Для студентов МГТУ им. Н.Э.Баумана по предмету Дипломы и ВКРВКР / Дипломная работа (Э-8) на тему "Разработка проекта плазменной установки для плавки металла с помощью плазмотрона на базе вакуумной камеры КС-411ВКР / Дипломная работа (Э-8) на тему "Разработка проекта плазменной установки для плавки металла с помощью плазмотрона на базе вакуумной камеры КС-411
2021-10-172021-10-17СтудИзба
ВКР / Дипломная работа (Э-8) на тему "Разработка проекта плазменной установки для плавки металла с помощью плазмотрона на базе вакуумной камеры КС-4110 "
Описание
Задание на дипломный проект:
разработать проект плазменной установки для плавки металла с помощью плазмотрона на базе вакуумной камеры КС-4110 и применительно к лаборатории кафедры Э8. Установка предназначена для исследования процессов в плазмотроне.
Исходные данные для проектирования:
Рабочее вещество-аргон;
Ток разряда: 1000 А;
Давление в камере 1..10 мм.рт.ст.;
Плазмотрон должен быть размещен в существующей вакуумной камере КС41110, с использованием, имеющегося в лаборатории обо-рудования, и привязан к системам новой лаборатории Э8.
Что в архиве:
![]()
Аннотация…………………………………………………………..………………….5
Введение………………………………………………………………………………...6
1. Конструкторская часть ……………………………..……………………...……16
1.1 Порядок запуска плазмотрона …………………………………..…………....17
1.2 Уменьшение износа катода за счет присадки бария ………………..17
1.3 Расчет основных параметров плазмотрона …………………………………..19
1.4 Расчет ресурса катода ………………………………………………………….23
2. Описание испытательного стенда………………………………………………24
2.1 Состав стендовой базы для испытания плазмотрона ..………………………24
2.2 Описание системы охлаждения вакуумной камеры………………………….25
2.3 Расчет охлаждения вакуумной камеры…………………………….................26
2.4 Описание системы подачи рабочего вещества…………………….................30
2.5 Описание системы электропитания и управления…………………………...31
3. Технологическая часть…………….……………………….……………………33
Анализ технологичности конструкции…………..………………………………..34
Обоснование выбора материалов…………………………………………….……35
Технологический процесс сборки плазмотрона ..………………………………..37
Контрольно-измерительные приспособления………………………….………..46
4. Промышленная экология и безопасность………………………………….…..48
Характеристика испытательного стенда с точки зрения
охраны труда……………………………………….…………….…………………49
Поражение электрическим током…………………….………………….………..49
Воздействие светового излучения плазмы…………………………….………….51
Воздействие шума……………………………………………………….………....52
Воздействие вибрации……………………………………………………….….….53
Основные направления решения вопросов электробезопасности………………56
Расчет защитного отключения.……………………………………….…………...57
5. Организационно-экономическая часть………………………………..……….60
Определение длительности и трудоемкости этапов создания установки……....61
Затраты на проектирование……………………………………………..................64
Затраты на изготовление…………………………………………………………...66
Затраты на испытания, доводку и исправление технической
документации…………………………………………………………..…………...68
Выводы ……………………………………………………………………….…….70
Список литературы………………………………………………………………….71
Приложения…………………………………………………………………………..72
Задание на дипломный проект:
разработать проект плазменной установки для плавки металла с помощью плазмотрона на базе вакуумной камеры КС-4110 и применительно к лаборатории кафедры Э8. Установка предназначена для исследования процессов в плазмотроне.
Аннотация.
Конструкторская часть данной дипломной работы включает в себя:
· разработку конструкции плавильного плазмотрона;
· расчет основных параметров плазмотрона;
· разработку экспериментальной установки;
· расчет системы охлаждения плазмотрона;
· схему вакуумной системы лаборатории;
· схему системы подачи газа;
· схему электропитания установки;
· схему системы управления.
В технологической части дипломного проекта приводится технологическая схема сборки плазмотрона и приспособление для контроля расположения отверстий фланца.
В экономической части дан расчет затрат на проектирование, изготовление и испытание лабораторной установки.
В экологической части рассмотрены потенциально опасные и вредные факторы и способы защиты от них, влияющие на персонал при работе на экспериментальном стенде и при изготовлении плазмотрона.
