Для студентов МГТУ им. Н.Э.Баумана по предмету Сопротивление материаловЗадача 3Задача 3
2013-08-252024-11-23СтудИзба
Задача 3 вариант 25
-40%
Описание
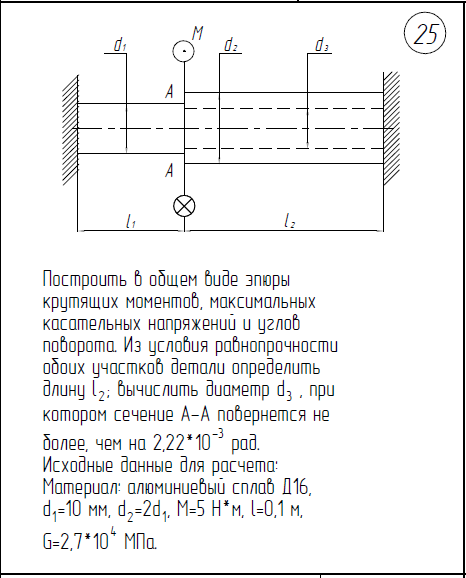
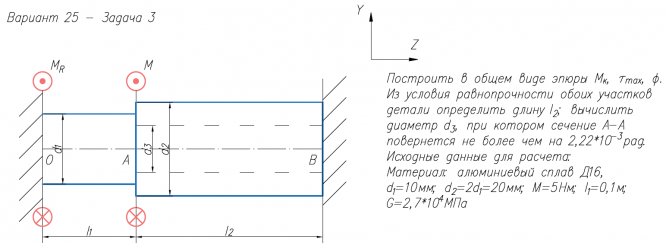
Построить в общем виде эпюры М/к, τ/max, φ. Из условия равнопрочности обоих участков детали определить длину l/2; вычислить диаметр d/3, при котором сечение А-А повернется не более чем на 2,22*10-3/рад. Исходные данные для расчета: Материал: алюминиевый сплав Д16, d/1=10мм; d/2=2d/1=20мм; M=5Нм; l/1=0,1м; G=2,7*104/МПа .
Характеристики решённой задачи
Предмет
Учебное заведение
Семестр
Номер задания
Вариант
Программы
Теги
Просмотров
439
Качество
Идеальное компьютерное
Размер
217,42 Kb
Список файлов
Вариант 25 - Задача 3.pdf

Вам все понравилось? Получите кэшбэк - 40 рублей на Ваш счёт при покупке. Поставьте оценку и напишите положительный комментарий к купленному файлу. После Вы получите деньги на ваш счет.