной (контролирующей) стадии. При травлении Si такими стадиями могут быть либо диффузия реагентов к поверхности, либо химическая реакция. Скорость диффузии реагента в соответствии с законом Фика:
, (1.5)
где Nоб, Nпов - концентрация реагента соответственно в объеме и на поверхности;
s - толщина приповерхностного слоя травителя, в котором существует градиент концентрации.
Скорость химической реакции
, (1.6)
где NA, NB - концентрации реагирующих веществ;
DW - энергия активации химической реакции;
R - универсальная газовая постоянная.
Показатели "а" и "b" для простых реакций численно равны коэффициентам в уравнении химической реакции.
Энергия активации - это избыточная энергия, которой должна обладать молекула в момент столкновения, чтобы быть способной к химическому взаимодействию.
Энергия активации, определяющая скорость диффузии в жидкостях DWg = 1-4 Ккал/моль. Энергия активации химических реакций для различных травителей 10-500 ккал/моль. В зависимости от соотношения DW и DWg контролирующей стадией является:
1. DW < DWg - химическая реакция;
2. DW > DWg - диффузия.
В первом случае скорость травления чувствительна к состоянию поверхности. Так шлифованная поверхность имеет меньшее значение DW, чем полированная. Величину DW снижают дислокации и другие дефекты кристалла. Поскольку различные кристаллографические плоскости имеют различные значения DW, то скорость травления зависит от ориентации пластины и температуры. Травители, для которых контролирующей стадией является химическая реакция называются селективными.
Во втором случае скорость травления нечувствительна к неоднородностям поверхности, слабо зависит от температуры и резко от факторов, влияющих на скорость диффузии (вязкость травителя, перемешивание травителя и др.). Травители, для которых контролирующей стадией является диффузия, называются полирующими.
Травление в полирующих травителях. Для Si типичными полирующими травителями являются смеси HNO3 и HF (платиновая). Травление происходит в соответствии с электрохимической теорией растворения Si. Согласно ей, вся поверхность пластины, покрытая раствором травителя, состоит из большого числа микроэлектродов-катодов и анодов. На анодных участках происходит окисление Si с последующими растворением окисла и образованием кремнийфтористоводородной кислоты. На катодных - восстановление азотной кислоты. Результирующее уравнение имеет вид:
(1.7)
Скорость травления Si в этом случае определяется диффузией реагентов к поверхности Si. При этом происходит сглаживание поверхностного рельефа.
Выступы на поверхности травятся быстрее впадин, вследствие более высокого градиента концентрации.
Травление в селективных травителях. Селективными травителями для Si являются водные растворы щелочей и гидразин гидрат (NH2)2 ×H2О. Химические реакции для этих травителей имеют высокие W: 13 ккал/моль для 10% раствора NaOH и 6-10 ккал/моль для (NH2)2H2O. Для селективных травителей характерна большая разница в скоростях травления различных кристаллографических плоскостей. Так в этих травителях плоскости (100) травятся в 20 раз быстрее плоскостей (111). Поэтому травление в таких травителях иногда называют анизотропным.
V-образные области получаются при локальном травлении пластин Si, ориентированных в плоскости (100). Маской служит пленка SiO2 .
Границы окон в пленке SiО2 следует располагать по направлению пересечения плоскостей (111) с поверхностью, т.е. по направлению [110]. Каждую плоскость (100) пересекает ряд плоскостей (111). Анизотропный травитель растворяет плоскость (100) до тех пор, пока не выявятся плоскости (111), начинающиеся у краев окна в пленке SiO2 . Точность углов между плоскостями (в данном случае 35,3°) позволяет получить углубление строго определенной формы.
Такие V-образные канавки применяются в технологии ИС для получения изолирующих областей и разделения пластин ИС с балочными выводами на кристаллы.
После всех технологических обработок пластины и подложки подвергаются обязательной промывке.
В процессе изготовления БИС и СИС промывка поверхности проводится неоднократно. Для этого используется особо чистая де ионизованная вода. Тщательная отмывка Si или диэлектрических подложек необходима после обезжиривания их в мыльных растворах или перекисно-амиачном растворителе.
Промывка Si после травления выполняется вытеснительным методом. При вытеснительной промывке травитель не выливается до конца, чтобы пластины не соприкасались с воздухом; в ванну поступает деионизованная вода, разбавляя остатки травителя и постепенно вытесняя его. Если же слить травитель полностью или извлечь пластины, в местах оставшихся капель травителя продолжаются химические реакции. В результате поверхность пластин не будет однородно гладкой.
1.6. Общие требования к расходным материалам
Основные разновидности жидких химических реактивов, используемых в производстве изделий полупроводниковой электроники. Требования к качеству химических реактивов. Описание процессов адсорбции с помощью уравнения Генри, включая область малых концентраций примесей. Особенности адсорбции примесей на поверхности полупроводника. Механизмы воздействия процессов адсорбции на качество ИМС. Классы чистоты жидких химических реактивов по стандартам ASTM и ГОСТ.
Хранение, расфасовка и транспортировка химических реактивов. Ёмкости для хранения и транспортировки. Повышение требований к чистоте в соответствии со спецификацией SEMI. Устройства подачи химических реактивов на рабочие места. Требования к насосам.
Протекание процессов адсорбции примесей на поверхности подложек БИС и СИС описывается уравнением Генри:
Г = Zc b C (1.8)
где Г – величина адсорбции;
Zc – адсорбционная ёмкость монослоя;
b - константа адсорбционного равновесия;
С – концентрация примеси.
14 Технология технического обслуживания и текущего ремонта автомобилей - лекция, которая пользуется популярностью у тех, кто читал эту лекцию.
На рисунке 1.12 приведены графические зависимости величины адсорбции для двух примесей, отличающихся значениями b.
На рисунке 1.13 приведен пример современного оборудования для проведения процессов отмывки пластин.
Рисунок 1.12 – Изотермы адсорбции примесей 1 и 2
![]() |
Рисунок 1.13 – Установка финишной отмывки пластин
[VVB1]