Плазменная плавка является вторым после электрошлакового переплава способом металлургической переработки материалов, который возник на основе процессов сварочной техники. В металлургии плазменная дуга применяется преимущественно для рафинирования металла и выплавки сталей и сплавов высокой чистоты и со специальными свойствами. Плавка ведется либо в охлаждаемом кристаллизаторе (непрерывный, точнее, полунепрерывный процесс), либо в керамическом тигле (периодический процесс). Косвенная плазма (плазменная струя) находит применение главным образом для обработки порошкообразных материалов, например, для термической диссоциации различных соединений и получения таким путем металлов из окислов, для синтеза тугоплавких веществ (нитридов, карбидов и т. п.) из элементов, для повышения температуры газа в металлургических агрегатах.
Особенности плазменной плавки. Плазменно - дуговая плавка обладает важными особенностями по сравнению с другими способами выплавки качественных сталей и специальных сплавов.
1. Плазменная плавка (в отличие от открытой дуговой и вакуумно-дуговой
плавки) характеризуется значительно большей стабильностью электрических параметров, что свойственно сжатой дуге. Это позволяет, в частности, получать более ровную поверхность слитка при плазменно-дуговом переплаве, благодаря чему во многих случаях отпадает необходимость в механической обработке слитков перед их ковкой или опрессовкой.
2. При плазменно-дуговой плавке можно применять различные газовые среды в камере печи (нейтральную, восстановительную, окислительную) и различные давления, как низкие, так и высокие.
3. Потери легирующих компонентов сплава (даже летучих) при плазменно-дуговом плавлении при атмосферном или повышенном давлении нейтрального газа в камере печи сводятся к минимуму, что является важным преимуществом в сравнении с вакуумными способами плавки, в которых эти потери составляют заметную величину. В то же время возможно дистилляционное рафинирование металла, если плавка ведется при пониженном (10-3 – 10-1 мм.рт.ст.) давлении в камере печи. Такой процесс в отношении удаления летучих вредных примесей и потерь па испарение основных компонентов сплава занимает промежуточное положение между плазменной плавкой при давлении аргона 1 атм. и плавкой в глубоком вакууме, отличаясь, однако, большей стабильностью режима и простотой осуществления.
4. Восстановительная или нейтральная атмосфера может применяться в комбинации с рафинирующим шлаком, что усиливает эффект рафинирования металла. При этом, в отличие от электрошлакового переплава, к шлаку не предъявляется требование высокой электропроводности.
5. Скорость плавления расходуемых электродов при плазменной плавке регулируется независимо от мощности плазменной дуги, что позволяет применять, когда это требуется по металлургическим соображениям, весьма малые скорости наплавления слитка, не снижая при этом теплового потока дуги на ванну, а также выдерживать ванну в жидком состоянии без подачи в нее электродного металла. Это расширяет возможности управления процессом кристаллизации металла и получения нужной структуры слитка.
6. В отличие от вакуумно-дугового и электрошлакового процесса можно переплавлять кусковые материалы.
7. Плазменно-дуговые источники энергии в комбинации с обычными металлургическими процессами и агрегатами могут существенно повышать их эффективность, как, например, при плазменно-индукционной плавке.
Плазменно-дуговые печи. Основными процессами, получившими аппаратурной оформление в виде промышленных или полупромышленных установок, являются: 1) переплав расходуемых электродов (или кусковых материалов) в водоохлаждаемый кристаллизатор (полунепрерывный процесс); 2) плавка шихтовых материалов в печах с керамическим тиглем; 3) индукционная плавка шихтовых материалов с дополнительным плазменным нагревом (периодические процессы).
Переплав расходуемых стержней или, как их обычно называют, электродов производится по схеме Института электросварки им. Е. О. Патона АН УССР (ИЭС) с несколькими плазмотронами и одним вертикально расположенным электродом (рис. 1) и по схеме Института металлургии им. А. А. Байкова АН СССР (ИМЕТ) — с вертикально расположенным плазмотроном и тремя расходуемыми электродами, подаваемыми горизонтально (рис. 2). Схема ИЭС позволяет плавить расходуемые электроды большого диаметра, что делает ее особенно пригодной для печей, предназначенных для крупномасштабного производства. Печи ИЭС действуют на ряде предприятий. Параметры печей этого типа приведены ниже. Печи УПП-3 и У-467 предназначены для выплавки слитков прецизионных и жаропрочных сплавов, У-400-для выплавки азотированных и специальных шарикоподшипниковых сталей в слитках малого веса, а печи У-550 и У-600 - для выплавки слитков специальных конструкционных сталей.
разработать проект плазменной установки для плавки металла с помощью плазмотрона на базе вакуумной камеры КС-4110 и применительно к лаборатории кафедры Э8. Установка предназначена для исследования процессов в плазмотроне.
Исходные данные для проектирования:
Рабочее вещество-аргон;
Ток разряда: 1000 А;
Давление в камере 1..10 мм.рт.ст.;
Плазмотрон должен быть размещен в существующей вакуумной камере КС41110, с использованием, имеющегося в лаборатории обо-рудования, и привязан к системам новой лаборатории Э8.
Что в архиве:
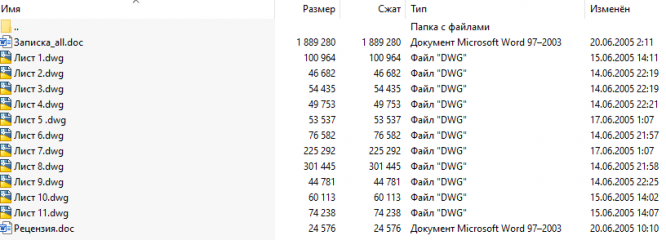
ОГЛАВЛЕНИЕ
Задание на дипломный проект.………………………………………………….......4
Аннотация…………………………………………………………..………………….5
Введение………………………………………………………………………………...6
1. Конструкторская часть ……………………………..……………………...……16
1.1 Порядок запуска плазмотрона …………………………………..…………....17
1.2 Уменьшение износа катода за счет присадки бария ………………..17
1.3 Расчет основных параметров плазмотрона …………………………………..19
1.4 Расчет ресурса катода ………………………………………………………….23
2. Описание испытательного стенда………………………………………………24
2.1 Состав стендовой базы для испытания плазмотрона ..………………………24
2.2 Описание системы охлаждения вакуумной камеры………………………….25
2.3 Расчет охлаждения вакуумной камеры…………………………….................26
2.4 Описание системы подачи рабочего вещества…………………….................30
2.5 Описание системы электропитания и управления…………………………...31
3. Технологическая часть…………….……………………….……………………33
Анализ технологичности конструкции…………..………………………………..34
Обоснование выбора материалов…………………………………………….……35
Технологический процесс сборки плазмотрона ..………………………………..37
Контрольно-измерительные приспособления………………………….………..46
4. Промышленная экология и безопасность………………………………….…..48
Характеристика испытательного стенда с точки зрения
охраны труда……………………………………….…………….…………………49
Поражение электрическим током…………………….………………….………..49
Воздействие светового излучения плазмы…………………………….………….51
Воздействие шума……………………………………………………….………....52
Воздействие вибрации……………………………………………………….….….53
Основные направления решения вопросов электробезопасности………………56
Расчет защитного отключения.……………………………………….…………...57
5. Организационно-экономическая часть………………………………..……….60
Определение длительности и трудоемкости этапов создания установки……....61
Затраты на проектирование……………………………………………..................64
Затраты на изготовление…………………………………………………………...66
Затраты на испытания, доводку и исправление технической
документации…………………………………………………………..…………...68
Выводы ……………………………………………………………………….…….70
Список литературы………………………………………………………………….71
Приложения…………………………………………………………………………..72
Задание на дипломный проект:
разработать проект плазменной установки для плавки металла с помощью плазмотрона на базе вакуумной камеры КС-4110 и применительно к лаборатории кафедры Э8. Установка предназначена для исследования процессов в плазмотроне.
Исходные данные для проектирования:
Рабочее вещество-аргон;
Ток разряда: 1000 А;
Давление в камере 1..10 мм.рт.ст.;
Плазмотрон должен быть размещен в существующей вакуумной камере КС41110, с использованием, имеющегося в лаборатории оборудования, и привязан к системам новой лаборатории Э8.Аннотация.
Разработка плавильного плазмотрона и установки для его испытаний
Цель проекта – разработать конструкцию плазмотрона на базе серийного плавильного плазмотрона ПТП-87, разработанного на Центроэнергоцветмет (отдел плазменной техники), по данным указанным в техническом задании, а также используя имеющееся стендовое оборудование лаборатории кафедры Э-8 спроектировать экспериментальную установку для испытания модели. В разрабатываемом плазмотроне использовать многополостной вольфрамовый катод с присадками бария.
Конструкторская часть данной дипломной работы включает в себя:
· разработку конструкции плавильного плазмотрона;
· расчет основных параметров плазмотрона;
· разработку экспериментальной установки;
· расчет системы охлаждения плазмотрона;
· схему вакуумной системы лаборатории;
· схему системы подачи газа;
· схему электропитания установки;
· схему системы управления.
В технологической части дипломного проекта приводится технологическая схема сборки плазмотрона и приспособление для контроля расположения отверстий фланца.
В экономической части дан расчет затрат на проектирование, изготовление и испытание лабораторной установки.
В экологической части рассмотрены потенциально опасные и вредные факторы и способы защиты от них, влияющие на персонал при работе на экспериментальном стенде и при изготовлении плазмотрона.
Введение
В конце XIX и начале XX столетия электрическая дуга получает промышленное применение в качестве источника теплоты для плавления металла в металлургии и сварке. Для металлургических целей создаются различные конструкции дуговых электропечей, и дуговая плавка открывает новую страницу в производстве качественных сталей и ферросплавов. И, наконец, в ответ на возрастающие требования к чистоте и качеству металла появляется вакуумно-дуговой переплав (ВДП), позволяющий устранить основной недостаток открытой плавки — взаимодействие расплавленного металла с атмосферой. В эти же годы бурно развивается дуговая сварка. Усиленно разрабатываются способы и средства металлургической обработки и защиты металла от воздуха в процессе сварки, способы повышения стабильности дуги, усовершенствуются способы управления дугой.
Плазменная плавка является вторым после электрошлакового переплава способом металлургической переработки материалов, который возник на основе процессов сварочной техники. В металлургии плазменная дуга применяется преимущественно для рафинирования металла и выплавки сталей и сплавов высокой чистоты и со специальными свойствами. Плавка ведется либо в охлаждаемом кристаллизаторе (непрерывный, точнее, полунепрерывный процесс), либо в керамическом тигле (периодический процесс). Косвенная плазма (плазменная струя) находит применение главным образом для обработки порошкообразных материалов, например, для термической диссоциации различных соединений и получения таким путем металлов из окислов, для синтеза тугоплавких веществ (нитридов, карбидов и т. п.) из элементов, для повышения температуры газа в металлургических агрегатах.
Особенности плазменной плавки. Плазменно - дуговая плавка обладает важными особенностями по сравнению с другими способами выплавки качественных сталей и специальных сплавов.
1. Плазменная плавка (в отличие от открытой дуговой и вакуумно-дуговой
плавки) характеризуется значительно большей стабильностью электрических параметров, что свойственно сжатой дуге. Это позволяет, в частности, получать более ровную поверхность слитка при плазменно-дуговом переплаве, благодаря чему во многих случаях отпадает необходимость в механической обработке слитков перед их ковкой или опрессовкой.
2. При плазменно-дуговой плавке можно применять различные газовые среды в камере печи (нейтральную, восстановительную, окислительную) и различные давления, как низкие, так и высокие.
3. Потери легирующих компонентов сплава (даже летучих) при плазменно-дуговом плавлении при атмосферном или повышенном давлении нейтрального газа в камере печи сводятся к минимуму, что является важным преимуществом в сравнении с вакуумными способами плавки, в которых эти потери составляют заметную величину. В то же время возможно дистилляционное рафинирование металла, если плавка ведется при пониженном (10-3 – 10-1 мм.рт.ст.) давлении в камере печи. Такой процесс в отношении удаления летучих вредных примесей и потерь па испарение основных компонентов сплава занимает промежуточное положение между плазменной плавкой при давлении аргона 1 атм. и плавкой в глубоком вакууме, отличаясь, однако, большей стабильностью режима и простотой осуществления.
4. Восстановительная или нейтральная атмосфера может применяться в комбинации с рафинирующим шлаком, что усиливает эффект рафинирования металла. При этом, в отличие от электрошлакового переплава, к шлаку не предъявляется требование высокой электропроводности.
5. Скорость плавления расходуемых электродов при плазменной плавке регулируется независимо от мощности плазменной дуги, что позволяет применять, когда это требуется по металлургическим соображениям, весьма малые скорости наплавления слитка, не снижая при этом теплового потока дуги на ванну, а также выдерживать ванну в жидком состоянии без подачи в нее электродного металла. Это расширяет возможности управления процессом кристаллизации металла и получения нужной структуры слитка.
6. В отличие от вакуумно-дугового и электрошлакового процесса можно переплавлять кусковые материалы.
7. Плазменно-дуговые источники энергии в комбинации с обычными металлургическими процессами и агрегатами могут существенно повышать их эффективность, как, например, при плазменно-индукционной плавке.
Плазменно-дуговые печи. Основными процессами, получившими аппаратурной оформление в виде промышленных или полупромышленных установок, являются: 1) переплав расходуемых электродов (или кусковых материалов) в водоохлаждаемый кристаллизатор (полунепрерывный процесс); 2) плавка шихтовых материалов в печах с керамическим тиглем; 3) индукционная плавка шихтовых материалов с дополнительным плазменным нагревом (периодические процессы).
Переплав расходуемых стержней или, как их обычно называют, электродов производится по схеме Института электросварки им. Е. О. Патона АН УССР (ИЭС) с несколькими плазмотронами и одним вертикально расположенным электродом (рис. 1) и по схеме Института металлургии им. А. А. Байкова АН СССР (ИМЕТ) — с вертикально расположенным плазмотроном и тремя расходуемыми электродами, подаваемыми горизонтально (рис. 2). Схема ИЭС позволяет плавить расходуемые электроды большого диаметра, что делает ее особенно пригодной для печей, предназначенных для крупномасштабного производства. Печи ИЭС действуют на ряде предприятий. Параметры печей этого типа приведены ниже. Печи УПП-3 и У-467 предназначены для выплавки слитков прецизионных и жаропрочных сплавов, У-400-для выплавки азотированных и специальных шарикоподшипниковых сталей в слитках малого веса, а печи У-550 и У-600 - для выплавки слитков специальных конструкционных сталей.
Рис.1
1-Электрод. 2-Плазматрон. 3-Слиток. 4-Источник тока.
Рис.2
1-Электрод. 2-Плазматрон. 3-Слиток. 4-Источник тока.
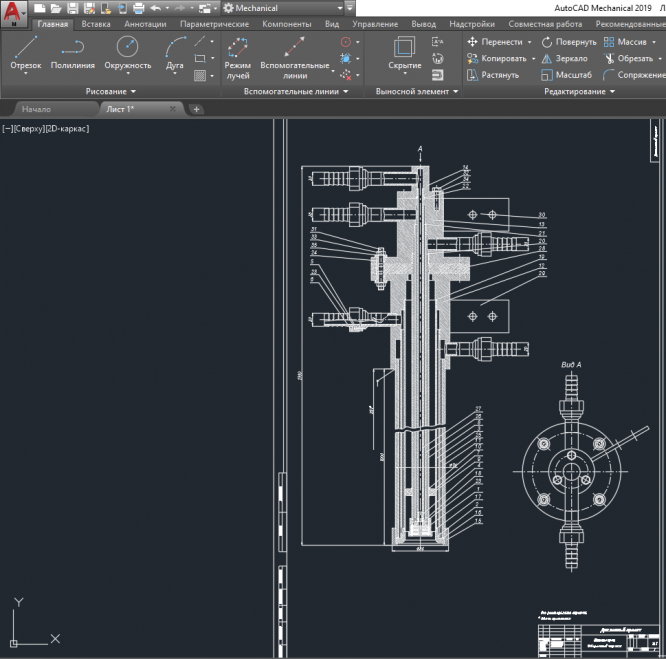
Характеристики ВКР
Предмет
Учебное заведение
Теги
Просмотров
38
Размер
2,86 Mb
Список файлов
Записка_all.doc
Лист 1.dwg
Лист 2.dwg
Лист 3.dwg
Лист 4.dwg
Лист 5 .dwg
Лист 6.dwg
Лист 7.dwg
Лист 8.dwg
Лист 9.dwg
Лист 10.dwg
Лист 11.dwg
Рецензия.doc

Ваше экономие времени является моей ГЛАВНОЙ задачей! Если я Вам хоть чуть-чуть помог, пожалуйста, сделайте и мне приятное, оставьте 5 ЗВЁЗД и позитивный комментарий. Большое спасибо!